The first thing that comes to mind when speaking of ceramic is pottery, yet a wide range of industries rely upon this material and technique. The manufacturing of ceramic components has reached a major milestone with the introduction of ceramic 3D Printing and one company that distinguishes itself among others of the same range in this niche market is 3DCeram.
The company develops & commercializes a range of ceramic 3D Printers. It also supports customers throughout the value chain from CAD to the manufacturing of parts.
Founded in 2001, by Richard GAIGNON and Christophe Chaput, the company initially offered a manufacturing on-demand service with conventional manufacturing processes, before gearing product offering towards SLA 3D printing technologies.
Richard GAIGNON, our guest in this Opinion of the Week series, shares the company’s journey while laying emphasis on the importance of ceramic 3D printing in industries where it is not expected.
From manufacturing on-demand to the development of 3D printers
*Ceramaker is 3DCeram’s brand of 3D printers. The company’s portfolio of 3D printers includes the C100 EASY, the C3600 ULTIMATE as well as the famous C900 FLEX 3D printers.
“The C900 FLEX is our flagship machine. With a build plate of 300x300x100 cm, this 3D printer is suitable for serial production. Several options including the SAM (Small Amount of Materials) option have been developed for this machine. The SAM (Small Amount of Materials) option allows for a printing process with very little material. This makes it possible, for example, to qualify ceramics. We will continuously enhance this 3D printer. Its hybrid version can print up to 4 additional materials (polymer, metal or other ceramics) simultaneously. Some laboratories are using the C900 to develop their way to print metal while others have demonstrated promising results to print SiC (Silicon Carbide)”, explains the co-president of 3DCeram.
The C100 EASY (100x100x150 mm printing plate) is suitable for developing parts and/or qualifying the process before the transition to industrial Ceramakers*. The machine is acknowledged for its ability to produce small parts. The “C100 EASY and the C3600 ULTIMATE have to work in tandem to achieve the desired results in industrial production or mass customization. With the largest plate (600x600x300 mm) available on the Ceramic 3D Printing market, the C3600 ULTIMATE is the latest addition to our portfolio”, continues the co-president.
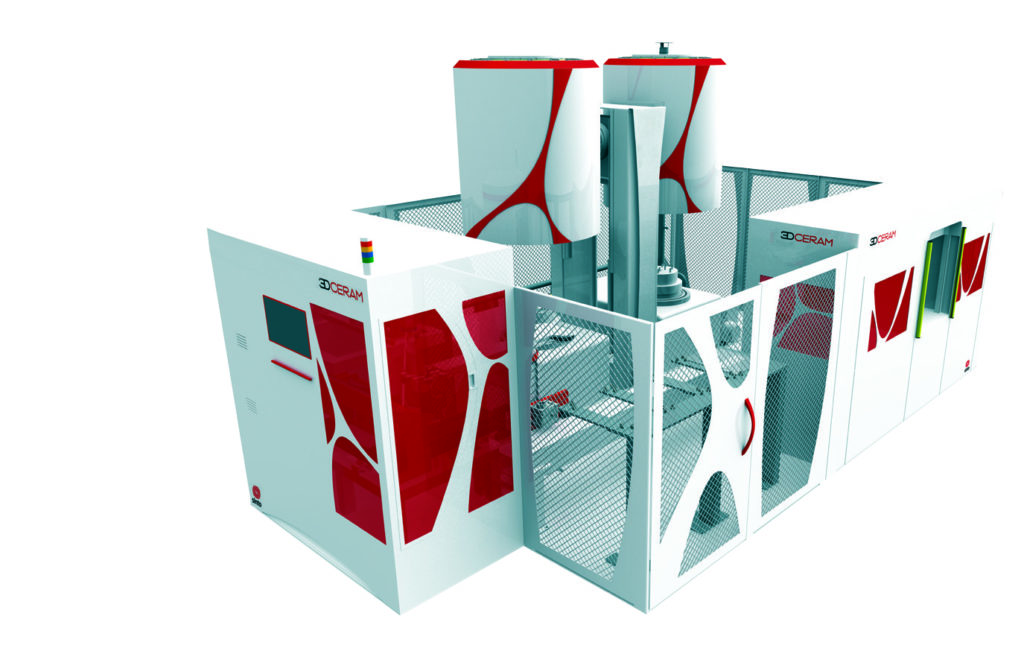
Choosing Stereolithography as a core technology
There are five main ceramic 3D printing processes on the market and 3DCeram has decided to bet on SLA. The flexible and easy to use technology allows for the development of new materials.
Over time, the French company has developed new solutions to improve the manufacturing process: “In post-printing, cutting support structures generates a high scrap rate. However, due to the development of our stripping support, we do not encounter such an issue with our technology. Indeed, during the printing process, the part is wrapped in an uncured “foam”, which is then easily cleaned. Easy to create, stripping support is simple to implement. Then come the debinding and sintering stages, which are required to achieve a perfect ceramic manufacturing process. At 3DCeram, we support our customers throughout the entire process up to the finished part. That’s why we also supply cleaning hoods and furnaces.
Furthermore, thanks to SLA technology, we have developed a “Free link” support technology that enables the manufacturing of 3D printing supports. The Free link support technology allows for the manufacturing of parts without leaving support marks and facilitates the baking process of the part. The risks of deformation during sintering are then controlled,” underlines Ricard GAIGNON.
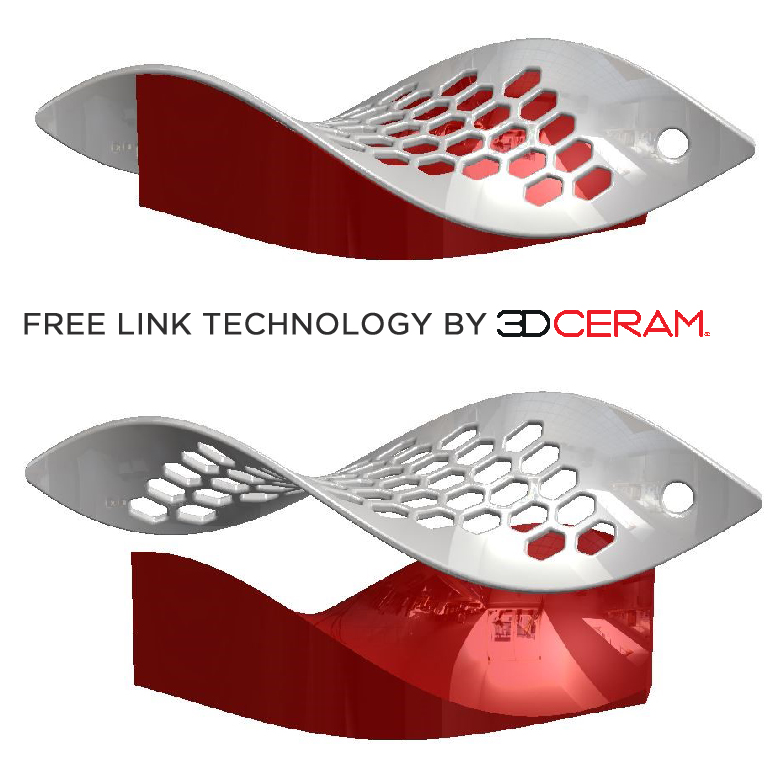
Applications of Ceramic 3D printing
As explained, Ceramic 3D printing is not just a matter of pottery. The manufacturing process is also leveraged in the electrical engineering, pharmaceutical, energy, automotive, medical as well as aerospace/aviation industries.
In the medical field, for example, we recently saw how the technology has accelerated the production of vaccines, or the fabrication of a ceramic cryotherapy probe to prevent breast cancer.
However, it should be noted that aerospace companies increasingly leverage ceramic 3D printing. According to GAIGNON, this market first “seeks to produce extremely high-performance parts with a lower weight. Technical ceramics, therefore, becomes an ideal material which delivers high-performance properties with good thermal and chemical stability“.
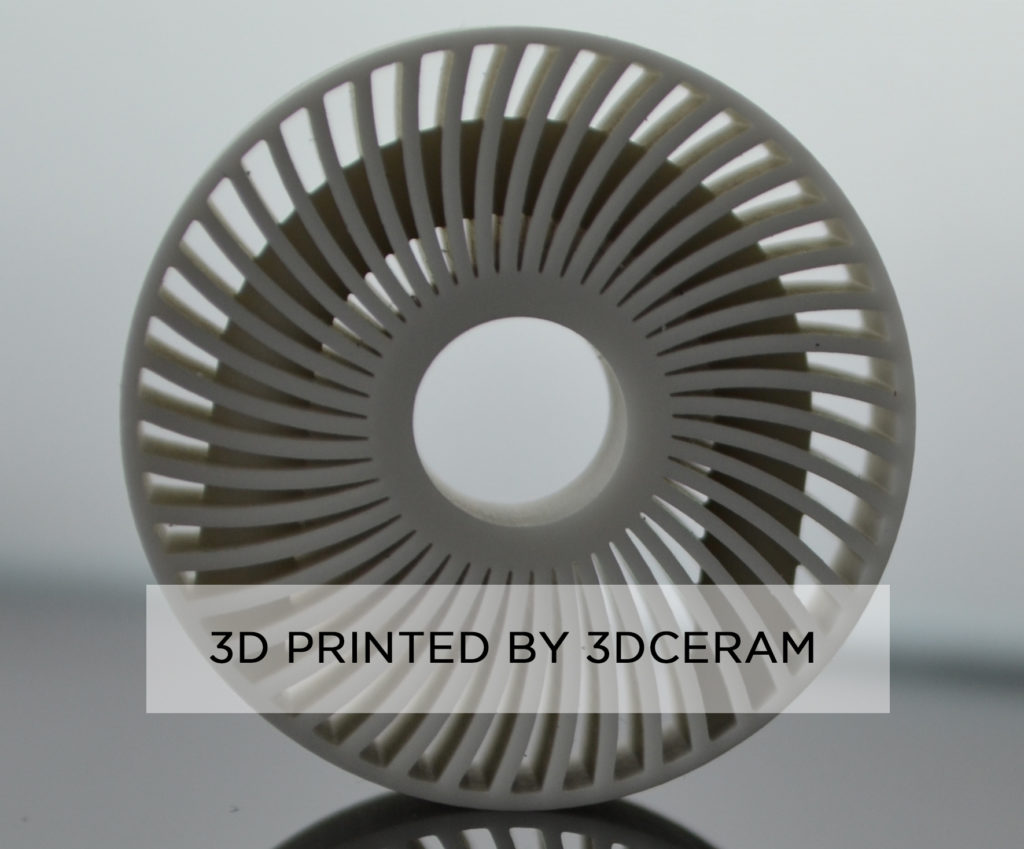
What’s next for 3DCeram?
Ceramic 3D printing is a manufacturing technology that is already well positioned on the market. However, due to the Covid-19 pandemic, companies were forced to reinvent themselves and to imagine new business models.
One thing everyone agrees on is local manufacturing and utilizing AM to produce locally has demonstrated, as per GAIGNON’s words, the flexibility, reactivity and agility of the technology.
“This period confirms our vision of considering AM as an industrial production tool which can complete traditional processes. In this regard, we are working on a new product offering.
This period has also changed our way of doing business. Digitalisation, on the other hand, has proved to be very useful and essential. Beyond the commercial aspect, it has become necessary to be “connected”.
In this industrial environment, 3D printing is more than ever a cutting-edge technology. Given the crucial role of digitalisation in such a manufacturing environment, 3DCeram will ensure support, maintenance and thorough customer service. We will also launch training programs to enhance the learning curve of our new and existing customers.
We aim to promote the integration of 3D printing in productive industries. Achieving this mission necessarily requires automation of processes. Once automation will be completely integrated and ROI (Return on Investment) will be determined, [3D printing] will bring its added value: mass customization” concludes GAIGNON.
Remember, you can post free of charge job opportunities in the AM Industry on 3D ADEPT Media or look for a job via our job board. Make sure to follow us on our social networks and subscribe to our weekly newsletter : Facebook, Twitter, LinkedIn & Instagram ! If you want to be featured in the next issue of our digital magazine or if you hear a story that needs to be heard, make sure to send it to contact@3dadept.com