With the Summer Olympic Games that are currently going on, we are currently discovering the means in which athletes have invested to prepare themselves for their various competitions.
At the heart of these preparations, one often finds the use of 3D printing or 3D scanning technologies to improve equipment’s performance for certain disciplines. One of these disciplines is cycling, a field where speed is everything.
With up to 90% of a cyclist’s energy output being spent to overcome air resistance, reducing drag is paramount. With the rider’s body being responsible for roughly 80% of the drag, and their bike the remaining 20%, it makes far more sense to focus on the rider, their biomechanics in various riding positions, their training, and especially, their clothing.
In this vein, sports performance brand Vorteq has worked with 3D scanner manufacturer Artec 3D to create custom-fitted aerodynamic skinsuits for cyclists.
Vorteq has designed what it describes as one of the “world’s fastest” cycling skinsuits. Their development requires the combination of Artec’s Leo 3D scanner, wind tunnels and engineering.
“Our mission is to help serious athletes, many of whom are already at the top of their game or near, find those many ‘tiny’ gains that when you add them all together, can really give an athlete the kind of edge that helps them surge over the top and on to victory,” said Sam Quilter, Metrology Engineer at Vorteq. “In contrast to our previous scanners, Leo gives us that flexibility to just pick up and go virtually anywhere in the world to do scanning, without requiring extra hardware, just the Leo itself.”
The sports brand would have invested an amount it has never invested in the past for the development of these skinsuits: $500,000 in R&D, while testing more than 45,000 different material, tension, and speed combinations in the specialized wind tunnels at Silverstone Sports Engineering Hub (SSEH).
The use of a 3D scanner – an Artec Leo – has been pivotal for digitally capturing a rider’s exact anatomy, and in the hours that follow those few minutes of scanning, all the sizes, patterns, and types of fabric have been meticulously selected in the computational draping system and then assembled by Vorteq’s skinsuit team.
According to Metrology Engineer Sam Quilter, “from the time an athlete walks in the door and we start scanning with Leo, then using Artec Studio to post-process the scans, followed by 3D modeling work in Geomagic Wrap, and finally exporting the 3D model for use in making a skinsuit, we are looking at about 2 hours total, which absolutely wasn’t possible in the past, not even close. And as far as the total production time for a skinsuit that’s ready to race, currently we’re at 2 days, but that gap is narrowing, and we’re shooting for a 24-hour turnaround time, which we’re sure to hit before too long.”
He explained his post-processing workflow in Artec Studio, “Leo makes it easy for me. Not many steps are needed in Artec Studio at all. I basically read the Leo data in, double-check everything visually, then use the Eraser tool for a few clicks to remove any occasional, unwanted bits. I normally keep the bike in the scan, since it’s a great reference point to get XYZ positioning as well as the angle, and then I go into Global Registration, where I just use the default settings because they work brilliantly as is. Normally I don’t need to do Outlier Removal, because the data is already clean enough for a person. Then I do a Smooth Fusion, and after a few other minor changes, I export it as an STL file for use in Geomagic Wrap.”
“In Geomagic Wrap, I use the Decimate tool to get the triangle count down further, and if I’m getting rid of any wrinkles, which shouldn’t be in the scan, but on a very rare occasion might be, I use the Relax command, and then I move on to the Smooth commands, which let me cut out any imperfections, because sometimes athletes twitch their fingers during the scanning, and we need to fix that. After we’ve done all we need to do, we export it as an OBJ file for use in our computational draping software,” Quilter said.
The Vorteq team thereafter uses the scans to scans to 3D print anatomically-precise mannequins of athletes. These mannequins are then used to create new skinsuits for the athletes without them having to visit the Vorteq office.
Speaking of the reasons that led to the fabrication of 3D-printed mannequins, Quilter said: “a full-sized mannequin lets us do wind tunnel tests on fabrics in isolation on just an arm, for example, to see how various fabrics and patterns affect drag reduction. That’s where the marginal gains really add up. Because with a live rider in the wind tunnel, there’s going to be the wiggle factor to deal with, where the rider is moving around, even ever so slightly, and that’s going to affect results. With a live rider, you can never have the exact measurement possible with a perfectly still mannequin, where the only factor that’s changed is the fabric that’s been put on. Mannequins don’t get tired, and they’re always perfectly still, which allows us to know exactly what kinds of changes our fabrics and designs are causing in terms of drag and performance.”
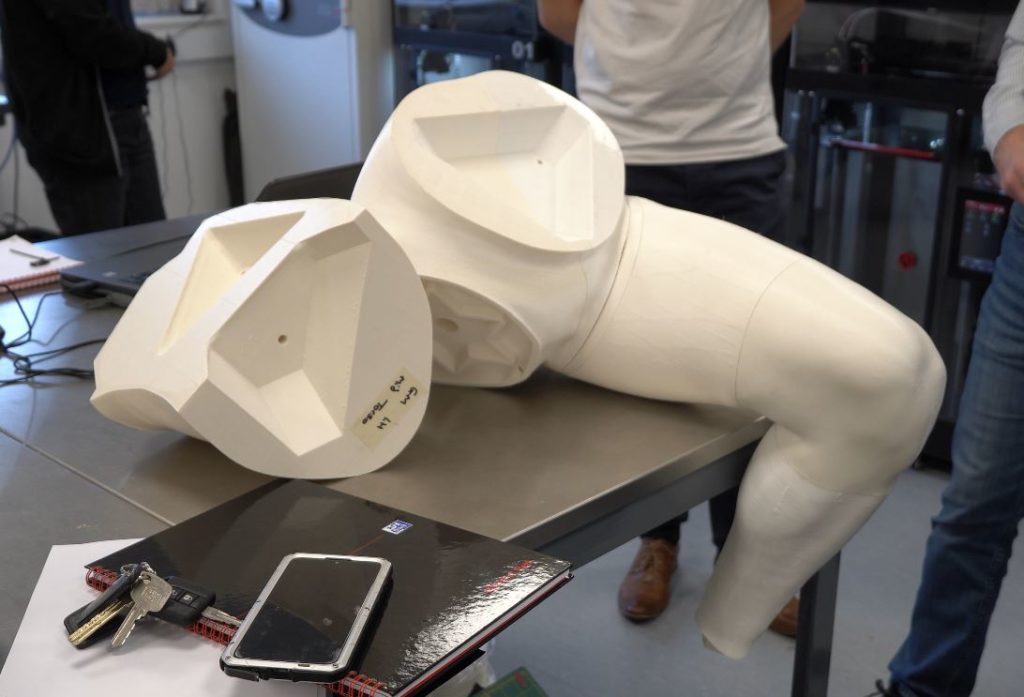
The skinsuits are currently being worn by five different Olympic athletes at this year’s Tokyo Olympics, and are designed to be lightweight, breathable, and significantly reduce drag.
Remember, you can post free of charge job opportunities in the AM Industry on 3D ADEPT Media or look for a job via our job board. Make sure to follow us on our social networks and subscribe to our weekly newsletter : Facebook, Twitter, LinkedIn & Instagram ! If you want to be featured in the next issue of our digital magazine or if you hear a story that needs to be heard, make sure to send it to contact@3dadept.com