It’s no secret that HIPing brought many benefits to the 3D printing industry, no matter the specific sector it is used in. Short for Hot Isostatic Pressing, HIP is a post-processing process used in additive manufacturing to achieve the maximum theoretical density and upgrade the fatigue resistance and ductility of high-performance materials. While HIP was used successfully to remove defects and eliminate pores in various materials, technology brought this process to the next step: optimized HIP for additively manufactured Titanium components.
Join us as we take a close look at this procedure that will take 3D printing to a whole new level, making it vital for applications where there’s no room for errors like the aerospace industry, Formula 1, car racing, and many others.
Combining Standard HIP with Elevated Temperature Treatment
The idea of obtaining additively manufactured grade 5 Titanium, or Ti6Al4V if you want to stick to its formula, has been around for quite some time. The benefits of getting a lightweight material with very robust characteristics can be a game-changer in many industries. However, it was only recently that the perfect combination of post-processing finishing was discovered to deliver excellent fatigue strength and a minimum standard deviation of mechanical properties.
As illustrated by Sauber Engineering, the key is combining Hot Isostatic Pressing, surface finishing, and Heat Treatment to obtain a robust production process and a final material with remarkable properties. The engineers at Quintus Technologies developed the High-pressure Heat Treatment process that combines standard HIP cycles and inert gas quenching to maximize fatigue strength and improve the manufacturing process altogether.
Minimizing Defects through HIP to Enhance High-Cycle Fatigue Strength
The main issue with additively manufactured components was their generally-lower fatigue resistance compared to components obtained through forging or other conventional processes.
Adding one layer after another, even with Titanium components, leaves for pores and micro-cracks to appear and considerably decreases ductility and fatigue resistance. However, multiple authors and researchers confirmed HIP’s successful use to eliminate internal defects and increase overall robustness, especially in Ti6Al4V. Using parameters like a 920°C temperature, 100 MPa pressure, and a 2-hour hold time dramatically increases the allowable stress from under 400 to over 600MPa.
Tackling the Ti6Al4V Softening at a High-Temperature Range
To further improve the static strength of L-PBF Ti6Al4V, scientists researched various values of heat treatment temperature levels. It is vital that the Titanium alloy is as fluid as possible for proper manipulation without losing its core values. Therefore, finding the proper temperature to soften it and cool it back was crucial. According to research such as the one done by G. Lutjerig, the martensitic phase decomposition starts at around 700-850 degrees Celsius. Maintaining these operating temperatures shown normal losses of yield strength compared to the forged Titanium components, as follows:
- Yield strength dropped from 1050 MPa to 950MPa at 700 to 800 degrees Celsius.
- A drop from 1050 MPa to 900 MPa at HIP temperatures of over 900 degrees.
To deal with the high-temperature deformation, the team from Quintus Technologies developed and implemented a low-temperature HIP cycle. This cycle was optimized to deliver the best results for the microstructure of the very fine L-PBF Ti6Al4V. This new cycle aims to minimize softening by reducing temperature but still compensate for this reduction by increasing the pressure during the HIP process.
Therefore, Quintus Technologies experimented with reducing the HP temperature from 920°C to 800°C and doubling the pressure from 100 to 200 MPa. Not only that doing so meant a more stable material with fewer pores and increased fatigue resistance, but complete full pore densification is achieved through this process. Furthermore, by increasing the pressure to 200 MPa, scientists also managed to retain a very fine lamellar microstructure for Ti6Al4V components, on top of compensating for the temperature decrease.
Obtaining Maximum Strength through High-pressure Heat Treatment
In some cases, applying a middle-temperature range HIP cycle can be very difficult or even unsuccessful. That’s especially the case when the defect size of L-PBF Ti6Al4V components is bigger than 300µm. This can happen especially when applying high-speed build parameters but in castings as well. To deal with these situations, Quintus Technologies came up with high-pressure heat treatment (HPHT). In other words, very high gas temperature and pressure values (similar to those used in high-pressure gas quenching – HPGQ) are used in a HIP furnace. Compared to conventional high-pressure gas quenching (done at around 15 bar), the density, heat capacity, velocity, and thermal conductivity values of the Ar gas used in HPHT are almost identical at 1500 bar. The increased pressure allows for a simultaneous HIP and solution-based heat treatment to take place.
Water, polymer, or oil can be used as solutions, and each comes with benefits for various industries. For example, when manufacturing components with thin cross-sections, such as body parts for F1 odds are that quenching them in polymer or water will lead to consistent pore formation.
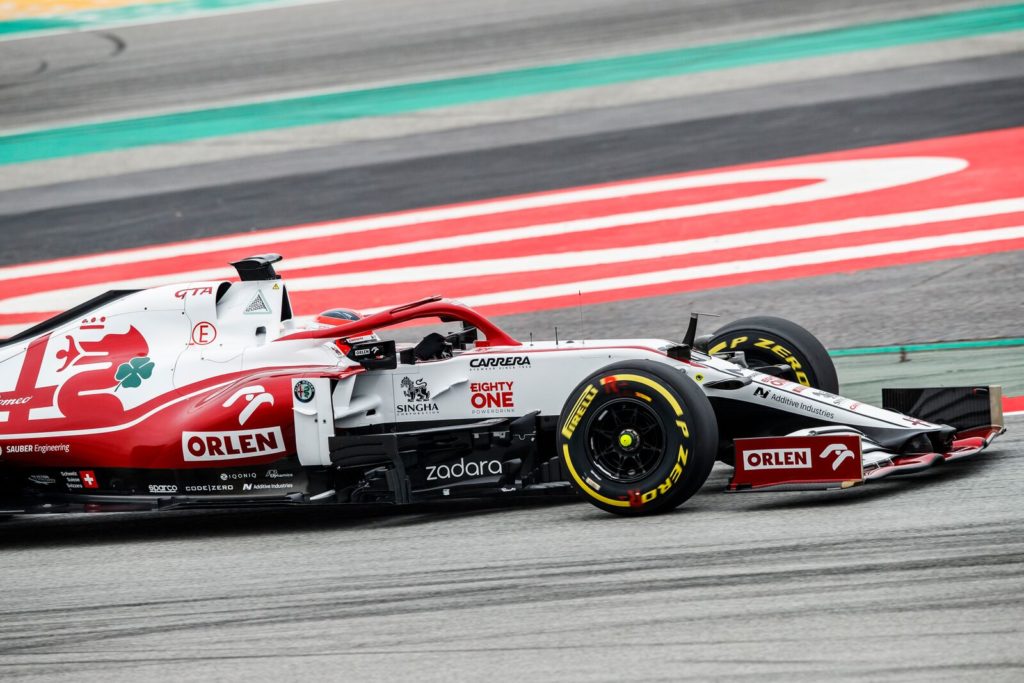
Application for HPHT on L-PBF Ti6Al4V for F1 Racing Car Cassis Inserts
What better example to illustrate the benefits of using HPHT on Ti6Al4V than Formula 1? This sport’s precision and extreme attention to detail make it excellent for showcasing the advantages of this method for processing Titanium components. Not to mention that every gram counts in F1, and relying on materials with excellent fatigue resistance that are also lightweight is vital. Using the re-engineered Titanium components lead to a weight loss of several hundreds of grams while maintaining the same strength and structural characteristics.
Around a dozen Ti6Al4V inserts are laminated into the chassis of F1 cars in vital force transmission points. These inserts play a very important role in the overall stiffness and handling of the car. With extremely thin sections of just 1mm, these inserts were ideal candidates for the use of HPHT-treated Titanium components. While there is still a lot of progress to be made, the high-temperature stress relief offered by HPHT combined with HIP processes shows a lot of potential for further use in F1.
Please share your thoughts in the comments below.
Featured image: Sauber Engineering.