Hager Group est un fournisseur de solutions et de services pour les installations électriques. La société couvre la distribution d’énergie électrique, les solutions de compteurs, des dispositifs de contrôle et protection, le cheminement de câbles et câblage, les systèmes d’automatisation des bâtiments ainsi que les dispositifs de sécurité tels que les alarmes et les détecteurs de mouvement et d’incendie.
Il y a environ 9 ans, la société dépensait encore environ 40 000 euros dans la production de ses pièces d’outillage chez des sous-traitants. En 2011, elle décide de se tourner vers l’impression 3D pour réaliser ses propres prototypes.
C’est ici que l’aventure commence…
Hager Group a environ 40 sites dans le monde et c’est Alexandre Callegher, Ingénieur en Fabrication Mécanique de la société basée en France – sur le site de Saverne, qui partage avec nous leur retour d’expérience sur le salon 3D Print.
Callegher explique que leur toute première imprimante 3D était une imprimante 3D FDM à 2000€ – dont on taira le nom ici – mais la première difficulté à laquelle ils ont fait face était le plateau chauffant qui était inexistant. De plus, l’imprimante nécessitait un gros travail de post-traitement, qui prenait énormément de temps.
Cette première expérience avait seulement confirmé une chose : ils avaient besoin d’une technologie d’impression 3D mais cette imprimante 3D FDM n’était pas la bonne technologie pour eux.
La société se tourne ensuite vers une technologie de FA de poudre qui est compliquée à utiliser car les opérateurs de la société n’obtiennent pas le support escompté.
De cette deuxième « mauvaise expérience », la société réalise ce dont elle a véritablement besoin pour réaliser ses prototypes : « on avait besoin d’imprimantes 3D « plug and play » capables d’assurer une stabilité dans le temps, et de créer des pièces complexes, fonctionnelles et légères de manière rapide et rentable à la fois. »
Et la technologie FDM de Stratasys entre en jeu…
Nous sommes en 2016 et Hager Group achète sa première imprimante 3D FDM Stratasys via le distributeur CAD Vision. Un investissement d’environ 45 000 € qui a permis à la société de produire à domicile l’équivalent de ce qu’ils dépensaient chez le sous-traitant en fabrication par usinage en un an, et de rentabiliser leur investissement dès la 2ème année d’utilisation.
La Fortus 380mc leur a permis d’exploiter des matériaux thermoplastiques de niveau industriel tels que l’ABS, le nylon, et le polycarbonate, sans compter le temps épargné au niveau des étapes de design. De plus, « imprimer les pièces en 3D nous a permis de réduire considérablement nos coûts de production par rapport à l’usinage en aluminium, mais aussi de réduire de 50% leur poids », explique Callegher.
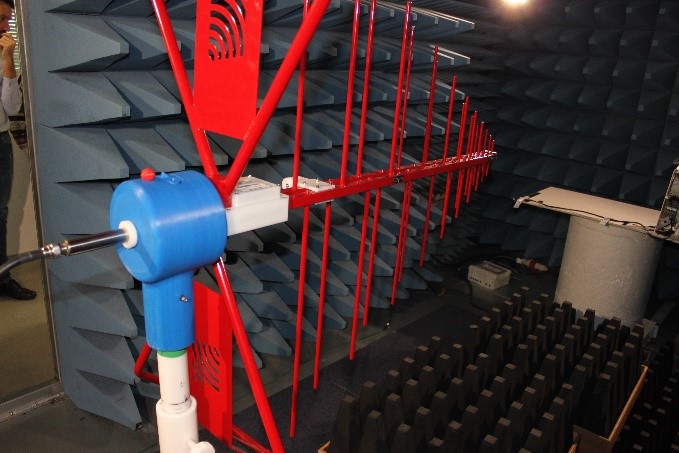
Aller encore plus loin
Callegher nous confie qu’ils vont aller encore plus loin que la simple production d’outillages. La société va commencer à commercialiser une petite série de produits avec des composants en 3D.
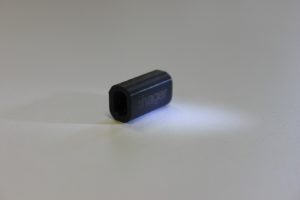
« Sur les deux années à venir, nous prévoyons d’imprimer en 3D 120 capuchons de petite taille avec un composant électronique fixé dedans avec une résine. Avant notre investissement, nous n’avions pas idée de ces avantages commerciaux. La fabrication additive de Stratasys nous a ouvert les yeux sur la façon dont nous pouvons entièrement déployer nos activités ici à Saverne, » conclut Callegher.
Il est maintenant possible de poster gratuitement des opportunités d’emplois dans l’industrie de la Fabrication Additive sur 3D ADEPT Media
Pour des informations exclusives sur l’impression 3D, abonnez-vous à notre newsletter et suivez-nous sur les réseaux sociaux !
Vous souhaitez-vous abonner à 3D ADEPT Mag ? Ou vous voulez figurer dans le prochain numéro de notre magazine numérique ? Envoyez-nous un email à contact@3dadept.com
https://pagead2.googlesyndication.com/pagead/js/adsbygoogle.js
(adsbygoogle = window.adsbygoogle || []).push({});