In an industry like Additive Manufacturing (AM), there are so many bright minds that it’s often a real conundrum to select who should be recognized for an “Innovators Award” – an AMUG award bestowed on those who have cultivated innovative ideas that have advanced the AM industry. Because AMUG is truly a one-of-a-kind event, the organization continues to reflect its dedication to one-of-a-kind innovators. This year, Greg Morris will be the recipient of this esteemed “Innovators Award”, and it took a conversation with him to understand his numerous achievements. Interestingly, that conversation goes beyond his journey to encompass the adoption of AM technologies across vertical industries and the future of Zeda.
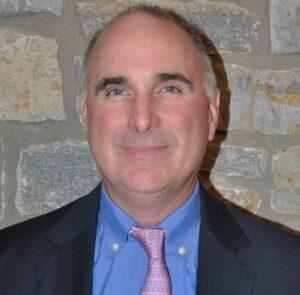
We’ve first known Morris as one of the five founders of Vertex Manufacturing, a company that merged last year with PrinterPrezz and now operates as Zeda. Actually, Morris is a man with multiple hats and it would probably require the whole chapter of a book to highlight them. The common thread among those hats is that they have always had a link with additive metals.
“When our company at the time, Morris Technologies, introduced laser powder bed fusion metal technology to the North American market back in 2003, I feel that we were fortunate to have been at the ‘right place at the right time’. We quickly realized this technology had a lot of promise, and we invested in it heavily over the years to follow. Fortunately for us, that ‘bet’ paid off in that the technology evolved and matured in such a way that we were able to work with our customers to use it for functional prototypes and eventually production parts. As many know, we worked closely with GE Aviation to develop the additive portion of their LEAP fuel nozzle tip. Once that was disclosed to the public, many other companies saw the potential and started to leverage the technology for their own products and purposes. With the development of more alloys, a much better appreciation of how to ‘design to the process’ and overall machine technology advancements, we have seen metal 3D printing become a potent tool for many companies looking to leverage the inherent benefits of design flexibility and freedoms for their products, helping to give products new capabilities, reduce costs and often alleviate supply chain constraints that have helped reduce lead times. Today, we continue to see not only technology advancements with many of these types of machines, such as multi-laser systems, enhanced machine and quality monitoring and many other such items, but we are also seeing a number of interesting metal modalities that are helping to address specific applications that also broaden the ability of engineers and designers to select the type of metal 3D printing that might best fit their applications and uses”, Morris told 3D ADEPT Media.
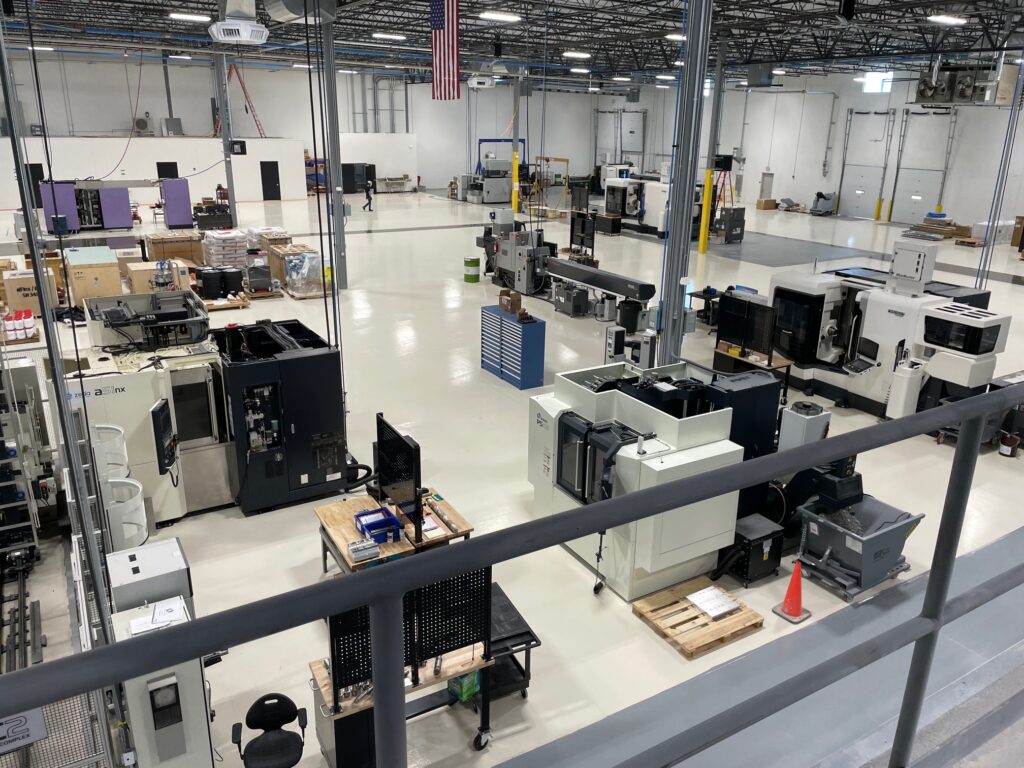
If this is only a small portion of a story that marked his journey, Morris recognizes that this story could not have been shared today without the many hands that joined forces to make it happen. To date, the man we first knew as the CTO of Zeta Technologies is transitioning into a more strategic role within the company while remaining an advisor to some small start-ups and companies.
The adoption of AM across the space, defense and aerospace industries
Vertex Manufacturing was one of the service bureaus that was bold enough to bet on Xerox ElemX™ 3D Printer – a liquid metal 3D printing technology that was still considered “new” in the market but apparently viable enough to 3D print aluminum consistently and reliably.
If we have always hoped that Vertex would make Xerox technology its secret weapon to drive AM across the space, defense and aerospace industries, Morris revealed that they started with a GE Additive LPBF machine and added a GE EBM technology after the integration of Xerox solution. It will therefore be no surprise to hear that LPBF was, is and will probably remain the primary technology driving the metal AM segment – at Zeda and for other AM users.
For our expert, there are metal AM technologies that are definitely a better fit than LPBF for certain applications. One such technology is binder jetting whose market shares are growing surely, but slowly. “While I would argue design differentiation can transform how one produces certain components, other factors have the potential to make larger impacts from a volume standpoint, such as cost per part. I think there are a variety of factors that hold back metal 3D printing from being more ubiquitous, with cost probably ranking as a primary one. Technologies like binder jetting and similar technologies can introduce both the design benefits of a layering process with throughput and thus cost competitiveness that technologies such as LPBF sometimes are not able to achieve yet,” Morris explains.
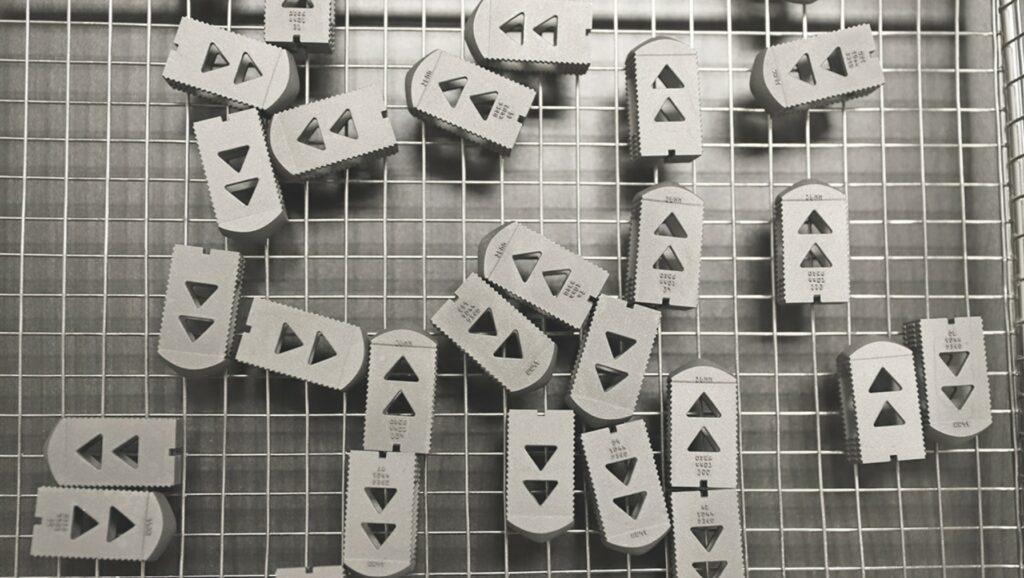
And when you add considerations related to materials, size of components and qualification of machines, one obtains the ingredients that could complexify the recipe to get parts for the aforementioned demanding vertical industries.
Far from being pessimistic, Morris focuses on the information we possess and how one can make the most out of it to grow:
- Given the fact that each metal AM technology has its own nuances and design requirements, one should recognize that it is very difficult to be an expert overnight in any of them, let alone multiple types of metal printing. As such, he outlines that the knowledge on how best to design a part with any particular technology in mind may not be as efficient as it might until either that experience is built up or additional tools become available that will help engineers and designers with a more ‘automated’ way of creating a part that will print well and that will achieve most of what they might want it to do.
- Be aware of promising materials and processes. Their advancements might be slow, but technologies and processes are being enhanced. Technologies that can produce larger parts efficiently with alloys such as Inconel, Copper and Stainless steel are gaining momentum. Among them, directed energy deposition (DED), friction stir weld (MELD) and others using emerging and novel ways of depositing and consolidating metal materials will be in demand for their speed and ability to deliver mechanical properties.
- Remain industry and application specific. For Morris, more efficient ways of producing additive parts (cost), faster lead times, and demonstrated and proven quality and material properties all play an important role in how quickly and deeply metal 3D printing is adopted into any industry, company or application.
The merger of Vertex and PrinterPrezz
If Vertex was acknowledged for producing parts for industries like space, defense and aerospace, PrinterPrezz was all about delivering a similar service to the healthcare and medical industries. We have always been intrigued by this merger as each of these companies operates in distinct fields of activity.
To this, Morris replies: “When discussions began around merging the companies, Vertex was a vendor to PrinterPrezz, providing post-machining and processing of titanium-produced implants that PrinterPrezz built. The synergy was combining both Vertex’s know-how and background of metal 3D printing as well as the capabilities and know-how of post-processing those metal 3D printed parts with PrinterPrezz’s desire to vertically integrate all of these capabilities. While Vertex indeed had more of a primary focus on aerospace, space and defense type parts, the ability to cross-pollinate learnings and know-how from these disparate industries was looked at as a strength.”
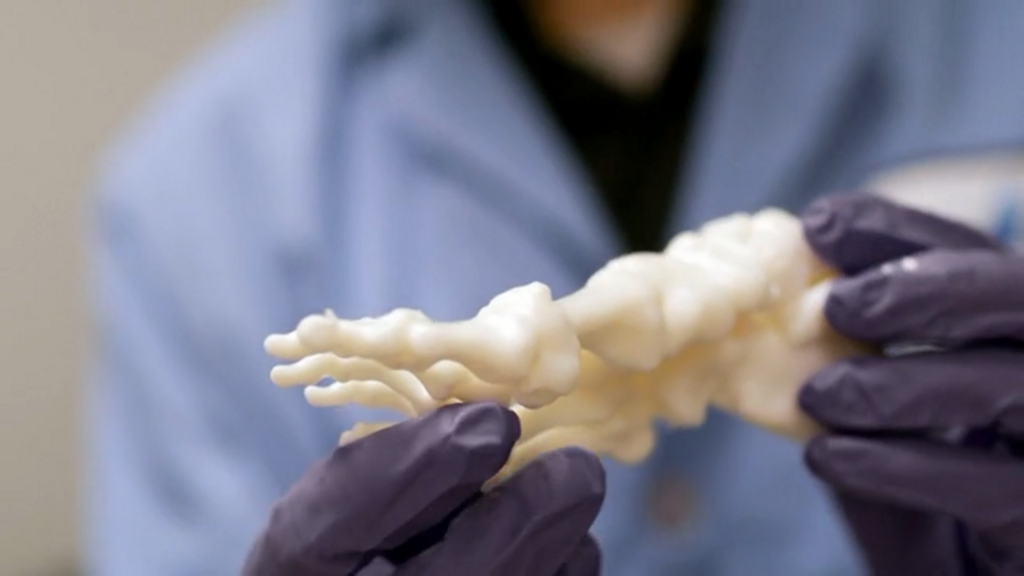
Speaking of the differences that set them apart in the use of AM technologies, he adds:
“PrinterPrezz had a pretty specific focus area printing for use in medical applications, whether that was for implants or instrumentation. Because of this, they worked pretty much exclusively with titanium and stainless alloys. They also had very specific post-build steps that were aimed at working with these types of smaller, industry-specific parts. Vertex, on the other hand, was more of a generalist, with a focus on aerospace, space and defense. To that end, Vertex worked with similar alloys as PrinterPrezz, but also produced parts in alloys more specific to other industries that desired nickel-based or other similar type materials. The post-build steps for Vertex also entailed having a broader range of capabilities simply based on the expanded needs being asked from these different customer types. Ultimately though, we find there are more synergies than differences in the various industry focuses.”
Moving forward, to drive the use of AM technologies across the aerospace, space and defense markets, Zeda, the company that combines Vertex and PrinterPrezz activities to date, will focus on the production of parts with alloys such as Inconel 718, copper with GrCop42, stainless steel such as 17-4 and 316 and aluminum.
To mark their willingness to continue focusing on the different sectors that were at the heart of Vertex and PrinterPrezz’s business, Zeda will have an entire division called Zeda Health which will soon be based out of Reno, Nevada, while the other side of the business will be the Zeda Technologies portion based out of Cincinnati.
“Both of these entities reside under Zeda Inc.. As the overall venture capital and private equity investment environment continues to improve, I believe Zeda will have the opportunity to attract the appropriate amount of capital to continue their growth into all of these markets,” Morris concludes.
Disclaimer: This interview was conducted as part of a media partnership with AMUG.