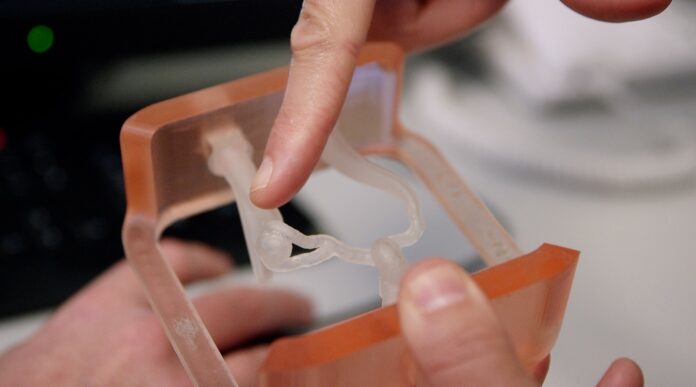
Elements healthcare providers should consider when getting into 3D printing and talking to 3D printing professionals
As pointed out in our conversation with Prof. Florian Thieringer (PP 10-12 of this issue), the learning curve of Additive Manufacturing (AM) is a tough path to follow because of several considerations that range from the required interdisciplinary expertise to cost considerations. Cost considerations highly depend on several factors that are often inherent to each hospital. These factors might include personnel, budget, or even the healthcare system within their country.
To optimize these costs and the use of their 3D printing equipment, some healthcare providers may rely on creative ideas that enable professionals outside of the healthcare field to benefit from the advantages of Additive Manufacturing.
The example of the France-based hospital CHU de Brest is one that’s worth mentioning here. The hospital’s use of AM as well as the coordinator’s profile clearly demonstrate that the use of 3D printing in a hospital is not limited to direct healthcare requirements.
Samuel GUIGO is the coordinator of W.PRINT, CHU de Brest’ 3D printing laboratory that integrates 7 FDM 3D printers, a resin 3D printer and a Polyjet machine. The laboratory is located just a few meters from the hospital, allowing users to directly come on-site, if need be. Guigo was previously a radiographer at the hospital. He seized the opportunity offered by AM to expand his scope of expertise to support other needs of the hospital. By brilliantly handling every task in the 3D printing lab (CAD, manufacturing, QA, communication, contract and more), he demonstrates that non-medically trained healthcare professionals can explore other career paths, thus creating a new path in their profession.
After the laboratory’s first 3D printing project in 2019 on an aneurysm case, the teams realized that 3D printing could be used on a broader scale for various applications such as the manufacturing of custom-made parts, anatomical models and much more.
“Our very first case led to the creation of a production unit in the hospital in order to provide custom-made services. I realized that a wide range of applications could help us make this service viable. These applications did not necessarily need to focus on surgery cases but can simply be a support that enhances the quality of life at work. The repair of non-critical biomedical parts, for instance, helps the hospital to save money when and where required.
That being said, healthcare applications remain the core of our expertise – whether we provide 3D printing services to other hospitals or for internal needs. We use AM the most to manufacture 3D-printed surgical guides that are used prior to the theatre room, 3D-printed models that serve an education purpose as doctors cannot train on patients, or even ultrasound models to teach young doctors how to cut an artery,” Guido told 3D ADEPT Media.
This conversation with Guigo also highlights the lack of information surrounding the first steps healthcare providers can take to get into 3D printing.
What are these steps?
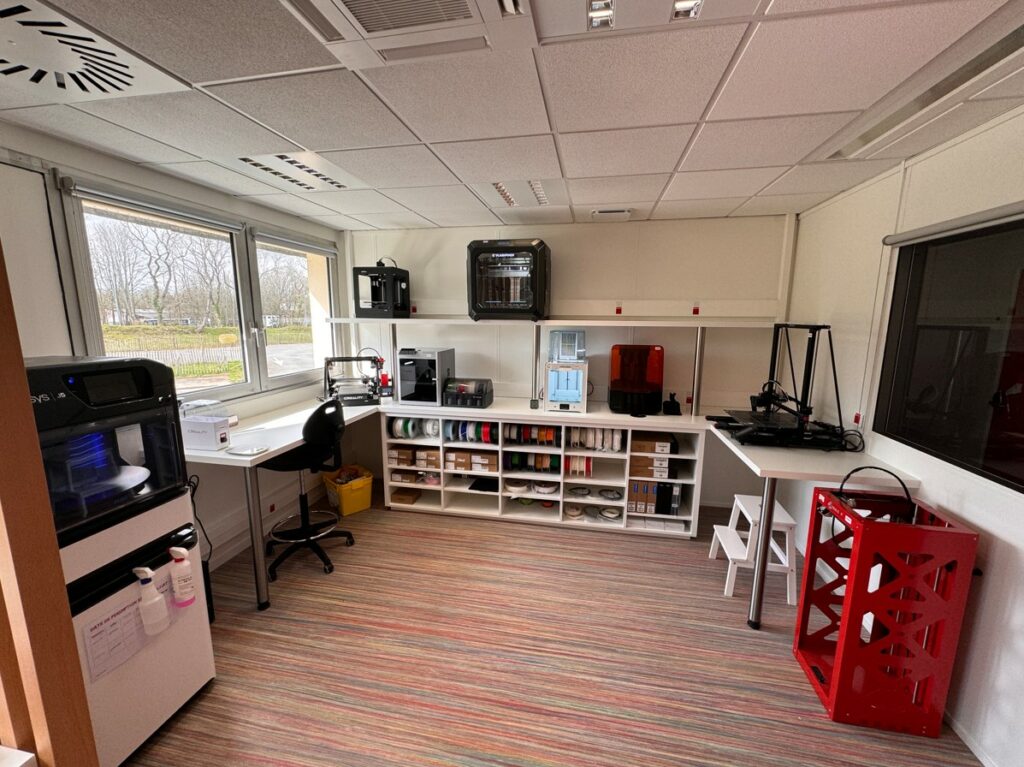
For those who are looking to integrate AM in the hospital, the 3D printing expert from CHU de Brest recommends “defining the different and specific needs in the hospital, gathering a small team and exploring both medical and biomedical applications in order to optimize costs.”
“Starting with simple cases studies is also a good way to get hands-on experience, or using open-source software to design models can be useful when you will be working with other first-time users. Most importantly, do not be afraid to reach out to other hospitals that are already quite advanced in their learning curve.
I also believe it is very important to have a guarantee of quality, i.e. an ISO-certified platform (for instance ISO13485). This is the next step in our development at W.PRINT as it is crucial to earn some legitimacy at both scientific and specialist levels,” he adds.
If investing right away in in-house equipment is not for you, then adjust your expectations, find, and talk to 3D printing service bureaus.
During your first conversation with a 3D printing service bureau, you should be ready to answer a couple of questions. We’ve identified 5 of the most important questions to keep in mind below :
- What’s the intended purpose of the model you want to produce?
The part’s function and how it’s going to be used are pivotal to think through the design, materials and other manufacturing requirements. As you may guess, a medical device that will be in contact with skin or bodily fluids will have stricter requirements that a non-medical part.
- For which volume production?
The answer to this question will help determine the AM process that will be used, the cost and eventually help to explore other manufacturing options. In the end, depending on the volume, maybe 3D printing will not be the ideal production candidate for your case.
- Are there any environmental considerations?
Answering this question will help in the selection of materials and other manufacturing requirements. Think of the different exposures the part may be subject to or may have to withstand: chemicals, liquids, temperatures, loads, etc.
- Are there any regulatory requirements?
As explained in the article “Approval of medical 3D printed products and their market access” (PP 5-8 of this issue), just because you can print it doesn’t mean you can use it. Therefore, be informed about the market access of your medical 3D printed products.
- Is there a desired price threshold?
Money is the sinews of war – even in the healthcare industry.
*Note: The conversation with Samuel Guigo has been edited for brevity and clarity. This article has first been published in the March/April edition of 3D ADEPT Mag.