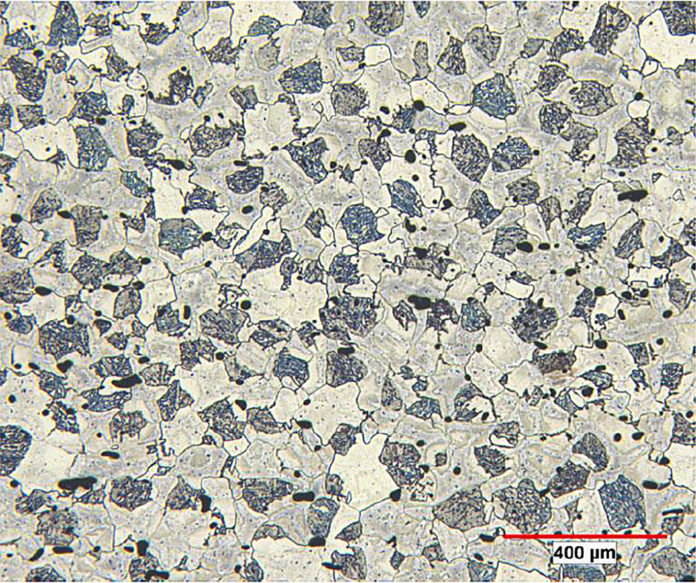
Digital manufacturer of advanced AM parts and materials for prototypes, GKN Additive, has improved one of the widely used low alloy dual-phase steel in the automotive industry. The material would be similar to DP600, which means, it could serve manufacturers’ efforts to reduce vehicle weight and improve crash performance.
With that ultimate goal in mind, and in an effort to constantly improve mechanical properties of materials that might enable to reach the aforementioned performance, parts’ producers have decided to focus on strength, weldability and spreadability while developing new alloys, which is exactly what GKN Additive did.
Named DPLA (Dual Phase Low Alloy) and FSLA (Free Sintering Low Alloy), the new metal powder materials developed by GKN Additive, deliver higher ultimate tensile strength (UTS) and low yield strength (YS) to UTS ratio, just like the DP600 (HCT600X/C).
While many could see the new materials as the transformation of the traditional automotive material DP600 (HCT600X/C) into two AM powders, GKN Additive goes beyond this simple adaptation by improving spreadability, laser absorption (Laser AM) and sinterability (Binder Jetting).
“Traditional DP600 offers specific standardized mechanical properties achieved by heat treatment. The dual-phase steel AM materials developed by GKN Additive on the other hand are very flexible in their characteristics, as their mechanical properties can be tuned more widely by the heat treatment after the laser or binder jetting process”, Christopher Schaak, Technology Manager for Binder Jetting at GKN Additive notes.
Designed to be processed by Laser Powder Bed Fusion (DPLA) and Binder Jetting (FSLA), the materials are ideal for applications that require to adapt the design of sheet metal parts, or to develop completely new structural components. However, while automotive customers are primarily targeted, it should be noted that other industrial sectors might also benefit from the new materials’ capabilities. Furthermore, those who are looking to achieve weight reduction of their parts, or to create new designs such as bionic structures might also see in these developments a great fit for their applications.
“With these AM processes, manufacturers in the Automotive industry can construct body parts differently than what was possible with traditional sheet metal parts. If you look at a tailored blank, many sheet- metal parts and support parts need to be formed and joined together to achieve a certain stiffness. By using structural components printed with AM on the other hand, you would need less process steps and less material, leading to cost optimization and a weight reduction”, explains Christopher Schaak.
That being said, a key area where we will see a wide range of applications performed with these new materials is the IDAM project, which aims to promote the “Industrialization and Digitization of Additive Manufacturing (AM) for Automotive Series Processes”. GKN shared first feedback of this project last year andalready assured thatseveral use cases as part of this project will see the use of these new materials.
“By using a subsequent heat treatment process to achieve the desired properties with the material within a wide range (medium to high strength properties), an AM provider can use an established printing process that does not need to be changed”, says Sebastian Bluemer, Technology Manager Laser AM at GKN Additive. “This allows streamlining of internal processes and enables a faster product delivery.”
This means that it will no longer be necessary to have the desired characteristics from a customer to develop and qualify a new material for the laser powder bed fusion or binder jetting process. GKN Additive is going to save a significant amount of time, since different mechanical properties could be achieved by varying the subsequent heat treatment.
“Our customers want to know what the new AM material can achieve in their respective use cases,” says Sebastian Bluemer, “and how it can be used. It’s faster to print parts with AM than to retool complete traditional production lines and manufacture the parts the conventional way. This means that AM is a good solution to quickly and functionally validate a material and a component, and to analyze faster and more efficiently, whether the material can help with a specific application or not.”
Remember, you can post job opportunities in the AM Industry on 3D ADEPT Media free of charge or look for a job via our job board. Make sure to follow us on our social networks and subscribe to our weekly newsletter : Facebook, Twitter, LinkedIn & Instagram ! If you want to be featured in the next issue of our digital magazine or if you hear a story that needs to be heard, make sure to send it to contact@3dadept.com