Aerodynamics (Aero) and Computational Fluid Dynamics (CFD) teams at GE’s labs in Niskayuna (New York) and Munich (Germany) are currently developing ways to speed up the process and take advantage of the 3D printing technology’s potential.
Waseem Faidi, manager of the additive research team for machine technology at GE Global Research who is leading the project, is talking about a strategy to accelerate additive manufacturing machines.
Stronger lasers could have worked but a wide range of variables needs to be taken into account: laser temperature, humidity, metal particle size and ambient gas flow.
“The question with 3D metal printers”, explains Faidi, “is how can I control gas flows in such a way that allows us to scale up the power of the lasers in the machine beyond what is possible today?”
Marshall Jones, one of the researchers at GE Global Research, set up a method for quickly welding metals that look alike.
Also, Jones found a way to make lead wires that are now used in light bulbs and some products.
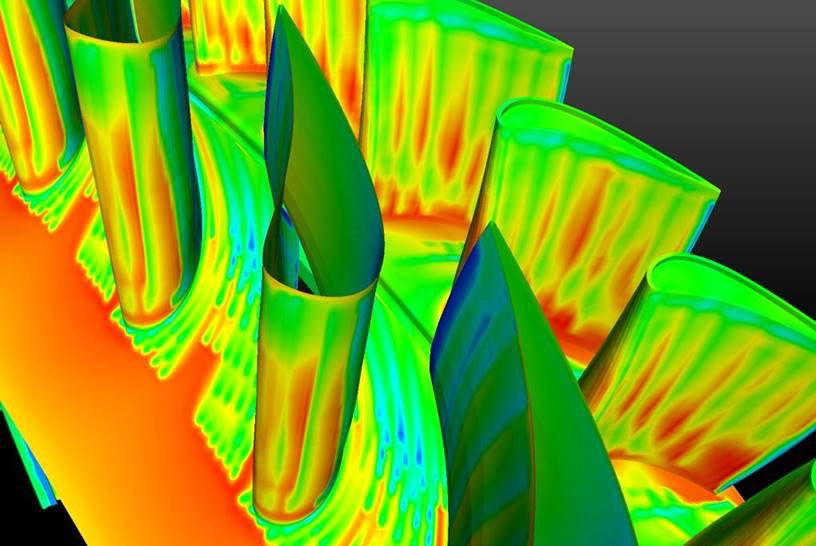
Finally, thanks to high-speed cameras and calculations’ simulation, researchers realized that the gas flow causes the “spatter” phenomenon that appears in the 3D printers’ build chamber.
For further information about 3D Printing, follow us on our social networks and subscribe to our newsletter!
//pagead2.googlesyndication.com/pagead/js/adsbygoogle.js
(adsbygoogle = window.adsbygoogle || []).push({});