2022 rings in a new era for Formula 1: cars are designed with new regulations in mind – which means further complexities for racing teams pursuing speed and reliability. While these regulations are engaging in various ways for racing engineering teams, it remains fascinating to watch the extreme applications in which newly created parts are being applied. 3D ADEPT Media sat down with Christoph Hansen, COO of Sauber Technologies, to discuss the additive production of these critical applications, and how these applications help Sauber Group build a technological expertise worthy to be explored beyond motorsports.
A lot can be said on Sauber Group, especially when we know that the company was founded in the 1970s and that from day one, the passion for racing has always been part of its DNA. What’s important to note in the context of the current Formula One season is that, after 25 years of competition in Formula One, its long-term partnership with Alfa Romeo in 2018 led the team to enter the 2021 championship under the name Alfa Romeo Racing ORLEN. As you may know, for racing teams to perform at their best, race and engineering must go hand in hand…And for an industry that was the first vertical to leverage AM, racing cannot be achieved today without advanced technological capabilities. A strategy that Sauber Group has well understood since the Swiss motorsport company has one of the largest AM production environments in its field of activity.
“We have the complete package when it comes to additive manufacturing capabilities:, 6 large SLS 3D printers, 7 SLA machines, 4 other metal 3D printers which are fully automated and therefore very productive. On top of this, we have an R&D department for materials development and validation. The production environment also integrates special units that help us make the right decisions when AM is leveraged. These units are completed by advanced heat treatment technologies such as Hot Isostatic Pressing (HIP) which are for instance, very useful for Titanium 3D printed components, etc. We operate this entire package under the umbrella of Sauber Group”, Hansen states from the outset.
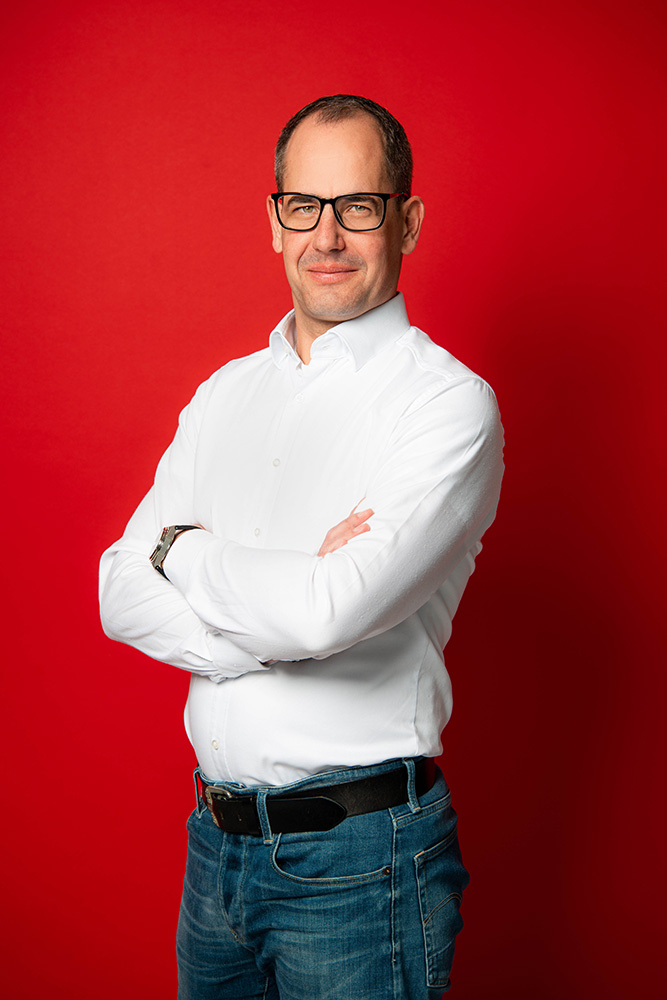
However, if the company seems to have a powerful machinery today, it should be noted they didn’t start investing in AM this way. As our guest told 3D ADEPT Media, Sauber Group started leveraging AM in the 1990s, but at this time, they were sourcing parts from an external supplier. “In 2007, we installed our first machine. It was an SLA 3D printer. And since then, we constantly increase our production capacity with other AM technologies. It’s only in 2016 that we decided to upgrade this production capacity with metal 3D printing which gave a huge boost to our business”, he adds.
Having a complete portfolio of AM & related processes is one thing, being able to make the most out of it is even better – especially in an industry where rules are ever changing.
New regulations in F1 and AM
The F1 2022 season officially started on Sunday March 20th in Jeddah Bahrain (GULF AIR BAHRAIN GRAND PRIX in the Middle East) – a chapter that Alfa Romeo F1 Team ORLEN writes with new drivers who recently joined the team: Valtteri Bottas and Zhou Guanyu.
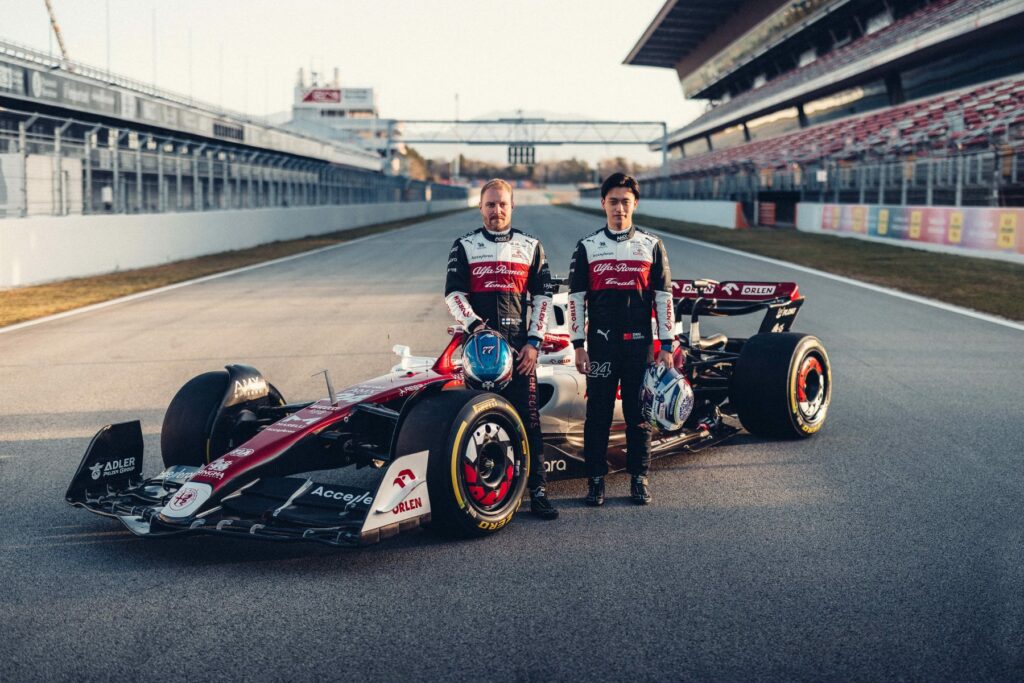
At the time we are having this conversation, Hansen expressed the team’s relief and satisfaction after months of pressure and preparation, which led them to a very good start into the competition. Indeed, Alfa Romeo F1 Team ORLEN opened its 2022 campaign with a strong performance that delivered a double points finish, with Valtteri Bottas finishing 6th ahead of team-mate, Zhou Guanyu, in P10.
“The pressure is off now. The past weeks were tough as we needed to get the car ready. A lot of emergency parts and other development parts needed to be done for the race car itself”, Sauber Technologies’ COO comments.
Behind the scenes of this magical performance, it should be noted that the new regulations have raised a number of challenges for engineering teams. One of the challenges was that regulations have inflicted a new design to racing cars, which means their aerodynamic performance was completely different than usual.
From a manufacturing perspective, these changes haven’t resulted in fewer aerodynamic applications for AM parts this year. However, the Alfa Romeo F1 Team ORLEN race car C42 includes more 3D printed parts in critical applications. The C42 is the first car the team built in this new regulations cycle. It is a radical departure from the past as it embraces the possibilities dictated by the new ground-effect floor, updated aerodynamic package and 18-inch (45cm), low profile tyres. Powered by a new Ferrari engine, this race car is designed to battle, as the new regulations will allow closer racing and competitive fighting from the front to the rear of the grid.
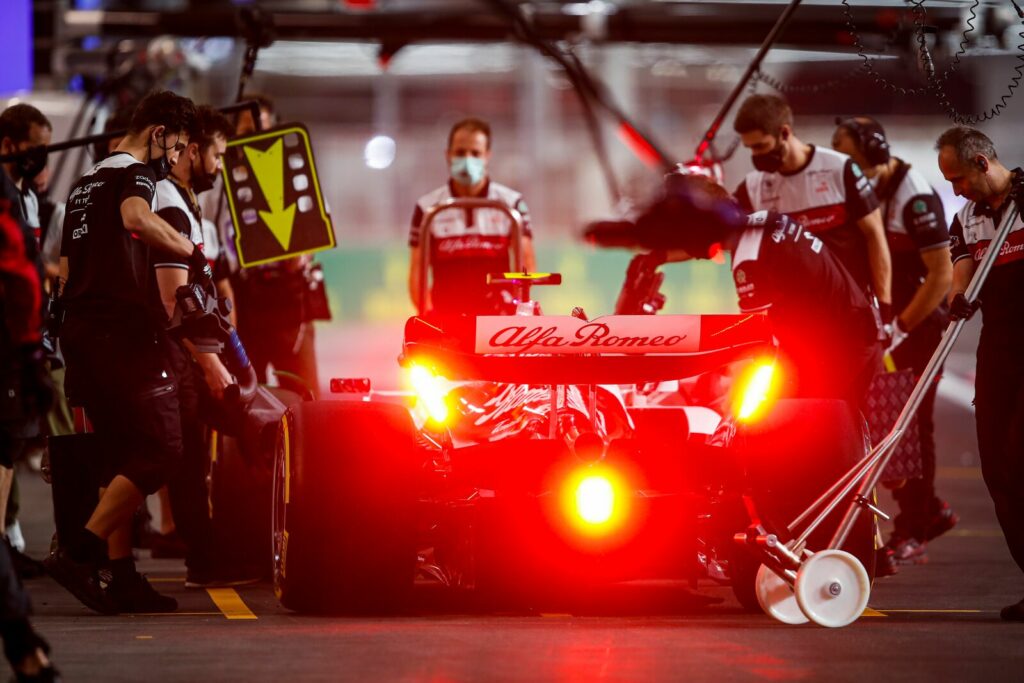
Speaking of Formula One in general, the main area where the use of AM is required is aero development – the wind tunnel models. The body of the wind tunnel models is essentially polymer parts and aluminium parts for the front and rear wings. This allows us to have very short iteration cycles, so we can develop the car very quickly. So the turnaround time from idea to design to production to testing is very short. In the early 1990s, when we started Formula 1, we used conventional manufactured components and it took weeks to get the expected results. With AM, the lead time has been reduced to a few days,” Hansen explains. “AM is also very useful for making components for the race car. These components include very sophisticated structural components for the chassis but also simple non-structural electronics boxes and equipment.”
Racing with Additive Manufacturing: the Alfa Romeo F1 Team ORLEN race car C42
Hansen said the Sauber team has additively manufactured between 300 and 400 parts for the C42. Around 150 parts out of this number have been 3D printed in metal.
The company representative did not elaborate on the exact areas where AM is used, but noted that these parts include safety-relevant structural parts where quality requires a high standard.
For every part produced, it is of utmost importance that the quality meets the high requirements. If this is not the case, it could have serious consequences for the pilot. To ensure this, we use technologies such as CT scans, so defects can be excluded. We also use hot isostatic presses to achieve the material properties. (etc.) All this ensures our technological edge.”, the expert outlines.
The chassis, which houses the driver and to which all components, assemblies and systems are attached, is usually made of a lightweight but very rigid honeycomb sandwich structure. Especially the inserts in the chassis – safety-critical class A parts – locally reinforce the composite sandwich panel. Depending on the function and load level, different materials can be used for the inserts, from carbon and aluminium to high-strength titanium for the Sauber C41 F1 racecar for instance, these Class A safety critical parts were produced with the Additive Industries MetalFAB1 system – using titanium (Ti6Al4V Gd 23) – to cope with the high fatigue and alternating loads experienced.
Furthermore, using 3D modeling and NonLinear Finite Element Analysis, Alfa Romeo also managed to iteratively reduce the weight of the 110 x 100 x 130mm inserts to just 580 grams, introducing undercut features into its design that weren’t constrained by the need to leave access for tooling.
While Sauber Group did not reveal any info yet on the production process of the C42, our guess is that the critical parts underwent a similar manufacturing process for the new car.
Additive Industries is Sauber Group’s metal Additive Manufacturing technology supplier since 2017. The long-standing partnership has enabled the Dutch OEM to play a pivotal role in the development and use of metal AM in the F1 car’s design, seeing its use significantly increase over the years. Today, Sauber Group has already produced over 50’000 metal laser PBF printed parts all industries included.
When asked why the focus on metal laser PBF when we know that not only weight is a decisive factor in racing car components, but it can also be obtained via other AM processes like composites AM, Hansen states:
“Composites 3D printing is still a compromise compared to the traditional composites materials. Even though we can achieve lightweight parts with this manufacturing process, having parts which are made up of Titanium or Scalmalloy® does not mean that the part is heavy. On the contrary, by using these materials, we can really achieve the lightest parts. These parts are usually replacing their counterparts we used to manufacture using conventional manufacturing processes. By comparing their weight with the one of their counterparts, we realize that we achieve lighter results with AM.”
Hansen’s answer steers the conversation towards AM materials. For SLS technology, Sauber uses its own HiPAC, a carbon-filled polyamide 12, while standard materials are used for sterolithography.
On the metals side, in addition to titanium, there are aluminum, stainless steel, and Scalmalloy®. The latter one is a recently-approved alloy by the FIA (Fédération Internationale de l’Automobile). Developed by APWORKS in collaboration with its parent company Airbus, Scalmalloy® comes with a very high tensile strength (UTS 520 MPa) and yield strength (480 MPa). Its low density provides the metal with specific properties which are above those of other aluminium alloys.
In the manufacturing value chain, it is no secret that materials are often the key item that hinders the scalability of AM applications hence the increasing development and qualification of new materials in the industry. In this case, although Titanium and Scalmalloy® are the main materials used for producing metal laser PBF printed parts of the C42, it’s interesting to note that Hansen is not in a hurry to explore new AM materials:
“I am happy with what we have right now. With the variety of materials, the complexity when it comes to achieving the required properties and quality, exploring other materials will only increase that complexity and will make it even more complex to maintain and ensure the mechanical properties. It’s also for these reasons that we work with a defined and limited portfolio of AM technologies as we need to make sure we maintain the quality we have right now. Sometimes, less is more.”
The next race?
Sauber Group has no intention to stop enhancing advanced manufacturing in MotorSports as its latest partnership with Camozzi Group illustrates. However, away from the track and thanks to its F1 expertise, the company has been silently building a legitimate place in the automotive 3D printing industry and beyond. It’s been a while that it has been providing other demanding industries with 3D printed parts and in 2022 the company takes a clear position with the creation of Sauber Technologies, a new company that aims to bring Sauber’s drive for cutting-edge innovation and Formula One mindset to business all over the world.
Sauber Technologies sees the incorporation of Sauber Engineering and Sauber Aerodynamics in a bid to strengthen services and the offer of know-how for customers across a wide range of industries. Sauber Technologies, part of the Sauber Group and based in Hinwil, Switzerland, will be fully focused on third-party business, providing a holistic service for complex engineering problems, from the idea stage to the finished products.
As Hansen said, the new company embodies the knowledge and expertise of 50 years of motorsport, matched with the latest technologies and a machine park second to none. Our staff can take care of every stage of any project, from the idea to the preliminary design, on to manufacturing and finishing of a product – in a wide range of industries.
“We have seen some of the practical applications of our expertise in recent months and we are excited about the new opportunities that await us in the future. We bring a cross-discipline approach to the table, allowing our customers to access processes and technologies in novel ways and bringing success stories from other fields into theirs. It’s a unique approach in this region and we’re ready to help our customers grow with our innovative mindset”, he concludes.
This content has first been published in the March/April edition of 3D ADEPT Mag. Remember, you can post job
opportunities in the AM Industry on 3D ADEPT Media free of charge or look for a job via our job board. Make sure to follow us on our social networks and subscribe to our weekly newsletter : Facebook, Twitter, LinkedIn & Instagram ! If you want to be featured in the next issue of our digital magazine or if you hear a story that needs to be heard, make sure to send it to contact@3dadept.com