« Fabrication de pièces à l’aide de moules imprimés en 3D ».
C’est probablement très culturel, mais j’ai grandi dans un environnement où on m’a appris que nos parents ont toujours raison – surtout les mères. Ils savent tout simplement ce qu’il y a de mieux. Imaginez ma surprise lorsque, à Formnext 2023, je suis tombée sur Foundry Lab, une entreprise suffisamment audacieuse pour affirmer haut et fort que « maman avait tort ». Bien sûr, je devais m’arrêter à leur stand pour leur dire qu’ils avaient tort d’affirmer une telle chose – quelle que soit leur raison – mais j’avais besoin de comprendre d’abord ce qui avait conduit à une déclaration aussi audacieuse. Cela m’a pris quelques mois et une conversation récente avec le fondateur et CEO David Moodie.
Nous avons peut-être découvert Foundry Lab l’année dernière, lorsqu’elle a fait ses débuts sur la scène européenne, mais l’entreprise a été fondée en 2018. Il s’est avéré que Moodie dirigeait un cabinet de conseil en design avant de fonder son entreprise et qu’il était frustré par leur capacité à prototyper uniquement des pièces en plastique et non des pièces moulées en métal.
« Mes clients se heurtaient à cette énorme lacune dans la fabrication – les pièces moulées sous pression sont impossibles à prototyper. J’étais frustré par l’impossibilité de tester nos conceptions dans le matériau de production – j’ai donc décidé de résoudre le problème moi-même », a-t-il déclaré.
Cela semble simple, mais ça ne l’est vraiment pas. Si j’ai été séduit par leur tactique de marketing, plus j’ai lu sur eux, plus j’ai trouvé matière à débat.
Que fait Foundry Lab ?
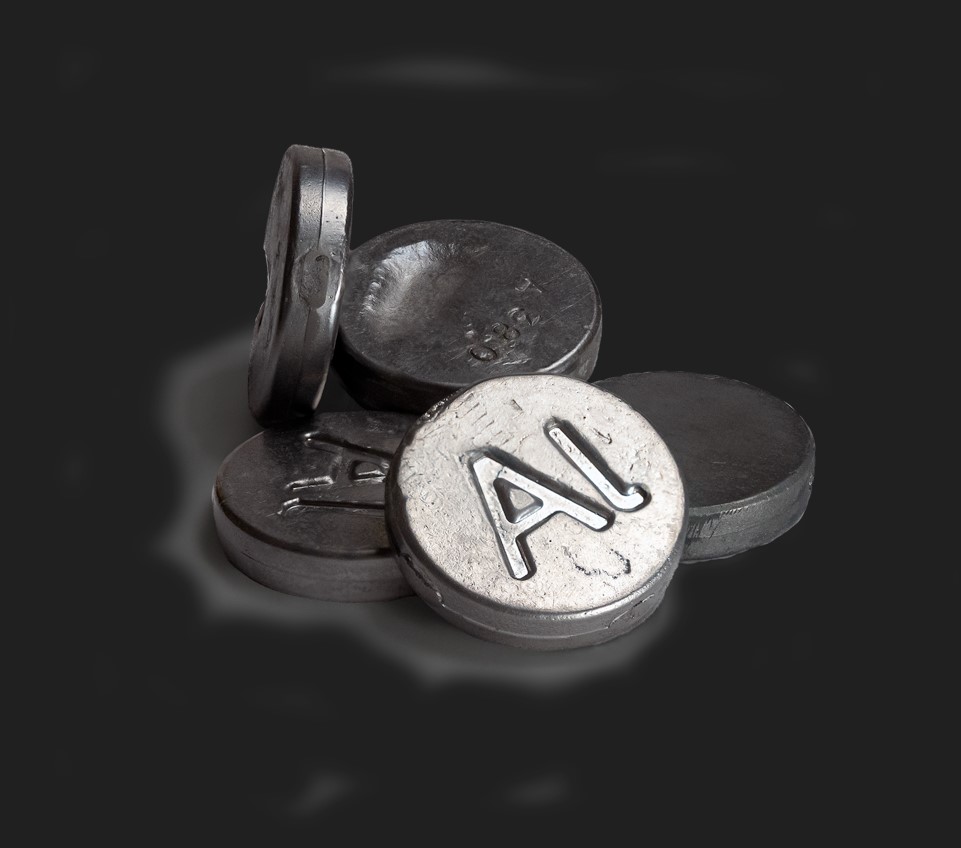
Pour faire simple, l’entreprise basée en Nouvelle-Zélande exploite les atouts du moulage traditionnel et les associe à la fabrication additive et à la technologie des micro-ondes pour produire des pièces métalliques.
Si j’ai bien compris, la réflexion stratégique de l’entreprise repose sur une dure réalité : il est difficile, voire impossible, d’imprimer en 3D une pièce de fonderie. Et surtout, il ne faut pas confondre cette dernière avec une pièce métallique, car il s’agit de deux choses différentes.
Pour combler le fossé entre le moulage et l’impression 3D, l’équipe a mis au point une solution appelée « Digital Metal Casting ».
Moodie explique le fonctionnement de cette solution : « Nous abordons le moulage de manière un peu différente : nous imprimons des moules en 3D dans une poudre de céramique, nous insérons un morceau de métal dans le moule, puis nous chauffons le moule. La pièce fond et remplit la cavité. Le résultat est un moulage avec le même alliage et la même géométrie que votre moulage de production ».
La controverse pourrait survenir lorsque Foundry Lab a déclaré « Arrêtez d’imprimer des prototypes ». Un point que le fondateur clarifie : « Nous disions essentiellement que si vos pièces sont destinées à être coulées en production, elles devraient être coulées en prototype. Les pièces métalliques imprimées ont la même couleur qu’une pièce moulée, mais c’est à peu près tout. Vous ne pouvez pas obtenir les données dont vous avez besoin à partir d’une impression ».
Comment cela fonctionne-t-il ?
La première explication que m’a donnée Hester Tingey (responsable marketing de la société) à Formnext révèle un processus en quatre étapes qui comprend : une imprimante 3D basée sur la projection de liant, une station de dépoudrage et un four à micro-ondes – le tout fonctionnant avec une solution logicielle dédiée ; tous ces éléments sont fournis par Foundry lab.
L’imprimante 3D fabrique un outil dans une céramique exclusive en utilisant un agent liant exclusif. Cette pièce subit un processus de durcissement par micro-ondes avant d’être dépoussiérée.
Le processus de moulage des métaux est réalisé sans qu’il soit nécessaire de verser du métal en fusion. Le métal solide, sous la forme d’un médaillon en forme de disque de Foundry Lab ou de toute autre pièce solide, est placé dans le moule, qui dispose d’un réservoir pour contenir cette matière première. Le four à micro-ondes ne fait pas fondre directement le métal, mais chauffe le moule en céramique à une température qui fait fondre le métal. Le métal en fusion s’écoule dans le moule, se solidifie en une pièce moulée et nécessite ensuite l’élimination de l’excès de matière, comme la bavure, comme pour tout autre moulage.
L’ensemble du processus présente cinq avantages principaux que Moodie énumère ci-dessous :
- Des pièces moulées de qualité sans aucune connaissance en matière de moulage.
- Nous avons constaté que le marché de la fonderie aux États-Unis et dans l’Union européenne est en plein essor, mais que les fonderies continuent de fermer. Le problème est que nous avons perdu la main-d’œuvre possédant les connaissances techniques nécessaires pour travailler dans la fonderie. L’objectif de Foundry Lab est de numériser la fonderie, afin de permettre à un opérateur non formé de réaliser des pièces de qualité.
- Sécurité : Le moule entre dans le four à froid et en ressort à froid. Il s’agit d’un moulage sans intervention. Il s’agit d’un changement de paradigme : on passe d’une fonderie sombre, avec du feu et de la fumée, à un environnement de salle blanche.
- Toute géométrie : En numérisant la fabrication du moule (impression 3D), nous disposons d’une liberté géométrique totale. La façon dont nous coulons permet également d’obtenir des parois minces – nous pouvons donc réaliser tout ce que la coulée sous pression aurait pu faire – sans la pression, les moules en acier ou les experts en coulée.
- Rapidité : le système peut produire une pièce en moins de 24 heures. Les pièces sont coulées dès le lendemain. (par rapport aux 6 à 18 mois dont dispose actuellement l’industrie).
- Coût : Il s’agit d’une question complexe – ce système est beaucoup moins cher que le moulage pour les petites séries. Il y a une corrélation lorsque les quantités sont plus importantes. Mais le coût initial de l’outillage est ce qui empêche les prototypes et les petites séries d’être coulés. En ce qui concerne les domaines susceptibles d’être améliorés dans ce processus, le fondateur mentionne des tailles plus grandes et des alliages à plus haute température – deux éléments que l’entreprise est en train d’améliorer.
Applications clés
« Nous avons déjà des pièces sur des voitures, sur la route !La raison en est que les pièces sont fonctionnellement équivalentes aux pièces moulées de production.Les applications que nous voyons actuellement sont la R&D en fonderie, la production de pièces anciennes sans requalification (résilience de la chaîne d’approvisionnement) et les courts tirages/passerelles entre les essais et la production de masse », a déclaré Moodie à 3D ADEPT Media lorsqu’il a été interrogé sur les applications clés qui démontrent le potentiel de leur technologie.
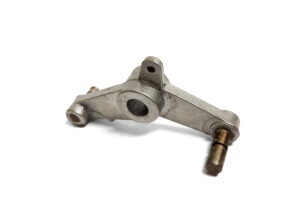
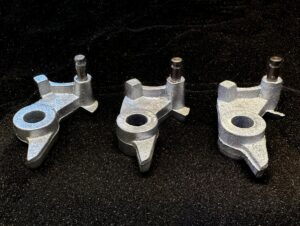
En outre, le développement d’applications est favorisé par les collaborations industrielles et le développement de Foundry Lab ne fait pas exception à cette règle. L’un des efforts de développement qui mérite d’être mentionné est celui de la société mondiale de gestion de l’énergie Eaton, qui s’appuie sur le système numérique de coulée des métaux pour couler des pièces en aluminium en quelques semaines plutôt qu’en quelques mois.
Ces pièces comprennent des broches en acier inoxydable et sont décrites comme « une avancée technologique qui n’est pas possible avec l’impression 3D traditionnelle ».
« Eaton est souvent confronté au défi de l’application de la fabrication assistée par ordinateur à des applications existantes parce que le changement de processus et/ou de matériau constitue un obstacle technique trop important », déclare Cameron Peahl, responsable de la fabrication additive au centre d’excellence de fabrication additive d’Eaton. « Dans cet exemple, la technologie de Foundry Lab nous permet de tirer parti de la vitesse et de la souplesse de la fabrication additive tout en conservant la méthode et le matériau de coulée conventionnels, y compris la goupille en acier coulée sur place. Il s’agit d’une avancée considérable dans notre parcours en matière de FA. »
Conscient que l’objectif de la plupart des utilisateurs est de parvenir à une production en série et en masse, Moodie confirme qu’ils « ne veulent pas rester bloqués là où l’impression 3D se trouve actuellement ». « Nous nous concentrons sur la production – c’est ce qui est nécessaire pour combler le déficit de capacité dans l’industrie aujourd’hui. »
Toutefois, dans l’intervalle, les étapes à court terme de l’entreprise consistent à achever la numérisation de l’ensemble du processus de coulée et à qualifier tous les alliages de coulée clés pour permettre au système de s’intégrer parfaitement dans la fabrication.
Ce dossier a été initialement publié dans le numéro de Mai/Juin de 3D ADEPT Mag.