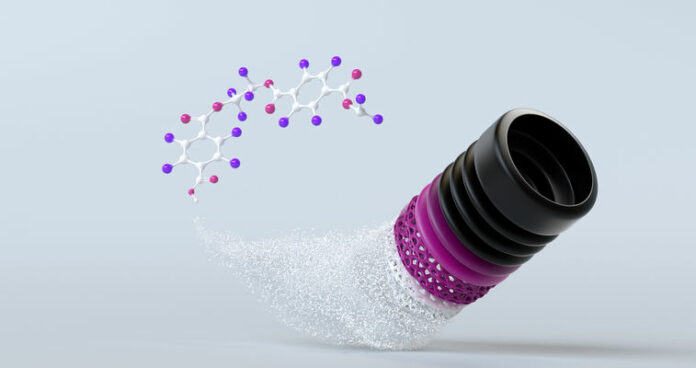
The time I have already spent in this industry makes me realize that the power of an additive manufacturing process lies in its ability to transform a material. This is in any case what is usually demonstrated in almost all the applications that are highlighted across industries. Today, with the growing popularity of 3D printing for manufacturing all sorts of items, material producers have a lot of work to do as they need to deal with new industry trends, qualification and certification. We caught up with Evonik’s Head of Additive Manufacturing Innovation Growth Field, Dr. Dominic Stoerkle, to discuss the development of materials in line with these stakes and how they interplay with automotive 3D printing applications.
The more AM is being challenged to foster industry 4.0, the more it raises debates in the way products are manufactured. In our still maturing industry, the technology increasingly holds promises for green benefits.
For example, at the production level, social, economic and environmental incentives drive the additive production with local feedstocks without the need for machining and numerous steps. At the device level, the newly fabricated object delivers new properties and optimized functionalities and at the material level, the focus is made on the use of AM with lower waste generation. The thing is, these advantages seem to be the ideal way to go for those who manufacture end-user products, locally. At an industrial level, we are still far from an ideal world given the various elements that need to be taken into account. That’s anyway what Evonik’sDr. Dominic Stoerkle draws our attention to:
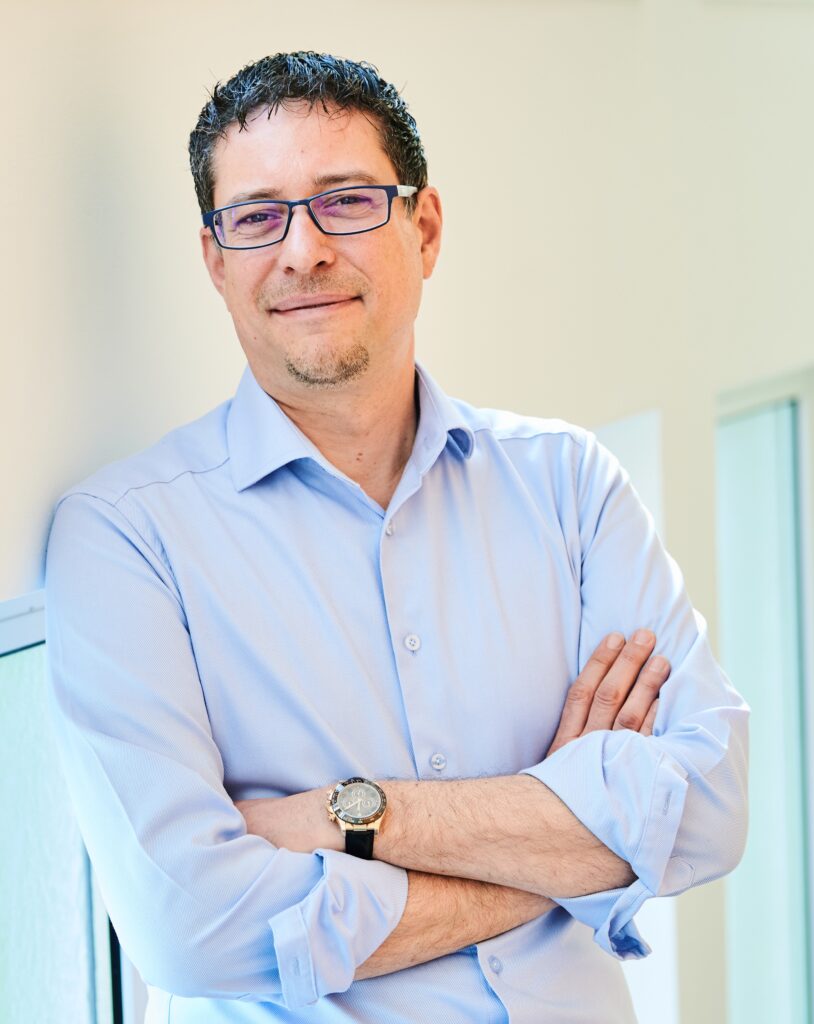
“Sustainability is the core element for being successful in the future. In addition to other factors, such as efficient production or reusability of materials, sustainable feedstocks are also an important part for additive manufacturing on its way to evolve into an industrial-scale production technology. However, it is important to look at sustainable feedstocks from different angles. We select the feedstocks based on comprehensive life cycle analysis considering carbon dioxide reductions together with other important factors such as water consumption and land use. At Evonik, we follow the eCO-line approach: We are working with our value chains to substitute fossil feedstocks with renewable and circular feedstocks such as end-of-life tires and we use renewable energy for production. In this way, the overall eco-balance of our products can be significantly improved along externally certified proceedings without changing material property profiles.”
If you are a regular reader of 3D ADEPT Media, you may already be familiar with the world of “Infinite 3D Printing Applications”that Evonik enables. The German specialty chemicals company continuously carves out a substantial place in the AM industry through its AM brand INFINAM® and investments made by its venture capital firm in the industry, Evonik Venture.
While some of the aforementioned incentives are being taken into account in the automotive industry for the manufacturing of metal 3D-printed parts, leveraging the resources brought by the world of plastics with AM could open up a new range of possibilities for automotive components. But that’s a different subject, that I hope we will discuss in another article.
That being said, there are a wide range of 3D printed plastics used for automotive components. As a matter of fact, plastics remain the most widely used materials in automotive AM. Be it for preproduction benefits, customization or tooling, the advantages in terms of costs, time, and mechanical properties of the parts are worth exploring. Currently, three common methods of 3D printing plastics have gained popularity across the industry: selective layer sintering (SLS)/ Laser Powder Bed Fusion (LPBF), fused deposition modelling (FDM) and resin 3D printing.
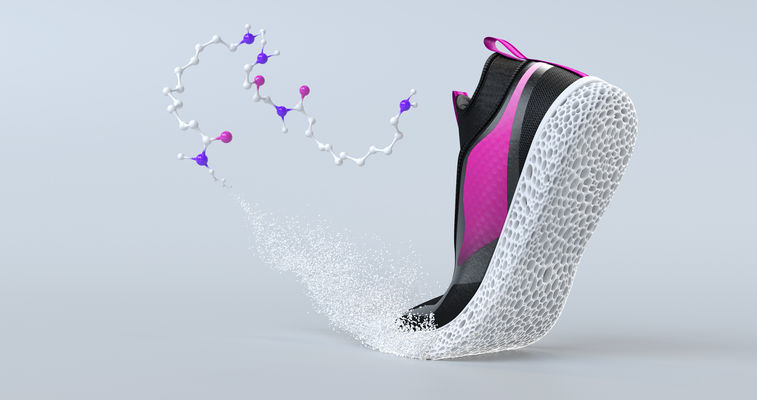
Why the focus on plastic materials for automotive applications?
It is no secret that mechanical components are often subjected to high stresses, high temperature and a corrosive environment which might ultimately lead to failure. The interest in high performance plastic materials naturally gains momentum as they can meet light weight requirements and deliver better properties in automotive applications.
According to a research on polymeric materials for automotive applications, a wide variety of plastics are used in vehicles. The basic functions of such wide use of high performance plastic materials in vehicles dictate the appearance of the automobiles, their functionality, economy and low fuel consumption. The application of polymeric materials allows more freedom in design and approximately 82 percent of an average vehicle’s weight gets recycled. That is, in our opinion, an item AM should take advantage of.
Interestingly, when we look at the most-widely used AM processes mentioned above, Evonik has built up extensive expertise in the development of automotive AM materials for all these technologies.
“Our polymer materials have been used in additive manufacturing for more than 25 years; we offer both the broadest range of technologies to produce powders and a very wide range of chemistry platforms to design photopolymers”, the company’s representative lays emphasis on. The company explains that its proven polyamide 12 powders are well suited for reliable and reproducible production of a large number of plastic parts. “With Polyamide 613, a stiff and ductile powder material with higher heat deflection temperature, we offer an alternative polymer optimized for all challenges in automotive applications – with similar good processability in Powder Bed Fusion printers as our polyamide 12. For applications that require high temperature and chemical resistance, our PEEK filament for the FDM technology is the material of choice. With respect to our photopolymer products, I want to mention the high-strength resin INFINAM® ST 6100 L which resembles glass filled nylon and INFINAM® RG 3101 L, an ABS like material. Both exhibit long-lasting thermomechanical performance and can be used above 70°C, the ST material above even 120°C, which is mandatory for automotive applications. In addition, we launched INFINAM® FL 6300 L together with the Austrian company Cubicure, a polyester-based elastomer photopolymer with unseen durability and fatigue behavior”, Stoerkle notes.
Speaking of applications that these materials can drive, the Head of Additive Manufacturing Innovation Growth Field explains that the variety of applications depends directly on the materials mentioned and their properties. Non-visible components without safety requirements can be 3D printed from polyamide 12, as well as covers and grids for air-condition where a huge knowledge about postprocessing of the surface is already available. For more advanced applications, the polyamide 613 powders with higher heat deflection temperature are suitable. Our recently introduced elastomeric resin INFINAM® FL 6300 L is the right material for dampening applications and cable holders, whereas the high-strength resin INFINAM® ST 6100 L can be used for connectors and clips. When we look at a bigger scale, one of the immediate goals of automotive companies is to accelerate the electrification of electric vehicles. It is currently estimated that 230 million electric vehicles will be sold worldwide by 2030. While the increasing promotion of electrification is partially driven by governments that tighten greenhouse gas emission regulations for carbon neutrality, it should be noted that the challenge is bigger for AM technologies’ providers who need to provide dedicated solutions to enable applications in the field.
The first step for AM companies is to understand that the pivotal component that will enable electric vehicles to stand out from the crowd is the next generation of batteries that should deliver better performance and ever shorter charging times. For material producers, the challenge lies in developing innovative materials to increase scale production at reduced times and costs, assembly speed and greater performance. Some of these materials are currently being developed by Evonik:
“To increase the range of electric cars, higher battery efficiency is needed. The next generation cooling systems with new cooling agents are required. Both monolayer and multi-layer system solutions developed by Evonik for the pipes of the cooling system can fulfill the need for a longer battery duration and perform well with different cooling agents. Moreover, we are developing a material that will meet one of the highest requirements in e-mobility: the V0 flame retardancy of polymers without compromising the chemical and physical properties of the materials over a wide temperature range.”
The goal here is to improve batteries with reduced weight and dimensions, that have efficient temperature control.
Other materials (all technologies included) that will play a key role in improving the efficiency and performance of a battery, include high-tech polymeric materials, polycarbonates, adhesives and thermoplastic materials.
Moving forward…
Amid the wide range of materials that can be leveraged in AM, the materials type that enables the greatest number of opportunities is polymers. The ability to transform these materials into various shapes that may fit the variety of additive manufacturing processes on the market is not only fascinating but it also requires years of expertise in polymer chemistry. Based on Stoerkle’s latest comments, this is exactly what makes Evonik outstanding:
“Thanks to our strength in innovation, years of expertise in polymer chemistry for AM and strong industry partner network, Evonik knows how to develop and manufacture materials and to scale processes for serial production. We use this expertise for the long-term development of new materials for 3D printing serial applications.
If we consider the powders segment, new processes like the ones developed by Evolve or Nexa3D require new, tailor-made powders. For both, the STEP and the QLS technologies, we jointly develop ready-to-use materials from our existing polymer powder portfolio like polyamide 613 for higher temperature applications or our INFINAM® TPA elastomer for flexible parts to make them suitable for those very exciting processes.
Lastly, [throughout this year], you will see our photopolymers appearing on a lot of major printer platforms. Our material validation focus here is on printer systems which promise to bring down total-cost-of ownership and allow for real industrial part production.
We do encourage everyone to contact us to develop and implement further applications with additive manufacturing.”
This exclusive feature has been written in collaboration with Evonik.
This content has first been published in the March/April edition of 3D ADEPT Mag. Remember, you can post job opportunities in the AM Industry on 3D ADEPT Media free of charge or look for a job via our job board. Make sure to follow us on our social networks and subscribe to our weekly newsletter : Facebook, Twitter, LinkedIn & Instagram ! If you want to be featured in the next issue of our digital magazine or if you hear a story that needs to be heard, make sure to send it to contact@3dadept.com