A look at medical 3D printing materials and other materials development
Have you ever realized that the first thing end-users experience when seeing and touching a 3D printed part is the material with which it has been produced? The problem is, a lot of credit is given to additive manufacturing machines, yet the true success of an application usually depends on an underappreciated component: material. As we navigate through the set of indispensable ingredients in an AM production, we have decided to explore the area of opportunities materials enable. What better way to do so than by having a material producer by our side?
Unlike most companies that announced their involvement in the additive manufacturing industry through stunning marketing actions, Evonik has first built up experience and expertise within its field of activity and has waited to have the certainty and the ability to provide real value before coming out from stealth mode.
Although it is best known for the materials it produces, the stock-listed German specialty chemicals company also provides additives as well as quality assurance services. Last year, the company marked a milestone in its AM journey as it decided to give a new direction to its AM materials by grouping them under the brand INFINAM®.
When asked if this name stands for a specific meaning, Sylvia Monsheimer, Head of Additive Manufacturing & New 3D Technologies at Evonik states:
“Our new INFINAM® brand stands for polymer-based materials – powders, resins and filaments – that enable infinite 3D applications. The brand name themselves comes from INFINity + Additive Manufacturing and is aligned with our unique market communication approach which we, by the way, claim #InfinityMeetsReality. In other words, introducing INFINAM®, we boost the chemistry of high-performance polymers and additives into ready-to-use materials for infinite 3D applications.”
As you can see, a glimpse at a materials producer’s activities like Evonik reveals that there are so much to say that it will require more than one article to cover each aspect related to the materials business.
Recognizing all this, we have made a very deliberate choice to address in this article, Evonik’s approach to develop medical 3D printing materials as well as the next steps in terms of materials development the company plans to focus on.
The prism of 3D printing materials for medical applications: the case of polymers
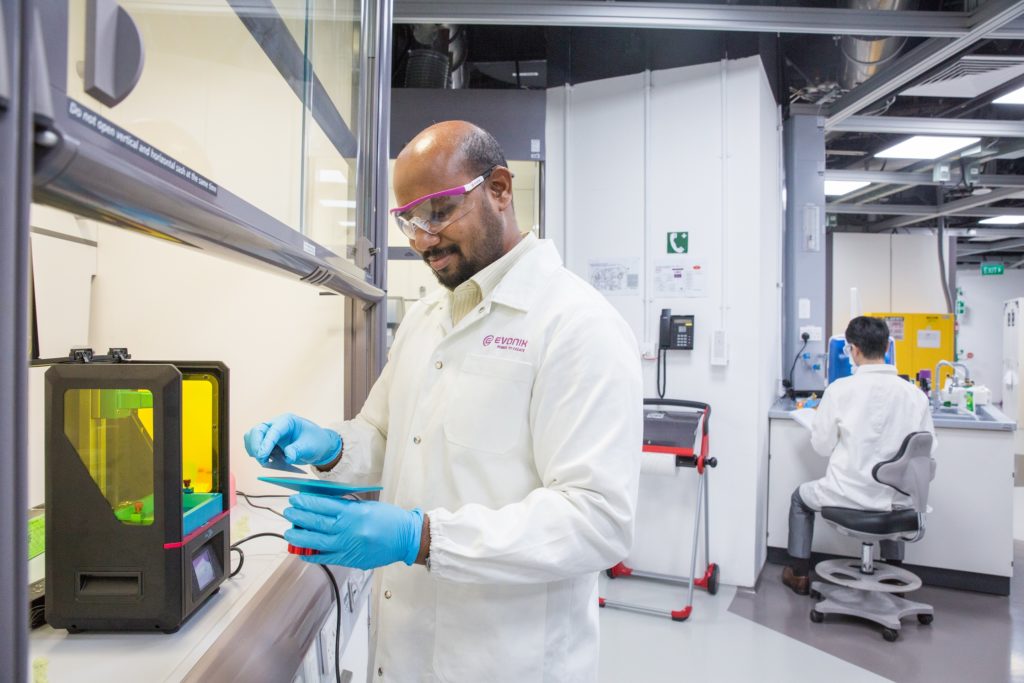
Medical 3D printing breakthroughs keep on going. Current and projected applications can be divided into several categories:
- Tissue and organ fabrication;
- Tailor-made prosthetics, implants, and anatomical models;
- As well as pharmaceutical research, an area that deals with the development of drug dosage forms, delivery, and discovery.
Interestingly, these applications are often enabled through a non-exhaustive list of materials, which may include titanium alloys, cobalt-chrome (cobalt-chromium-molybdenum alloy), and polymers to name a few. The thing is, for a vital industry like the medical, most materials are often subjected to certifications and regulations before being used on a patient.
As a matter of fact, the term biomaterial has been coined to reflect the type of substance that can be introduced into the body as part of an implanted medical device or used to replace an organ, a function of a member, etc.
In this vein, to avoid confusion and to make this very-much needed distinction between AM products dedicated to the medical industry and AM products dedicated to other industries, companies develop dedicated brands to meet the needs of this market. At Evonik, it was also crucial to make that distinction:
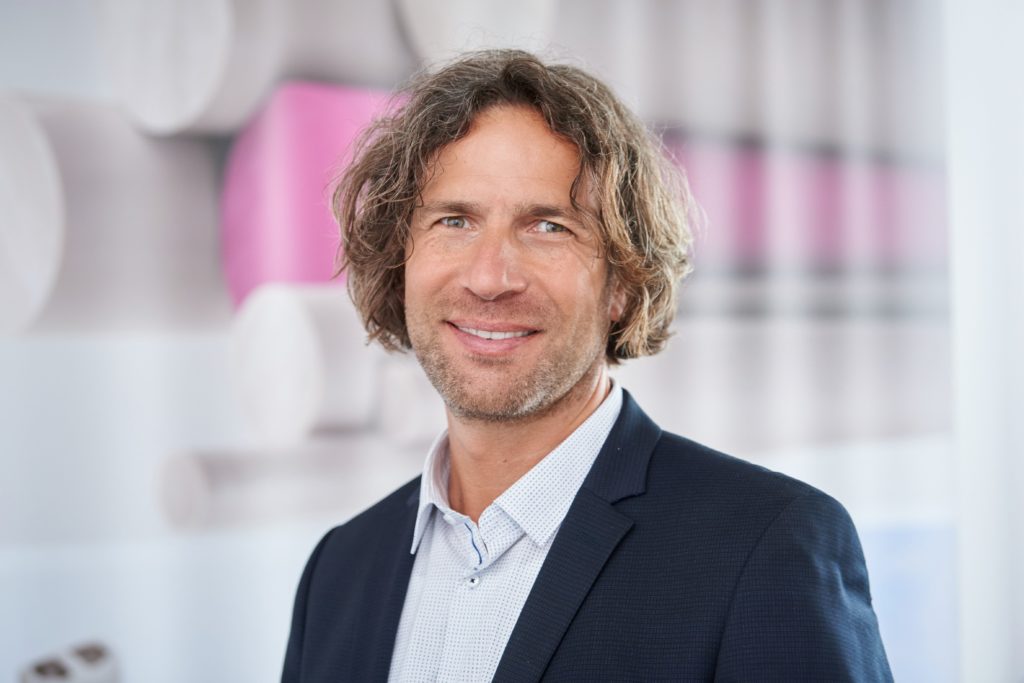
“Evonik offers the most extensive portfolio in the sector of 3D printable biomedical materials for medical technology. For plastic implants the portfolio includes, in addition to VESTAKEEP® i4 3DF PEEK filament for permanent body contact, also the RESOMER® product line with bioresorbable filaments, powders, and granules.”
These specialty materials are subject to strict standard specifications for polymers in medical applications that apply to the respective brands mentioned above. For this reason, these products have been excluded from transfer to the INFINAM® product family and will continue to be marketed under the VESTAKEEP® and RESOMER® brands”, Marc Knebel, Head of Medical, Evonik explains.
Nonetheless, a report from the European Patent Office reveals that between 2010 and 2018 and despite the wide range of materials that exists, a great number of patent applications were filed for 3D printing with polymers compared to other groups of materials combined. This underlines an increasing interest in the use of polymers for medical applications. Apart from the biocompatibility of certain polymers, it should be noted that these materials provide a wide range of opportunities in terms of compositions. It is also possible to modify their structure and surface as well as requirements solicited by specific applications, including the addition of additives to improve the basic properties of plastic materials, as for example, antimicrobial compounds.
That being said, for researchers, surface chemistry, mechanical properties, and topography of functional polymers would be three key parameters that foster their effective use in AM technology. However, as polymers are available under different forms, Knebel advises medical professionals to keep in mind the final purpose of the applications in order to choose the one that suits best a production:
“The most important factor is a good fit of material and processing technology that assure safety and effectiveness for the production 3D printed medical devices. Powders as well as filaments are already successfully used for those applications. INFINAM® PA12 powders are used for short-term body contact devices. VESTAKEEP® PEEK filament is available for long-term body implants, as FFF is the state-of-the-art technology to produce high quality parts in a safe process with this material. When it comes to filaments, an additional advantage is the fact that FFF/FDM printers are typically smaller which can favour the use directly in a hospital environment, with the potential of point-of-care, production of implants. In any case, the freedom of design and the quality is the determining factor over the costs.”
As you may have guessed, FDM remains one of the most commonly used AM technology in medical 3D printing applications. Others include but are not limited to extrusion-based bioprinting, material sintering, inkjet or binder jet printing, polyjet printing or even laminated object manufacturing.
Despite this compatibility of AM technologies with medical applications, this niche segment still suffers from a lack of diversity in suitable biomaterials which results in a low number of applications in the field. Current 3D printing biomaterials are mostly utilized for either drug delivery or space-filling implantation purposes.
According to Evonik’s Head of Medical, the main reason that explains this slow adoption might lie in the fact that the qualification process of a material takes a lot of time that depends on regulatory authorities but also on the work of medical device manufacturers.
“Any new material and technology need to go through a careful step-by-step validation and approval process which does take time. Evonik is already offering a broad range of biomaterials of its VESTAKEEP® PEEK and RESOMER® brands with the required quality and with the needed documentation. Validation and qualification of the printers and printing processes are moving forward quickly. In addition, we note a high interest of medical device manufacturers across the globe thus already in 2021 we are confident that biomaterials will be used in many different applications”, he concludes.
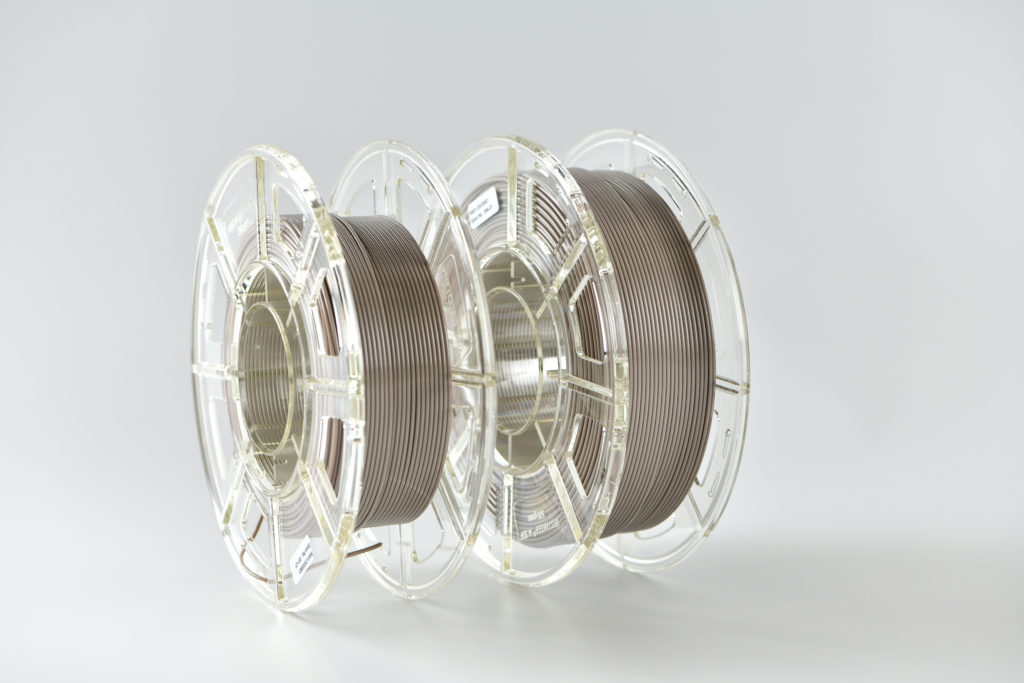
Current and future state of materials development at Evonik
In addition to its bioresorbable powder and its implant-grade PEEK filament for medical applications, Evonik’s 2020 AM activities were also marked by a co-branded flexible high-performance specialty powder based on a thermoplastic amide grade (TPA) and the opening of a new 3D Printing centre in the USA. On top of that,the materials producer has completed the construction of its first plant dedicated to new polyamide 12.
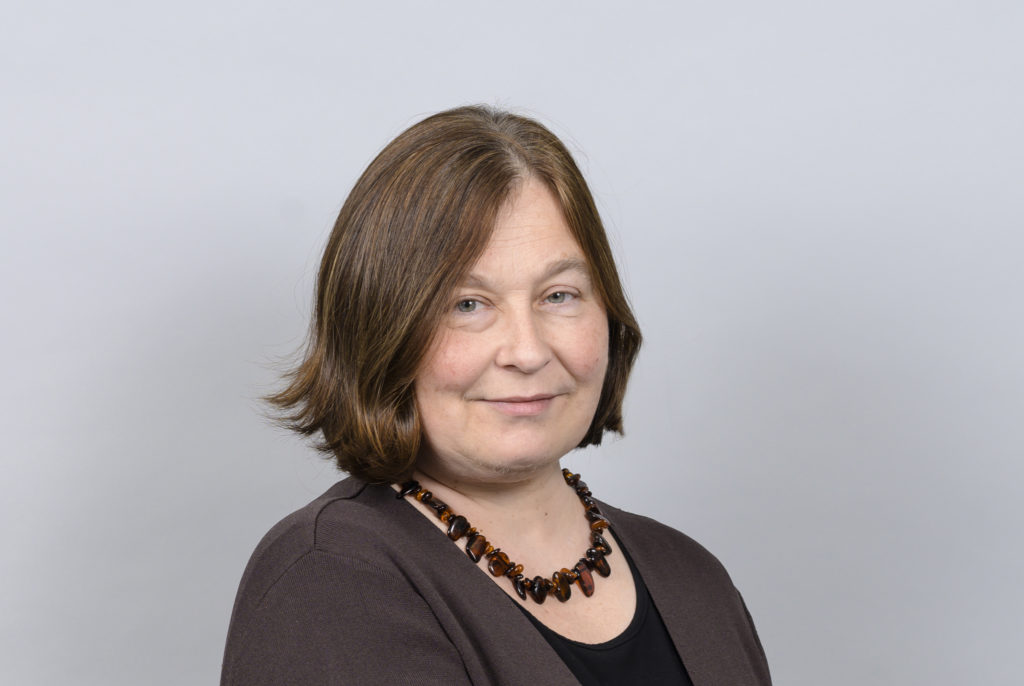
Monsheimer points out the polyamide 12’s outstanding properties make it an ideal material candidate for applications where “high stability paired with flexibility” and “high temperature resistance and low weight” are required. Given its wide range of applications in automotive, oil and gas and even medical devices, “the polyamide 12 market is posting annual growth rates exceeding 5 percent worldwide, significantly outpacing the global gross domestic product.”
Speaking of the AM industry in particular, the materials expert announced that its growth rates even reach double digits.
“We plan to broaden our portfolio of polyamides but also non-polyamide polymers by developing materials with enhanced properties to open new infinite applications. Our new 3D printing centre in Austin, Texas, on the one hand can supply application support to customers and on the other hand our new site has a focus on the material development manufactured by the structured polymers technology which complements our proven methods for powder production beside precipitated polymers”, she announces.
No matter what direction Evonik follows, the company remains driven by the market needs. To do so, the company keeps in mind its primary goal which is to develop “ready-to-use” high-performance materials that can meet the requirements of various technology lines. A goal that necessarily requires an in-depth collaboration with 3D printer manufacturers as we saw with HP and today with Evolve Additive Solutions for the STEP technology – a process that would need a dedicated powder material -.
In this vein, other developments we might expect from the company includes“a new product line of photopolymer resins with unique combination of material properties” which will fill“the gap of today’s commercially available photopolymers for VAT Polymerization.”
Last but not least, at the heart of these activities, also lies the ambition to contribute to a more sustainable industry, but the battle is even harder for a materials producer given the nature of their activity. That’s why sustainability is pursued in various ways, within the group’s Additive Manufacturing Innovation Growth Field:
“On the one hand, we are constantly improving our own production processes to make them as efficient and safe as possible. On the other hand, we are putting our innovative power into the development of, for instance, new powder materials to increase their reusability rate during a 3D printing process. As a matter of fact, some of our INFINAM® PA12 powders can be already reused by only replacing the powder needed for the parts of the previous job”,Monsheimer outlines. And this for us, is the sign that sustainability is not just a topic they talk about, but a vision they are walking through.
This exclusive feature has initially been published in the 2021 March/April edition of 3D ADEPT Mag.