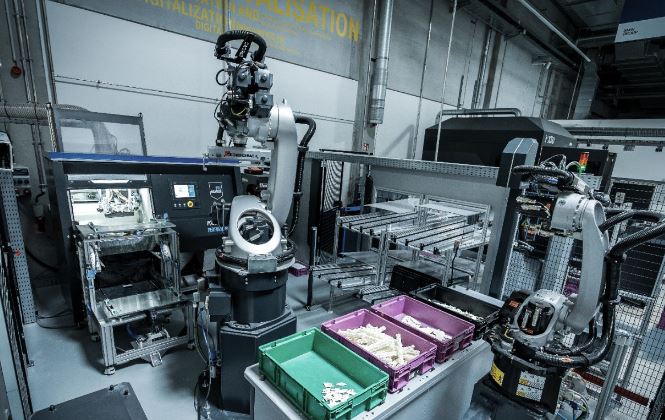
The Additive Manufacturing industry saw the first implementation of an automated AM production line for polymer 3D printed parts at scale at the BMW campus in Munich as part of the Polyline Project.
Earlier in 2020 we reported on the project being launched with 15 Germany-based industrial and research partners to develop a digitalized production line which was used to produce plastic polymer 3D printed parts. Through the Polyline project BMW, DyeMansion, EOS and Grenzebach aimed to complement conventional production techniques like machining, casting, etc with AM in the form of high-throughput production line systems.
The project was funded by the German Federal Ministry of Education and Research with a total of 10.7 million euro for three years.
The Additive Manufacturing Head at BMW Group, Dr. Blanka Szost-Ouk said: “The POLYLINE automated process chain fits into the next generation printers and our standard production requirements, is a system-agnostic solution due to their standardized interfaces. Which is crucial for scaling up Additive Manufacturing”.
The Co-founder of DyeMansion, Philip Kramer said: “The successful POLYLINE project shows that an end-to-end automated factory is possible with 3D printing – and this is just the beginning”.
The Head of Polymer Systems at EOS, Fabian Krauß highlighted how this system can be adapted to fit the needs of other sectors: “We have developed this at BMW for the automotive industry and we can now adopt and adjust it to other industries”.
Development of the automated AM production line
While EOS supported the project with its EOS P500 3D printing system which can be fully automated and integrated, DyeMansion enhanced the finishing of the 3D printed parts with their post-processing solutions.
“The level of automation and integration then differs from the use case and can be adjusted specific to each situation. The machine ensures the highest reliability, the highest level of homogeneity, repeatability, and reproducibility. Besides a high level of automation and integration, the EOS P 500 provides a superior level of flexibility. It offers different modes of operation and has a one-click mode of operation for shop floor execution as well as an all-access operation for manufacturing engineers. Using industry standard APIs for software connectivity, hardware automation and integration, the EOS P500 can be integrated into industrial environments”, said Fabian Krauß.
With the help of DyeMansion’s Powershot DUAL all the requirements for physical automation were fulfilled to run continuous batches in the absence of an operator.
“The Powershot DUAL Performance was built for scale, so it can serve ten or even more printers in the production and therefore make an end-to-end factory possible”, said the DyeMansion Co-Founder, Philip Kramer.
Grenzebach helped with intelligent and safe networking of the additive manufacturing processes in the Polyline project. This includes
- the Exchange P500/4 solution, which is placed directly at the printer and automatically replaces the exchange frame and cools the build jobs in the buffer stations.
- the automated transport of the exchange frame to the next stations with the secure transport container and an automated guided vehicle (AGV)
- the robotic cell with KLT handling and bin-picking robots for further processing and sorting of components.
In addition, the joint development of automated hardware and software interfaces suitable for industrial use in all process stations was a central component of the Grenzebach work package.
“The main advantages of automation are to increase the productivity of the equipment, to reduce the downtime of the equipment, and to create a safe work environment for the employees”, said Oliver Elbert, Head of Additive Manufacturing at Grenzebach.
The AM companies involved in the Polyline project are displaying their products at Formnext 2023 at Frankfurt.
Remember, you can post job opportunities in the AM Industry on 3D ADEPT Media free of charge or look for a job via our job board. Make sure to follow us on our social networks and subscribe to our weekly newsletter : Facebook, Twitter, LinkedIn & Instagram ! If you want to be featured in the next issue of our digital magazine or if you hear a story that needs to be heard, make sure to send it to contact@3dadept.com