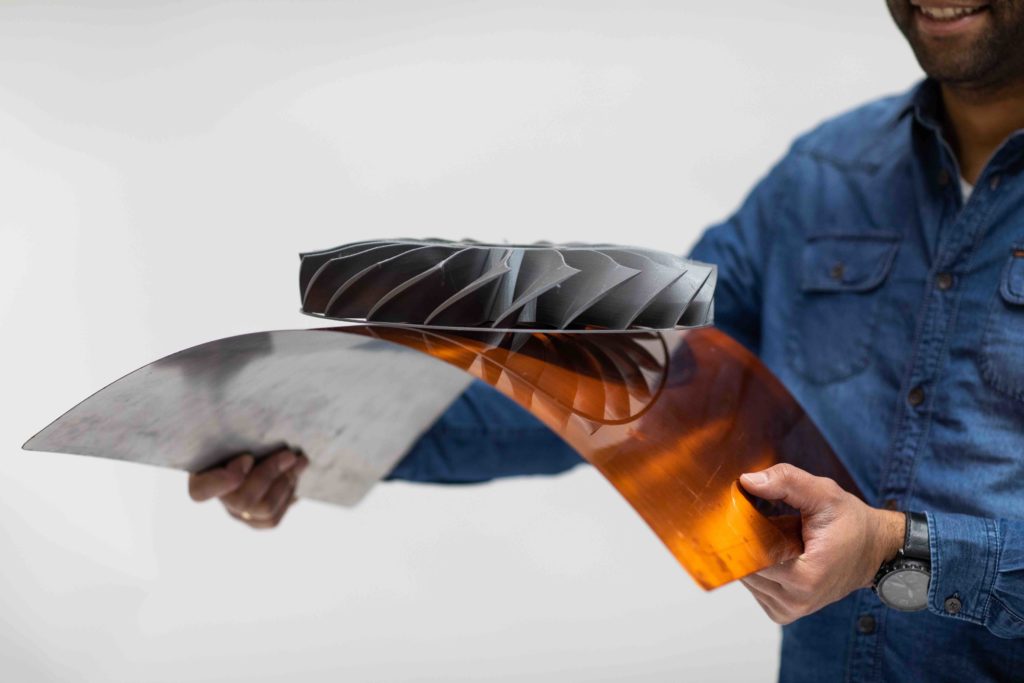
In order to help companies overcome one of the biggest barriers to the adoption of additive manufacturing (“cost”), the Netherlands-based manufacturer FELIXprinters provides a range of industrially-oriented 3D printing platforms.
Since the beginning of this year, the manufacturer unveiled 2 3D Printers including the Pro 3 Desktop 3D Printer. According to the company, the adoption of AM processes for production applications is still relatively low. Several reasons can explain this situation:
- High capital and running costs; high consumable costs; inconsistent material properties which are a significant prohibitor for critical components; and, often, a failure to understand when and how to apply AM to maximize its benefits.
- The lack of resources provided by conventional entry-level AM platforms, which are affordable but remain unreliable, not to mention their high failure rates.
How does the company respond to these barriers?
To respond to this adoption for production application, the Dutch manufacturer has relied on two things: price and specifications.
The FELIXprinters industrial AM machines vary in cost from approximately €2000 to €13,000 depending on the build envelope required. The full range of the company’s industrial AM machines are backed up by an array of ancillary products and services and pro-active customer service supplied to the users of the company’s technology.
The FELIX Pro L and XL 3D printers have been developed with greatly increased build volumes, up to 144 Litres (the Pro L can build parts up to 300 x 400 x 400 mm or 11.8” x 15.75” x 15.75”; while the Pro XL has a build chamber of 600 x 400 x 600 mm or 23.62″ x 15.75″ x 23.62″).
To ensure quality and reliability, both of these larger systems incorporate print chambers, which incorporate an enclosed warm zone and a cold zone. The warm zone supports consistent temperature control during the build, which is particularly important when printing materials with a high shrinkage factor, such as ABS, carbon fiber or Nylon. In contrast, the cool zone is where the electronics are housed, to prevent overheating and subsequent machine/build failure.
Through these key products of its portfolio, the company aims to give manufacturers the ability to benefit from the use of 3D printing as a production tool.
For further information about 3D Printing, follow us on our social networks and subscribe to our newsletter
Would you like to subscribe to 3D Adept Mag? Would you like to be featured in the next issue of our digital magazine? Send us an email at contact@3dadept.com
//pagead2.googlesyndication.com/pagead/js/adsbygoogle.js (adsbygoogle = window.adsbygoogle || []).push({});