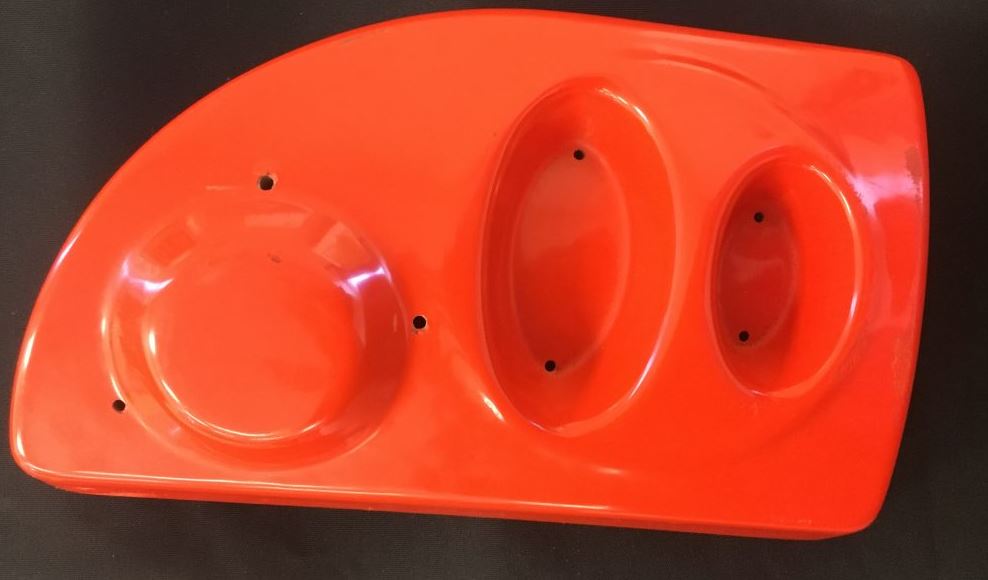
ExOne and Catalysis recently announced their intention to work on a new rapid tooling process. Invented more than 30 years ago, the concept consists in combining rapid prototyping techniques – nowadays additive manufacturing – with conventional tooling practices to produce a mold quickly or parts of a functional model from CAD data in less time and at a lower cost relative to traditional machining methods.
In this case, ExOne has brought its 3D Printing technology to help Catalysis develop a new rapid tooling process for low-to-medium volume production parts. Simply put, the team 3D printed an ExOne sand mold using the manufacturer’s binder jetting technology.
Proprietary coatings were given to the mold so that it could be a reusable for low-to-medium run production.
Catalysis customers that operate in a diverse variety of end markets, including automotive, appliance, aerospace, incubators, medical, packaging, recreation and more, can benefit from this new solution for metal forming, vacuum forming and plastic injection processes.
“We offer a number of different 3D printing technologies and select the best technology to meet and exceed our customers’ needs, based on the specific application. Given its speed and volume capabilities, we are especially interested in binder jetting for production parts. ExOne offers the best solution to satisfy this need,” said Darrell Stafford, Chief Executive Officer and President of Catalysis Additive Tooling. “With an ever-increasing number of applications, we are finding that our go-to technology for development of thermoforming, composite and foam tooling is binder jetting.”
For further information about 3D Printing, follow us on our social networks and subscribe to our newsletter
Would you like to subscribe to 3D Adept Mag? Would you like to be featured in the next issue of our digital magazine? Send us an email at contact@3dadept.com
//pagead2.googlesyndication.com/pagead/js/adsbygoogle.js (adsbygoogle = window.adsbygoogle || []).push({});