Exclusive interview on a tripartite collaboration of MSC Software, Markforged and Danfoss that’s leading to the delivery of performance optimisation tools for Markforged users.
While no one can say with certainty what will happen in the (near or distant) future, technology experts provide more certainties with regards to the future of manufacturing – especially additive manufacturing (AM). Additive has been around for decades, but in the last five years we’ve seen a groundswell of manufacturers turning to the AM as affordable, industrial-grade printers have entered the market.
Industrial 3D printers can print complex parts with materials and processes that are reproducible, consistent and provide high quality results that mirror the intent of the engineer that designed them. However, just as reductive manufacturing processes have been refined and perfected, know-how and experience are essential to ensuring a part performs as it should when it is 3D printed.
This is exacerbated if manufacturers have limited knowledge of the materials involved. When the desired result is not achieved it is not only frustrating; you might not know the reasons why. There are many factors that could affect how a part performs under load such as an incompatibility between material properties and the AM technology, or if a complex part topology is not well optimized for the print process that is used. The difference is that new AM processes are data-driven and the materials can also be encoded digitally, so a design can be modelled and simulated precisely before a single part is printed.
Danfoss, a global industry leader that provides hydraulic and electronic solutions for mobile equipment, was an early adopter of this new technology, and they soon found that even the best designs required iterations of these challenges. One of the company’s objectives was to test the parts were ready to be added to the manufacturing line. So, the company set out to reduce the number of build trials per part and find a Finite Element Analysis (FEA) tool that might lead to a “right first time” approach while using AM technology.
The Danish company has therefore decided to leverage the expertise of its two partners, Markforged & MSC Software, to address these challenges.
We sat down with Craig KLOCKE, Tripp BURD & Olivier LIETAER, respective representatives from Danfoss, Markforged and MSC Software to discuss these challenges and the unique solution that will be made available to a larger public in the future.
Olivier LIETAER from MsC Software Tripp Burd from Markforged Craig Klocke from Danfoss
How did Danfoss initiate the partnership between Markforged and MSC Software?
The Danfoss Group has a solid footprint in the additive manufacturing industry. The company is known for its comprehensive range of products and services in cooling food, air conditioning, heating buildings, variable frequency drives, gas compressors and powering mobile machinery – in other terms, a wide range of industries where they can explore various applications of AM.
Three decades ago, the company started using additive manufacturing. The Danish Group has explored several types of technologies such as SLA, FDM, MJF and composite printers, as well as partnering with Fast Radius to accelerate the adoption of AM.
Moreover, 2017 was a decisive year for the industrial manufacturer that took a giant leap into its digital transformation with the opening of the first of three global 3D printing centres in Nordborg, Denmark, and later on, in North America and Asia.
To date, the Group recorded over 15,000 3D printed parts manufactured around the world. However, despite the current – yet – quiet success of its digital transformation, Danfoss still encounters challenges in its path to optimize production efficiency.
Optimizing production efficiency with metal AM and appropriate software tools
Just like several industrial manufacturers, the multinational has relied on AM to accelerate its digital transformation. Indeed, metal AM remains a key factor influencing market demand and Craig Klocke’s team is completely aware of that. The Head of Additive Design and Manufacturing declared:
“Everyone knows the advantages of AM: its flexibility, its added value for customers. Metal is required in some applications because of its general properties and its ability to meet requirements in terms of strength and stiffness although polymers and composites have incredible capabilities.
Furthermore, another reason why we need metal 3D Printers is that our current materials are metals. Plus, it’s quite ironic, but we need to have all capabilities in metal 3D printing to secure the majority of our requests. Indeed, our clients believe we need to have it, so we make sure we have it, otherwise, they would not want to deal with us. Actually, a small percentage of our requests end up in metal 3D printing applications, however, it is increasing!”
Leveraging metal 3D Printing capabilities can quickly become costly if the user does not have the appropriate tools, not to mention the time invested in production processes and testing, but the team has been impressed by Markforged’s affordable technology. Danfoss harnesses both metal and composite printers from Markforged in its facility. The team found that Markforged’s composite parts were as strong as aluminum when reinforced with carbon fiber, but they didn’t have any experience in polymer and composite parts when they started. The Head of Additive Design and Manufacturing mentioned, “Without this experience, the trial and error cycles are much longer and harder. As we are already a customer for both Markforged and MSC Software, it was easy to connect our three companies, to discuss this issue. The challenge was even bigger for Markforged and MSC Software that needed to develop a solution that would better improve our ability to predict, but also to integrate the detailed fiber path of the printer into the software”, continued Klocke.
The partnership between Markforged & MSC Software
Markforged is one of those manufacturers who strongly believes that a robust additive manufacturing solution could make a major difference in the race against digital transformation. Acknowledged for its metal and carbon fibre 3D printers, the manufacturer has raised a significant amount of new capital this year ($82 million in a Series D funding round, making its total raised $137 million since 2013) to lead innovations.
MSC Software, on the other hand, is part of a big family, whose functioning is crucial to understand to be able to make the most of it. The company develops simulation software technology that enables engineers to improve quality, save time, and reduce costs associated with design and test of manufactured products. Simufact Engineering simulates metal manufacturing processes, while e-Xstream engineering provides the composite and advanced materials modelling platform called DIGIMAT. All companies are part of Hexagon, a global provider of sensor and information technologies in many industries (aerospace, automotive, healthcare and many more).
To address Danfoss’ need, Markforged and MSC Software have decided to work together on the validation and optimization of designs before they’re printed on Markforged 3D printers.
It looks very simple saying this way, yet we are talking about a long process that requires a full understanding of the printing process and the integration within numerical simulation workflow such as a Hexagon Additive Manufacturing Solution.
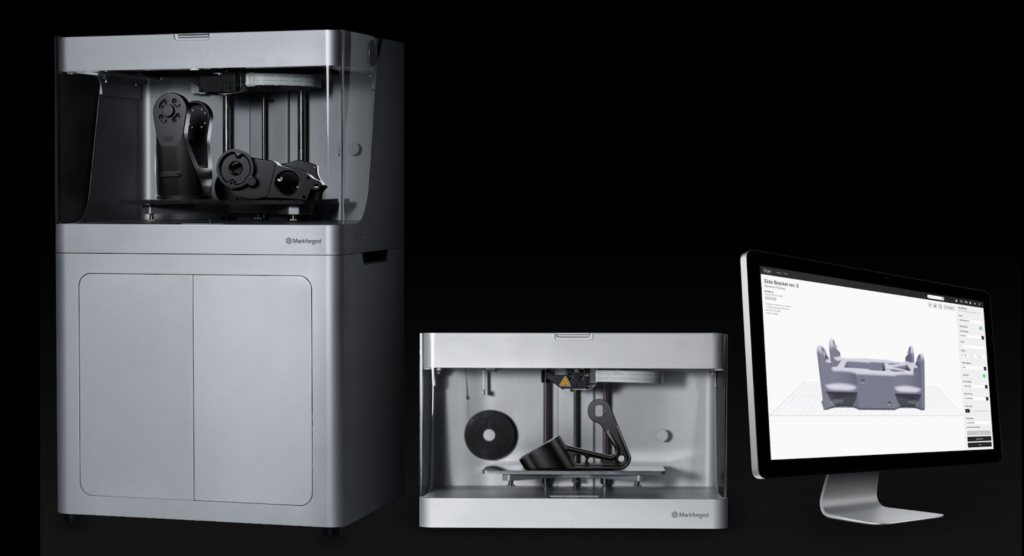
Building an additive manufacturing solution
The development of Digimat for Additive Manufacturing started a couple of years ago. As the technology and market expand, the company developed a solution dedicated to AM. “Five years ago, we started discussing with key customers for Digimat Additive Manufacturing. They wanted to benefit from the same numerical chain that we propose for injection molding, but in this case for AM”, explained Olivier Lietaer, Business Development Engineer at e-Xstream Engineering.
MaterialCenter is a material lifecycle management platform developed by e-Xstream Engineering, known for its Digimat product, that aims to track, collect and store all material-related data.
“Specifically for AM, MaterialCenter enables manufacturers to improve the print quality and ensure the traceability by capturing all AM data. Those data can be linked to the material (the batch number), the machine (the type of 3D Printer used for the production, its serial number), the process settings, the number of parts in the build or the testing”, continued theBusiness Development Engineer.
In other words, this centralized data management system would enable any user in a few minutes, to find relevant data that are fully connected and traceable across the Company.
“If the user wants to compare different builds, or if there is an issue with the production of a given part, the user can easily go back to the part manufacturing data and discover what was the cause of the problem”, said Lietaer.
With the recent acquisition of AMendate, a Germany-based company that specializes in topology optimization, MSC Software is now able to provide a holistic generative design software solution called Apex Generative Design that automates the design of 3D printable designs. Furthermore, backed by its parent company Hexagon, MSC Software is increasingly able to provide industrial manufacturers end-to-end solutions for AM that incorporate scanners and metrology software to close the design process loop with inspection of the produced part and finishing.
“With the recent acquisition of AMendate, we are now able to propose topology optimization capabilities. Whatever the technology used to create the part (metal, polymer or composite), we are well-positioned to help the engineer make the right choices through the use of the data management system, process simulation with Digimat or Simufact and as-printed part performance. The reason why we have various solutions is more historical: we are coming from the materials engineering world and Simufact is coming from the metallic manufacturing world. It makes sense that each of these companies develops dedicated solutions. Moreover, we absolutely have to see things at a higher level: whether the user leverages Digimat or Simufact, they belong to our End-to-End Solution, the most important thing is that we are helping engineers to produce their parts with more efficiency, by lowering their cost, and the amount of materials that is usually used”, declared e-Xstream Engineering’s spokesperson.
The potential of numerical simulation: Material Engineering, Process simulation, and Part Performance
To help Danfoss predict what will happen during the production process with Markforged’s 3D printers, MSC Software and Markforged are currently working on three important stages: Material Engineering, Process simulation, and Part Performance.
The process simulation was also a key issue raised by Danfoss. Their engineering team wants to know how the part will exactly be printed – If there will be a risk of debonding for instance – and any other issues that might prevent a failure. As for part performance, Danfoss’ engineers need to know how to optimize the part performance for a given amount of material. The Onyx and continuous carbon fiber materials are the two materials whose data were analyzed as part of this partnership.
MSC Software’s strategy is, therefore, to leverage a Digital Twin technology to collect and analyze real product data during operations. As per the words of Lietaer, they develop “Digital Twin (DT) of materials by creating materials models which can be used for the simulation.” It is also possible to create a DT of the printer.“With this digital twin, [it will be possible for Danfoss to] first virtually investigate and understand the process, define what is the best workflow, what is the impact of changing any aspect of the design [in their] process, before physically evaluating and testing the part.”
Images via Danfoss Images Digimat
Markforged and MSC Software have only been working for a couple of months.“We have already made huge efforts and progress in terms of steps we need to achieve to get the right numerical simulation tools. We started with mechanical testing of the materials, both the Onyx and the continuous fiber. The testing campaign includes different configurations, with respect to the toolpath orientation”, explained e-Xstream, although they could not reveal more about the details of the test.
However, the company affirmed that the materials models have been integrated into the new Digimat version released on October 24th (the first step) and allowing advanced users to benefit from the technology.
“Firstly, we are now working on an interface that allows users to exchange toolpath data between Markforged’s software and Digimat. Taking into account the materials behaviour and the toolpath data are the two key ingredients to predict the parts’ structural performance and validate that the composite part can replace metal. Lastly, Markforged printers and processes will be integrated in our standard FEA validation tools that are easy and efficient to use for anyone”, continued Lietaer.
Concluding thoughts
It should be noted that although the MSC numerical simulation discussed presents advantages when it comes to determining the ideal weight or defining the best part layup to reduce printing time and material usage, but it will not be a requirement for Markforged’s existing or future customers.
“The partnership with MSC Software is very exciting” noted Tripp Burd – Manager, Strategic Application Engineering at Markforged who is happy that a request from their mutual customer enabled them to work together. “Partnering with technologies like the Digimat allows our customers to better understand and increase confidence in the performance of the printed parts. AM is a quite new technology and there is still much to learn about this area. The application of software simulation for the production of components is a great addition to our technology that delivers parts that were not possible to deliver with other technologies.”
“The materials of Markforged are advanced and quite challenging to model. So, there will be a continuous effort to improve the accuracy of the solution. Over time, we will be able to achieve the same level of accuracy that we have for other traditional techniques. Our goal is to accelerate adoption of AM by helping the engineers to take the right design choices and increase the aperture of AM applications. We trust that numerical simulation and such partnerships are key to achieve this”, concluded Olivier Lietaer.
“My vision and hope are that FEA, AM and composites become automatic activities just like it is today for traditional manufacturing. With traditional FEA, we have eliminated the test cycle, build cycles by using numerical analysis. And I am confident that we will get there very quickly with AM as well. That means, as part of our development, reduced costs and reduce risks. It’s green and effective. I am very pleased that Markforged and MSC Software enter a partnership and that we have been able to initiate it. I am really excited to continue the partnership that we have with both companies. I can’t predict where we will be in five years for now, but I know it will be a better and more exciting place than the one where we are today”, said Klocke.
This interview has originally been published in the October-November Issue of 3D ADEPT Mag.