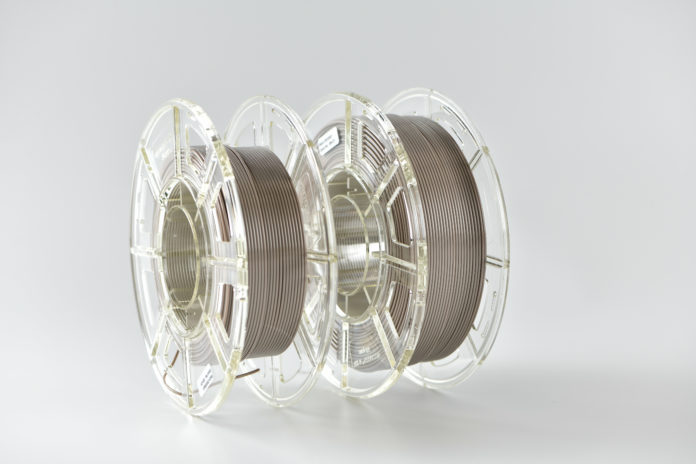
With the release of its new 3D-printable PEEK (polyether ether ketone) filament, Evonik raises the bar for the production of custom-made plastic implants.
Indeed, the specialty chemicals company’s new filament is an implant-grade material for medical applications that meets the requirements of ASTM F2026, a standard specification for PEEK polymers leveraged in surgical implant applications.
Available under the brand name VESTAKEEP® i4 3DF, the development of the new material is based on a highly viscous, high-performance polymer from the producer: VESTAKEEP® i4 G. developed in compliance with cleanroom requirements, the new PEEK has also been subjected to stringent quality management standards for medical materials.
According to the company, operators that will leverage the material with their FDM technology will appreciate the filament’s biocompatibility, biostability and x-ray transparency. With a diameter of 1.75 mm, the filament is available as a spool of 250- or 500-gram.
“For modern medical technology, the development of our first 3D-printable implant material opens up new opportunities for customizing patient treatments. Orthopedics and maxillofacial surgery are examples of areas where this could be applied,” says Marc Knebel, who heads the Medical Devices & Systems market segment at Evonik. “Innovative high-performance materials like Evonik’s VESTAKEEP® PEEK—along with highly complex hardware and software, and the perfect match between materials and machines—form the basis for a sustainable 3D-printing revolution in medical technology. Therefore, we will successively expand our product portfolio of 3D printable biomaterials.”
A cost-effective way of adapting the materials’ characteristics to a given 3D Printer
As a materials producer, Evonik is well aware of the fact that buying a filament without any assurance that it will meet a given application is most of the times a waste of money.
For this reason, customers can benefit from a testing-grade version of its PEEK filament. In other terms, that testing-grade version will be a similar material that would integrate the same product properties as the implant grade, but without the documentation needed for approval in medical technology applications
In a recent conversation, Sylvia Monsheimer told us there is a need to develop tailor-made materials for each technology on the one hand, and to work in compliance with the customer pespective on the other hand. That’s exactly what they are doing right now.
Remember, you
can post free of charge job opportunities in the AM Industry on 3D ADEPT
Media or look for a job via our job board. Make sure to follow us on our
social networks and subscribe to our weekly newsletter. : Facebook, Twitter, LinkedIn & Instagram ! If you want to be featured
in the next issue of our digital magazine or if you hear a story that needs to
be heard, make sure to send it to contact@3dadept.com.