A lightweight electric commercial car chassis optimized for performance is built using wire arc additive manufacturing (WAAM). A novel stream-lined design framework combined with near-net shape efficient additive manufacturing helps to reduce the product design, iteration and validation cycles by a factor of >120.
In electric vehicles, achieving structural, weight and performance optimization of traditional gauge-level chassis follows an extended design-and-iteration cycle. This is a time-consuming process that typically spans 2 to 3 years and struggles to align with a rapid changing market.
A new holistic framework significantly condenses the design, optimization, and validation stages for automotive chassis. By optimizing weight saving and performance improvement and by reducing the development cycle, this method contributes to the sustainability of energy-efficient vehicles.
Wire arc Additive Manufacturing (WAAM) technology offers a commercially viable and technically flexible alternative to chassis manufacture to overcome the limitations of traditional chassis production.
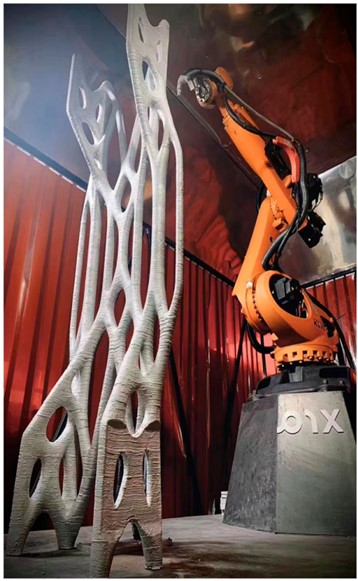
WAAM is typically best suited to produce large-scale high-value components with complex geometries that are difficult to achieve through traditional milling or casting processes.
The WAAM system comprises a Fronius CMT Advanced 4000R arc power supply with a wire feeding device, a Cold Metal Transfer (CMT) welding torch installed on a KR 150R2700KUKA robot, and an argon conveying system and working platform. The feedstock is a 7075 aluminum alloy welding wire with a diameter of 1.2 mm and is deposited on a 7075 aluminum rolling substrate in the T6 state.
First, a pool of 44 skeleton chassis is designed using automated topology optimization methods. These candidates are then ranked according to their material usage (costs) and to optimize the manufacturability and deposition rates. The validation phase concludes the development cycle with representative crash and collision simulations at speeds of up to 40km/h where results show the printed structure sustains minimal deformations.
This framework combines numerical simulation and experimental characterisation to significantly reduce the chassis design, iteration, and validation cycles cycle down to a week, accelerating the development process by a factor of 120.
This framework is applicable to nearly all robotic arm-based 3D printing strategies and facilitates real-time optimisation of the deposition process according to the geometric design.
References:
The pictures referenced in this article come from the reference below available in an Open Access form, distributed under the terms of the Creative Commons Attribution-Non Commercial License.
[1] Jianlin Li, Qiang Cui, Chi Panga, Peng Xu, Wei Luo and Jiangshan, Integrated vehicle chassis fabricated by wire and arc additive manufacturing: structure generation, printing radian optimization, and performance prediction, VIRTUAL AND PHYSICAL PROTOTYPING 2024, VOL. 19, NO. 1, e2301483.
About the author:
This article has been written by Stephanie Giet, PhD. Giet spent the last 12 years working with metal additive manufacturing (AM), particularly for aerospace.
More recently, she validated the full AM value stream to manufacture, qualify and certify AM parts for commercial flight with EASA. Today, she shares technical insights into the use of metal AM technologies and their applications to industrial products.