This article has been updated to highlight the key specifications of the A205 alloy
In 2020, ALTANA AG, a speciality chemicals group headquartered in Germany, acquired TLS Technik GmbH & Co. Spezialpulver KG, a market-leading niche supplier in the field of atomization and customization of special alloys, in particular Titanium, Aluminum, and Copper, with flexible production concepts and the ability to atomize in temperature ranges up to 2500 °C. Almost in parallel, the UK-based Aluminium Materials Technologies Ltd. (AMT), the developer of the patented special alloy A205 and the corresponding A20X powder, was acquired by ALTANA to expand its ECKART division and to enable the market entry into the AM segment as a specialist for atomization, classification, and customization of metal alloy powders. With ECKART’s decades of experience in the manufacturing of pure, spherical and nodular aluminum powders, as well as zinc and copper-based metal powders, the know-how and capabilities of AMT and TLS significantly strengthen ECKART’s footprint in the AM market. ECKART officially made its entrance into the market last year at Formnext 2021, just after the full integration of AMT into its activities.
A closer look at the main alloy ECKART provides the AM market with
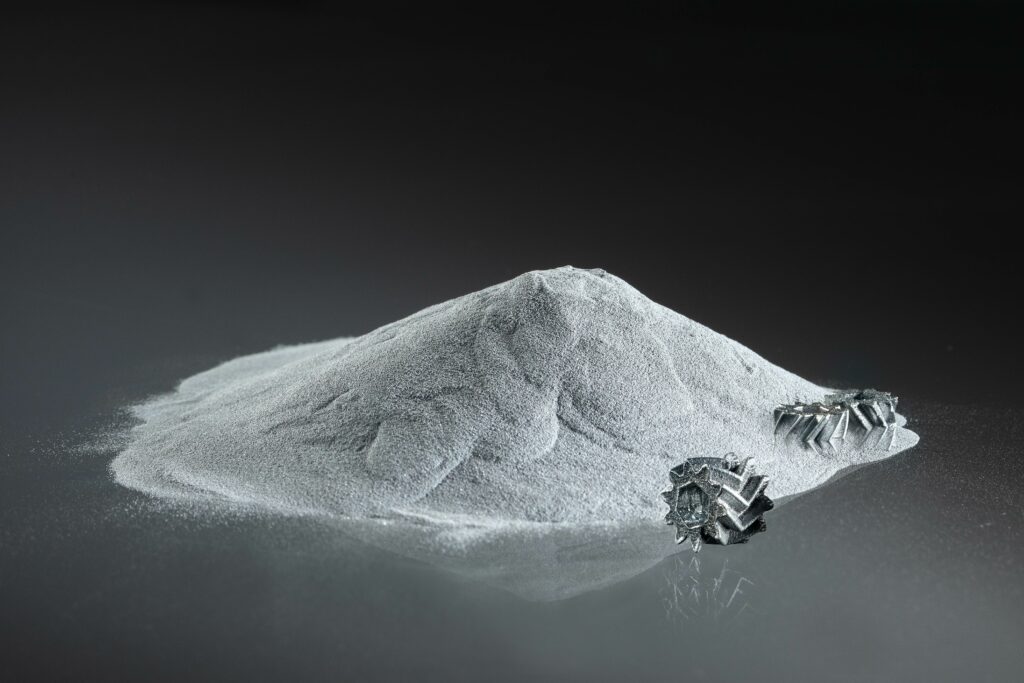
Additive manufacturing of high-strength aluminium alloys has been challenging from the beginning, with most alloys being susceptible to the formation of metallurgical defects during processing. To overcome this challenge, AMT has driven the development of high-performance aluminum alloys specifically designed for additive manufacturing and casting applications. The unique A205 alloy overcomes the intrinsic weaknesses of conventional aluminium alloys, combining outstanding mechanical performance with excellent processability.
A20XTM is a lightweight aluminum-based powder derived from the aerospace-approved (MMPDS) A205 alloy. Its unique chemical composition contains ceramic TiB2 particles which modify the solidification mechanism, resulting in fully equiaxed and fine-grained microstructures. Indeed, an important feature of A20X is its excellent processability which is characterized by a wide processing window during laser powder bed fusion (LPBF). Like AlSi10Mg, A20X is not susceptible to solidification cracking and can be processed on any commercial LPBF machine.
In contrast to AlSi10Mg, however, A20X shows superior mechanical properties. Even at 200 °C, its yield strength is still above 300 MPa. This is attributable to two factors: ceramic TiB2 particles stabilizing the microstructure, and the choice of the alloying additions Cu, Mg, and Ag, the concentrations of which have been optimized to result in the formation of a high number density of thermally stable nanoprecipitates. A20X has proven to exhibit fatigue properties comparable to wrought, high-strength aluminum alloys, making it the best-performing aluminum alloy for additive manufacturing, the company explains.
ECKART’s 2022 AM roadmap and presence at Formnext 2022
Ever since it positioned itself in the Additive Manufacturing market, the commercial development of the established A20X™ powder is an important pillar of ECKART’s approach.
“In these difficult times, we are fully focused on our goal of being the partner of choice for our customers in the field of metal powders. ECKART is one of the leading global players with decades of experience in the field of atomization. Our focus remains on highest quality and reliability – we continuously improve our product and service offerings. The year 2022 is exceptional, dominated by harsh price fluctuations, supply chain and raw material shortages globally. ECKART and ECKART TLS GmbH set the focus on remaining a reliable partner for our customers despite the macroeconomic challenges we are facing”, Dr. Ulrich Schmidt, Global Head of Functional Applications at ECKART GmbH states.
The company will showcase the capabilities, unique properties, and application areas of the proprietary A205 alloy at Formnext 2022, in Hall 12.0, A101.
Remember, you can post your job opportunities in the AM Industry on 3D ADEPT Media or look for a job via our job board. Make sure to follow us on our social networks and subscribe to our weekly newsletter : Facebook, Twitter, LinkedIn & Instagram ! If you want to be featured in the next issue of our digital magazine or if you hear a story that needs to be heard, make sure you send it to contact@3dadept.com