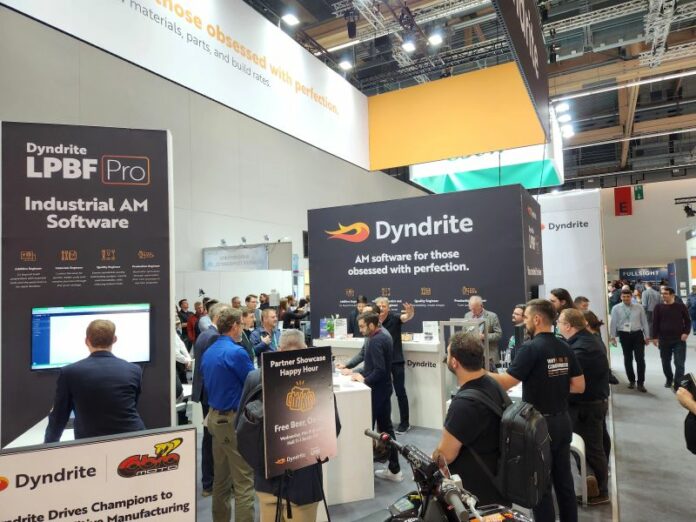
The Additive Manufacturing industry’s demand for a faster adoption of 3D printing materials and techniques got a new lease of life Dyndrite joined forces with AM companies Constellium, Elementum 3D, and Sandvik to launch “Materials Consortium”.
Dyndrite brings its additive CAM software experience to this industry-led materials consortium. The primary objective of this collaboration is to make (LPBF) powder parameters and related testing data for 3D printing materials freely available to the public. This will help in better knowledge sharing resulting in increasing adoption of printing materials across sectors.
The new materials consortium is set up to help the AM industry with
- materials parameter sets for Laser Powder Bed Fusion (LPBF) 3D printers
- print parameter sets and related material test data for ASTM Consortium for Materials Data
- standardization (CMDS) initiative and for public access.
The Consortium will work with metal plastic powder providers to add more 3D printing materials parameters to the forum.
The Materials Consortium members will explore the production, testing and public access of 3D printing materials parameters.
Democratizing access to 3D printing materials parameters
The CEO of Dyndrite, Harshil Goel spoke of the necessity of the Consortium as it will help “maximizing the capabilities of 3D printing materials, specially as it relates to the geometry being printed, is a black art within our industry”.
Calling 3D printing materials the “pillar of Additive Manufacturing”, Goel added: “If additive is to become a mainstream manufacturing process, users require transparency and standardization. Public access to a set of trusted, democratized parameters shines a light on the path of adoption”.
The Chief Engineer of Constellium, Ravi Shahani said: “The Materials Consortium will make it easier for our customers to benefit from our high performance materials designed specifically for laser powder bed fusion, such as our Aheadd® CP1 aluminum-iron-zirconium powders”.
“This will help accelerate adoption of aluminum AM across multiple LPBF platforms to produce higher performance components at lower qualification cost and lower production cost. Customers will quickly achieve predictable, robust properties, precise geometries, better surface quality, simplified post-processing and optimized print cycle times”, Shahani added.
Dyndrite is building on the success of its recently launched next-generation 3D printing materials and process development software for LPBF which lets users optimize laser and material parameters for difficult-to-print features. Through this Consortium Dyndrite’s tools can be used to accelerate materials parameter development for leading metal 3D printers.
The Chief Technology Officer of Elementum 3D, Dr Jeremy Iten said: “Dyndrite surpassed our previous capability for supportless low angle features, thus expanding the range of applications favoring additive manufacturing. Dyndrite is helping Elementum 3D deliver a more effective product to our customers.”
Dyndrite and other AM companies of the Consortium are showcasing their products at Formnext.
Remember, you can post job opportunities in the AM Industry on 3D ADEPT Media free of charge or look for a job via our job board. Make sure to follow us on our social networks and subscribe to our weekly newsletter : Facebook, Twitter, LinkedIn & Instagram ! If you want to be featured in the next issue of our digital magazine or if you hear a story that needs to be heard, make sure to send it to contact@3dadept.com