In general, materials are so complex that they often lead to longer product cycle times when the appropriate material has not been leveraged or used properly. In additive manufacturing, that complexity is even more pronounced because not only the technology does not have one unique guideline, but the manufacturing process sometimes, requires the combination of several materials or simply more accuracy to deliver the complex structures of a part.
Materials science and engineering is therefore a whole world that AM operators need to understand. To discuss a bit of this world and how it is important to AM specialists, we’ve invited Malvern Panalytical in this Opinion of the Week series.
As a provider of scientific instrumentation for the chemical, physical and structural analysis of materials, Malvern Panalytical enables scientists & engineers to better understand materials, products or processes.
Dr. John Duffy, Sector Marketing Manager, answered our questions as part of this Opinion of the Week. Duffy holds a degree in Chemistry and a PhD in Chemical Engineering from the University of Nottingham. He has started as a rheology specialist at Malvern, previously known as Malvern Instruments. To date, it’s been 11 years that he joined the structure and over time, he has witnessed AM become an important growth area for the organization.
Those parameters that do not seem important, yet they are crucial for AM
Beyond their instruments, Malvern Panalytical is acknowledged for the technical know-how they provide. Their instruments are used in various industries and applications. While the requirements are usually the same, it is possible to observe some specific requirements in certain sectors.
Put simply, the company enables engineers to learn and master techniques for measuring particle size, particle shape, elemental composition, crystallographic structures and properties such as molecular weight and Zeta potential.
As far as AM is concerned, their services depend on several factors including the type of manufacturing process or the type of materials leveraged.
“For example, characterization requirements for material jetting or material extrusion will be different than powder bed processes, while characterization requirements for metals may be different than for polymers. We have solutions for polymers and metals, and for liquids, solids and powders, so we can address several different challenges within the additive manufacturing industry”, explains Duffy.
Taking the example of the Mastersizer 3000 laser diffraction system, the specialist explains that this device serves for measuring particle size distribution whereas a device like the Morphologi 4 analyzer serves for measuring particle shape.

“Particle size and shape are important parameters for all powder bed processes whether the material is a ceramic, polymer or metal powder, as these parameters greatly influence powder packing and flowability. Powders that pack consistently well to give a high density are associated with the production of components with fewer flaws and consistent quality, while the ability to spread the powder evenly and form a uniform layer with no air voids is of critical importance”, completes the spokesperson.
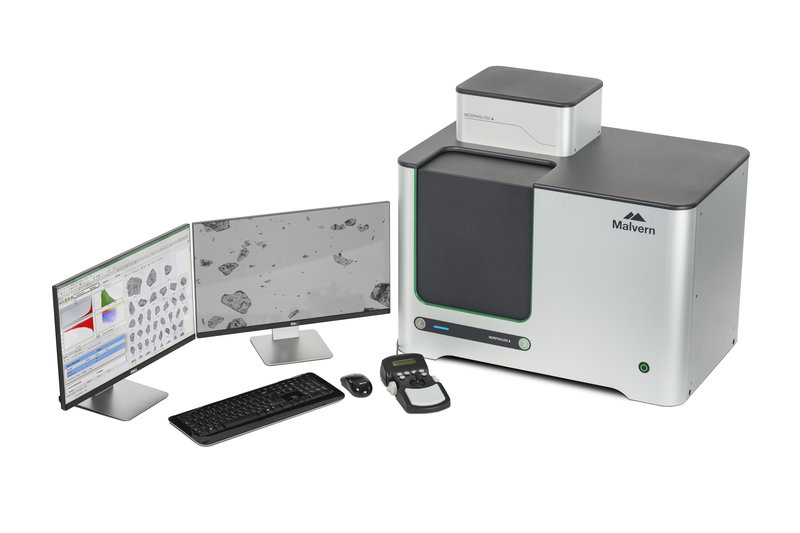
A matter of chemistry
Next to particle size and particle shape is chemistry.
Imagine you leverage a powder whose alloy composition does not comply with the ideal material for your production, you are likely to get a finished part that does not integrate the desired properties.
To avoid this situation, the materials specialist should take advantage of a solution that can accurately determine the majority of alloying elements in a sample. Once such type of analysis is performed, measurements can easily be performed.
Furthermore, sometimes the rapid heating and cooling in the build environment can lead to residual stresses that can also affect mechanical properties. To avoid this situation, the materials specialist or engineer should determine the crystallographic structure of both metal powders and fabricated parts.
Each of these situations requires the use of specific instruments that Malvern Panalytical can provide. They include for instance, X-ray fluorescence (XRF) solutions as well as X-ray diffraction (XRD) instruments.
“Residual stress and stress gradients can be measured by XRD, as well as texture – the non-random distribution of crystallographic planes in a material, which can affect properties directionally. XRD can also be used to measure the microstructure of semi-crystalline polymers, but the most common tool we provide for looking at polymer structure is Gel Permeation Chromatography (GPC) with advanced detection. This technique can be used to determine the molecular size, weight and structure of a wide range of macromolecules, used in processes such as vat photopolymerization, Selective Laser Sintering (SLS), binder jetting, material jetting and material extrusion”, explains Malvern Panalytical’s John Duffy.
Particle size, particle shape and chemistry are in the end, a few examples that highlight the importance of probing and measuring a material’s structure and properties prior to manufacturing. Hence the term materials characterization.
Impact & challenges in AM
In additive manufacturing especially, it should be noted that “the biggest source of variability comes from the materials, which means that inconsistent material properties will give inconsistent finished component properties”.
According to the Sector Marketing Manager, “this becomes even more critical for powder bed processes since there are more material variables and process interactions that can affect the final component, such as particle size, particle shape, porosity, chemistry, thermal properties and presence of impurities.
Characterization is not just important for validating the supply chain but plays a vital role in new materials development also, such as developing new alloys, polymers or composites. If additive manufacturing is to realize its full potential, then we will need a bigger library of materials to choose from in the future and that means significantly more emphasis on research and development. Many of our instruments are sold for this purpose also, as there is a need to iteratively test and validate materials throughout the development process”.
In terms of tools, engineers can leverage the same devices to study the materials’ structures. However, the main difference at the technical level remains chemistry. Indeed, while metallic powders are crystalline and include an ordered arrangement of atoms, polymers on the other side, are long chain macromolecules that are amorphous or semi-crystalline in nature.
“The type of process will also influence the type of characterization technique. For powder bed processes, particle size and shape are considered important, independent of whether the powder is a polymer, ceramic and metal. For processes like material jetting or extrusion, then viscosity and rheology of the material needs to be assessed, which are very much related to the properties of the constituent polymers”, completes Dr. Duffy.
This Opinion of the Week reminds that AM is not only about manufacturers, materials producers or software publishers. The value chain keeps growing and every player that joins this industry addresses an issue that enables to better master the entire AM process. Malvern Panalytical is one of those players today.
To date, Dr. Duffy revealed that the largest challenge is keeping up with the industry to be able to develop increasingly cost-effective, accurate, intuitively designed instrumentation and software to address their customers pains and needs.
“To realize the potential of additive manufacturing, more emphasis will need to be placed on materials used in terms of process compatibility, consistency and functionality. Characterization of materials will therefore be critical to the success of additive manufacturing and we at Malvern Panalytical are excited to be part of this revolution”, concludes Dr. Duffy.
Remember, you can post free of charge job opportunities in the AM Industry on 3D ADEPT Media or look for a job via our job board. Make sure to follow us on our social networks and subscribe to our weekly newsletter : Facebook, Twitter, LinkedIn & Instagram ! If you want to be featured in the next issue of our digital magazine or if you hear a story that needs to be heard, make sure to send it to contact@3dadept.com