Throughout last year, several applications we covered as well as an exclusive dossier on the topic confirmed that Directed Energy Deposition (DED) 3D printing (often calls interchangeably WAAM) is rising. For this year, I had to wait until the end of this first semester to see exciting announcements in this field of activity.
The first one comes from Cranfield University spin-out WAAM3D that has launched a new metal 3D printing platform; the other comes from Sciaky, Inc., a subsidiary of Phillips Service Industries, Inc. (PSI) which announced that its Electron Beam Additive Manufacturing (EBAM®) technology process deposited 40 lbs. (18.14 kg) of titanium per hour. If true, this deposition record would be the highest – and fastest – in the world right now.
WAAM3D’s metal 3D printing platform
Unveiled at TCT 3Sixty 2022 last week, and named RoboWAAM, the new machine brings a combination of sensing hardware and software developments which can be easily reconfigured to accommodate wide-area parts with tooling of various sizes, or rotational components.
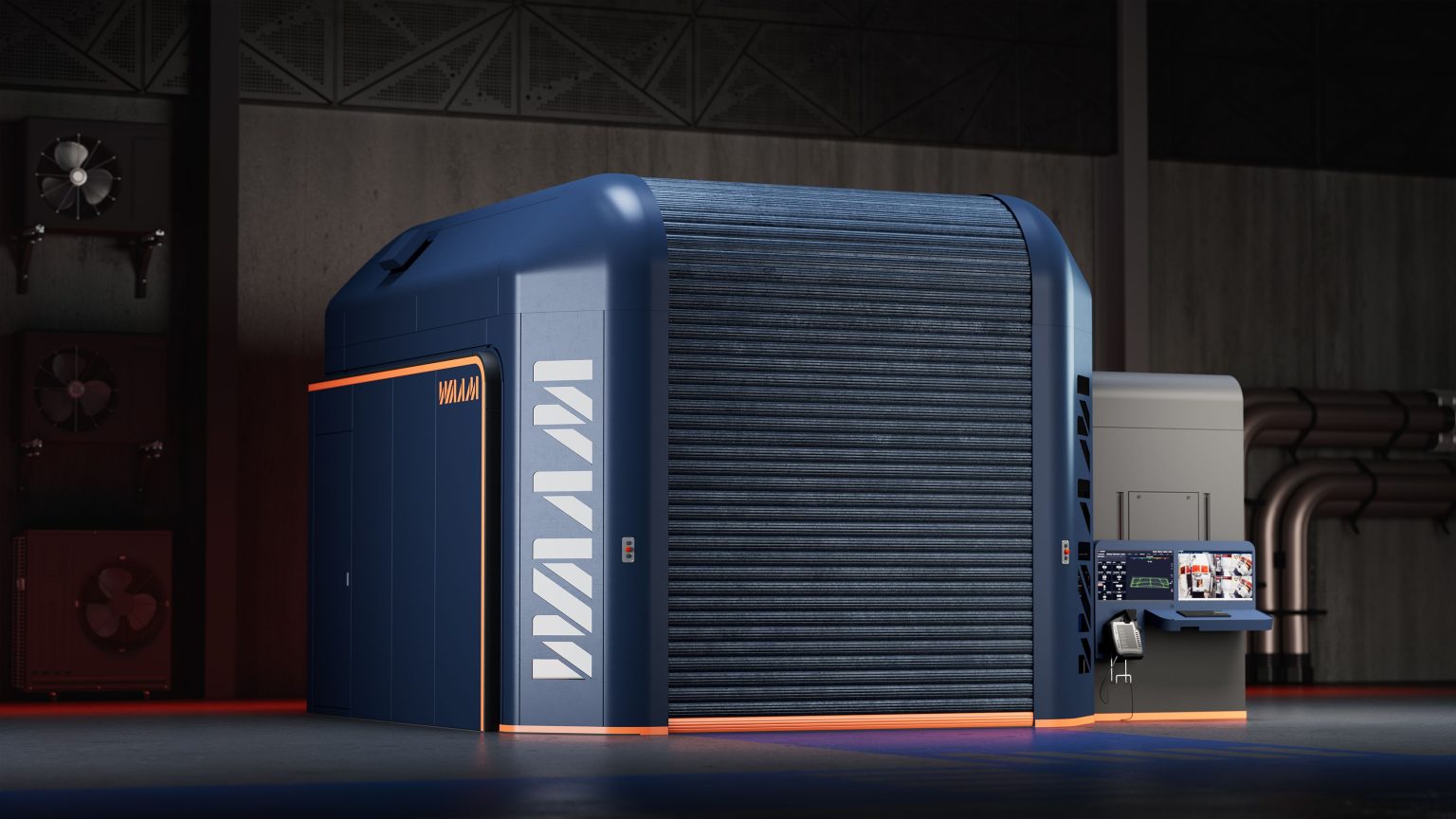
With a maximum build envelope of 2 x 2 x 2 metres and a large material spool capacity of 70kg, WAAM3D states the machine can process virtually any wire form material. The machine manufacturer has also integrated a new double-point temperature measurement feature that controls the deposition printing parameters and checks the parameters for reliability in-situ.
“It works seamlessly with the programmes generated by WAAMPlanner. It is managed by WAAMCtrl, the operating system overseeing the whole of the build process, providing process monitoring and governance over the many health and safety capabilities, as well as fully auditable process trail. Our 20 years of experience has enabled us to design 80% of the components from scratch to create a truly coherent hardware and software ecosystem”, the team says.
What makes this machine different from a robotic welding cell is a dedicated Fume Management System for containment, filtration, and treatment. On a safety note, it should be noted that the machine enables automatic purging, atmosphere maintenance, and evacuation cycles in order to safely process reactive materials. Other functions interesting to note – speaking of the difference with a robotic cell – are its large wire payload capabilities and a self-lacing wire reloading system.
Furthermore, with an integrated real time interferometric sensor called ShapeTech, the The RoboWAAM can reconstruct the 3D profile of the deposited structure and extract the layer height value all around the part to provide in-progress and immediate confidence in consistency of deposition.
Sciaky’s highest and fastest deposition rate
The Saint Exupéry Institute for Research in Technology (IRT), located in France, achieved EBAM’s high deposition rate (HDR) while conducting work for its Metallic Advanced Materials for Aeronautics (MAMA) project. Launched in 2019, one of MAMA’s initial goals was combining die forging with metal 3D printing to develop a new process for manufacturing titanium aircraft parts.
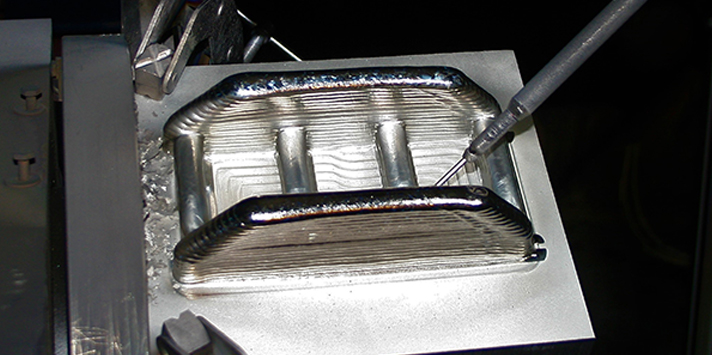
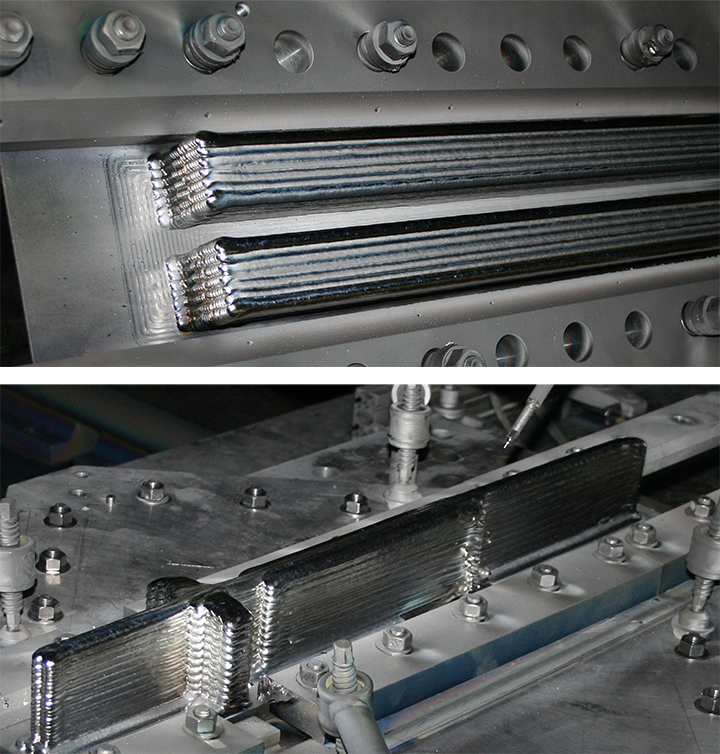
To date, Sciaky’s EBAM has deposited over 330 lbs. (150 kg) of Ti-6AI-4V (titanium) for three different MAMA applications. Additional projects are planned for 2022 and beyond, with a groundswell of support to adopt these new processes into production. Airbus and Aubert & Duval are also key process contributors for this particular initiative of the MAMA project.
Sciaky’s EBAM systems can produce parts up to 19 feet (5.79 meters) in length. EBAM brings quality and control together with IRISS® – the Interlayer Real-time Imaging and Sensing System, a real-time adaptive control system that can sense and digitally self-adjust metal deposition with precision and repeatability. This innovative closed-loop control is the primary reason that Sciaky’s EBAM 3D printing process delivers consistent part geometry, mechanical properties, microstructure, and metal chemistry, from the first part to the last, Sciaky says in a press release.
Remember, you can post job opportunities in the AM Industry on 3D ADEPT Media free of charge or look for a job via our job board. Make sure to follow us on our social networks and subscribe to our weekly newsletter : Facebook, Twitter, LinkedIn & Instagram ! If you want to be featured in the next issue of our digital magazine or if you hear a story that needs to be heard, make sure you send it to contact@3dadept.com