Dans une industrie où la croissance de la FA est souvent mise en évidence par une forte concentration sur les métaux, les polymères restent le groupe de matériaux le plus utilisé, toutes applications confondues. Des industries telles que l’aérospatiale, l’automobile et le biomédical explorent les applications des pièces en polymères à haute température avec la FA, mais un fossé doit encore être comblé pour qu’elles puissent atteindre la production en série.
Soyons clairs : de nombreux exemples ont déjà démontré que des polymères de haute performance traités par FA ont permis la fabrication d’outillages ou d’applications finales. Le fait est que, pour que ces matériaux soient considérés comme un substitut des métaux, pour qu’ils puissent fournir des pièces de grande valeur dans des séries de production à faible quantité, ils doivent répondre à un certain nombre d’exigences.
Cet article a pour ambition de présenter les défis que les fabricants doivent encore relever lorsqu’ils adoptent les polymères haute performance dans la production en série, ainsi que ceux que ces matériaux peuvent déjà résoudre au niveau de la fabrication.
Plusieurs contributions ont été envisagées, mais Sylvia Monsheimer, responsable de l’impression 3D industrielle et des nouvelles technologies 3D chez Evonik, a été invitée à partager ses idées clés avec Ralf Anderhofstadt, responsable du centre de compétences Fabrication additive, atelier d’impression et médias chez Daimler Trucks & Buses.
Evonik Industries AG est une société allemande de produits chimiques spécialisés cotée en bourse, qui développe et commercialise l’un des portefeuilles les plus complets de solutions matérielles dans l’industrie de la FA sous la marque INFINAM®. En ce qui concerne les matériaux, les poudres de polyamide 12 de haute qualité de la société sont reconnues pour leurs applications polyvalentes dans l’industrie de la FA. L’expérience de l’entreprise dans le développement de matériaux d’impression 3D à base de polymères nous permettra de nous mettre dans la peau d’un producteur de matériaux et de comprendre la complexité des polymères haute performance.
Daimler Trucks & Buses, quant à lui, apportera son expertise en tant qu’utilisateur de la FA. Pour beaucoup de gens, cette entreprise est le plus grand constructeur de véhicules commerciaux, avec plus de 40 sites de production dans le monde et plus de 100 000 personnes sur plus de 40 sites à travers le monde. Dans le domaine de l’impression 3D, le constructeur automobile bénéficie de plus de 25 ans d’expérience dans la construction de prototypes par impression 3D. Avec 50 000 pièces détachées de bus imprimables en 3D disponibles aujourd’hui, l’entreprise a surtout utilisé la FA dans la division après-vente, pour réagir rapidement et avec souplesse aux besoins urgents des clients, par exemple lorsque ceux-ci commandent des pièces rarement demandées ou ont des demandes spéciales.
Anderhofstadt nous a confié qu’ils travaillent actuellement avec de nombreux partenaires et prestataires de services, c’est pourquoi ils testent tous les processus de production additive et vérifient s’ils sont adaptés aux séries. Pour l’instant, ils se concentrent sur la SLS, la MJF et, bien sûr, la FDM, en fonction de l’application.
Comprendre le concept des polymères « haute performance »
Si vous êtes nouveau dans ce monde, veuillez noter que le terme « polymères » est souvent utilisé de manière interchangeable avec « plastiques ». Toutefois, nous utiliserons principalement le mot « polymères » dans cet article.
D’un point de vue technique, les polymères haute performance (HPP) sont un groupe de matériaux qui peuvent conserver leurs propriétés mécaniques, thermiques et chimiques souhaitables lorsqu’ils sont soumis à des environnements difficiles tels que des températures élevées, des pressions élevées et des produits chimiques corrosifs.
Si le terme « haute performance » est désormais naturellement utilisé dans le jargon scientifique et industriel, la vérité est qu’il ne s’agit pas d’un terme scientifique à proprement parler. Néanmoins, il permet de définir une catégorie spécifique qui se trouve à la tête d’une pyramide mettant en évidence les performances des polymères. Les polymères haute performance sont situés au sommet de la pyramide des polymères et sont directement suivis par les polymères techniques et les polymères de base/standard.
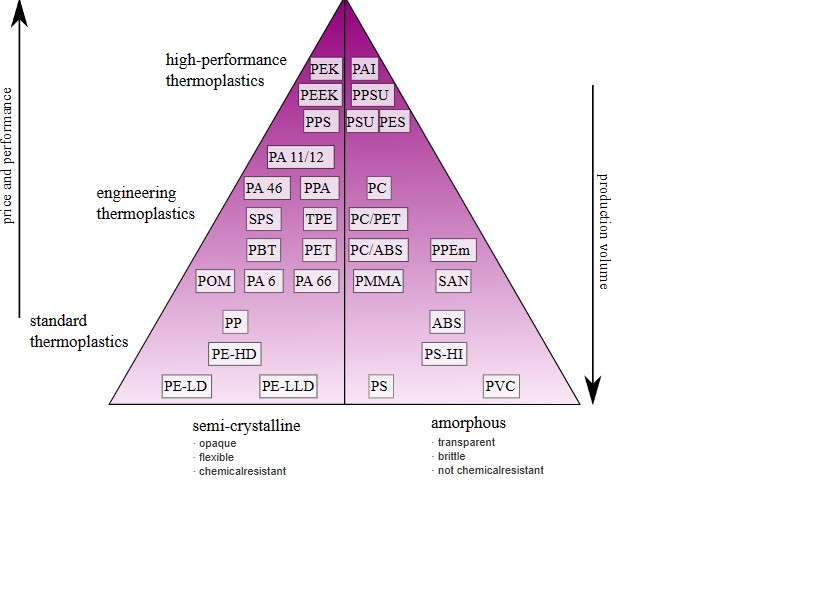
La dernière fois que nous avons vérifié, les polymères haute performance représentaient environ 700 000 tonnes, soit seulement 0,2 % de tous les polymères synthétiques. Ils sont généralement beaucoup plus difficiles à fabriquer. Comme ils sont basés sur des monomères plus complexes, ils s’avèrent assez coûteux. Cela dit, plus le matériau polymère est complexe ou difficile à produire, plus le polymère résultant est performant.
D’une manière générale, les polymères offrent beaucoup plus d’avantages que les métaux : ils sont plus résistants aux produits chimiques, ils ne nécessitent pas (beaucoup) d’efforts de finition après traitement, ils sont plus légers que les métaux typiques, ou ils sont naturellement absorbants pour les radars et isolants thermiques et électriques. Il est fascinant de constater que certaines de ces propriétés sont également recherchées dans les polymères haute performance développés pour la FA.
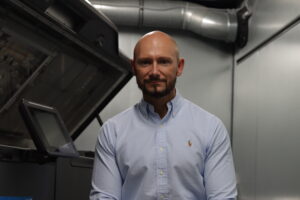
« Un avantage important réside dans la résistance aux hautes températures, raison pour laquelle ce type de matériaux est également très intéressant pour le secteur automobile. Les propriétés telles que la haute résistance à la traction et la haute résistance aux produits chimiques soulignent bien sûr cet aspect. Par conséquent, les polymères haute performance deviennent de plus en plus une alternative intéressante aux métaux », souligne l’expert de Daimler.
Fait surprenant, les propriétés qui rendent les polymères haute performance utiles sont souvent celles qui les rendent difficiles, voire impossibles à produire à l’aide des machines de FA courantes sans processus à haute température.
« Si nous parlons de production en série – des pièces qui sont produites pour une application finale – nous rencontrerons pas mal de défis : Nous ne devons pas seulement remplacer l’étape de construction d’une pièce, mais des ajustements des étapes du processus de production avant et après la construction d’une pièce doivent être envisagés et prouvés. En d’autres termes, nous devons travailler à l’intégration dans la chaîne de processus qui est principalement axée sur les applications. Et les solutions clés en main ne sont pas disponibles dans leur ensemble. Or, ce point est toujours sous-estimé », affirme d’emblée Monsheimer.
Anderhofstadt est d’accord avec elle puisqu’il insiste sur la nécessité de processus de libération techniques et qualitatifs : « pour les pièces de série, il est bien sûr essentiel d’obtenir 100 % des propriétés de la pièce dans le contexte global afin d’atteindre les normes de qualité. C’est également la base de la reproductibilité, qui est absolument nécessaire pour la production en série. »
Ajoutez à cela la « considération des coûts », et vous faites en sorte que la conversation englobe l’ensemble de la chaîne de fabrication :
« Un autre défi à coup sûr, ce sont les coûts de la solution globale d’impression 3D. La concurrence avec le moulage par injection est imbattable pour un grand nombre de pièces simples. Les technologies de fabrication additive en général offrent des avantages si on peut utiliser la liberté de conception ou si on peut réaliser des assemblages en une seule pièce. Dans ce cas, [il est nécessaire de revoir la conception de la ou des pièces en tenant compte de la FA]. Enfin, il manque encore des matériaux spéciaux pour des applications spéciales. C’est là que nous intervenons en élargissant continuellement notre portefeuille de matériaux d’impression 3D axés sur les applications », ajoute le représentant d’Evonik.
Alors, de quels défis s’agit-il ?
« Défis » est un grand mot qui est régulièrement utilisé dans tous les sujets liés à la FA. Dans ce cas précis, j’aimerais les considérer comme des limitations qui ouvrent de nouvelles perspectives aux utilisateurs de la FA.
La première chose que nous retiendrons du dernier commentaire de Monsheimer est le nombre limité de polymères à haute performance. Il est intéressant de noter que le processus n’est pas aussi simple que de créer des formes de polymères traditionnels utilisés dans le moulage par injection.
Le problème de la « délamination » au niveau de la fabrication. Selon le fabricant de machines Orion, les pièces qui sont spécifiquement fabriquées en PEEK souffrent souvent de ce problème. Cela signifie que les couches fusionnées qui construisent la forme finale ne sont pas correctement soudées ensemble. Ces pièces en PEEK défectueuses se comportent davantage comme une pile de tranches vaguement connectées que comme un ensemble continu. Ces propriétés mécaniques inégales sont appelées « propriétés anisotropes » et constituent un problème courant dans les pièces imprimées de nombreux fabricants. Ils ont pu explorer une nouvelle solution à ce problème lorsqu’ils travaillaient sur la FA des CubeSats, ces satellites miniatures et légers utilisés pour la recherche spatiale, l’observation de la terre ou les télécommunications. L’équipe a utilisé son système de chauffage par rayonnement thermique. Développé en interne chez Orion, il fusionne les couches entre elles tout en chauffant l’ensemble de l’objet et en dirigeant le rayonnement thermique vers la couche précédente avant le dépôt du nouveau matériau. Chaque couche du matériau imprimé est moulée sur la précédente grâce à un chauffage sélectif allant jusqu’à 300 °C. Cela garantit que les couches forment une seule pièce solide et continue. Il en résulte des composants imprimés en 3D plus solides, plus isotropes et prêts à être utilisés immédiatement, explique Orion.
Comme vous pouvez le deviner, si ce problème n’est pas résolu, il entraîne souvent des limitations liées à d’importants gradients thermiques, à l’accumulation de contraintes résiduelles et à l’adhésion entre les couches, ainsi qu’à l’incapacité des imprimantes 3D à maintenir en permanence les températures de traitement élevées requises. C’est la raison pour laquelle on n’insistera jamais assez sur la nécessité de collaborer entre les fabricants de matériaux et les fournisseurs de technologies, rappelle Monsheimer avant d’ajouter :
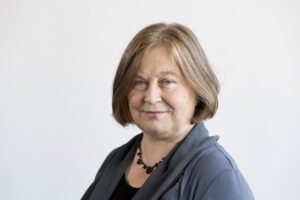
« Un bon matériau est clé ! Cela signifie qu’il faut disposer d’un matériau pouvant être traité en toute sécurité et répondant à tous les besoins des processus d’impression 3D ou de l’application concernée, au meilleur prix. Si ce rapport entre les propriétés du matériau et les coûts est atteint, nous pouvons commencer à travailler sur d’autres défis. »
Une autre limite se manifeste dans le type d’applications réalisées avec ces matériaux. Par exemple, en raison de leur faible rigidité structurelle, il est difficile ou rare de réaliser des structures lourdes avec des polymères. C’est la raison pour laquelle la plupart des applications sont présentées dans l’industrie des soins de santé, dans l’industrie de la bijouterie (Boltenstern, par exemple, offre des boucles d’oreilles ou des bracelets personnalisés en série dans différentes couleurs, fabriqués à partir du PA12 d’Evonik) ou à des fins de personnalisation dans d’autres industries. Dans l’industrie automobile, cependant, il y a de grands espoirs d’assister bientôt à quelques nouvelles applications :
« Nous procédons actuellement à des tests finaux sur des polymères à haute performance pour des applications de série. Les premières informations à ce sujet seront bientôt annoncées officiellement, car cette gamme est également très intéressante pour nous dans le secteur des camions et des bus.
Nous avons déjà installé plus de 50 000 pièces de série imprimées en 3D dans nos véhicules. Actuellement, l’accent est toujours mis sur le secteur des polymères, mais nous avons déjà mis en œuvre plusieurs applications de série en différents métaux. Outre les supports, divers couvercles et inserts de poignée dans le domaine du métal, les pièces typiques sont également des supports ou divers composants sur le système d’échappement », s’enthousiasme Anderhofstadt.
À l’avenir, et en ce qui concerne l’industrie automobile, Anderhofstadt souligne la nécessité de disposer de polymères à haute performance pour répondre à d’autres exigences :
« Je pense fortement à des propriétés telles que la protection contre le feu et donc le retardement des flammes des matériaux. Et bien sûr, cela doit aussi être en accord avec les objectifs de durabilité. Enfin, pour la production en série, il est essentiel que ces matériaux puissent être utilisés pour une production économique », complète-t-il.
Monsheimer ne peut le contredire sur le point de la durabilité – puisqu’elle souligne également cette préoccupation. En effet, l’empreinte carbone et/ou l’élimination peuvent être des problèmes critiques, car certains polymères ne peuvent pas être recyclés alors que tous les métaux le peuvent. Cependant, certains producteurs de matériaux ont commencé à prendre des mesures pour résoudre ce problème – et Evonik en fait partie comme vous avez pu le lire dans ce numéro de 3D Adept Mag (page 17).
« Après le prototypage, les applications constituent le prochain défi pour les matériaux, car ceux-ci doivent désormais être optimisés pour des applications particulières », conclut Monsheimer.
Ce dossier a été initialement publié dans le numéro de Janvier/Février de 3D ADEPT Mag.