Les pièces automobiles ont-elles été un espace difficile pour la croissance de la fabrication additive (FA): le cas de Toyota
Lorsque j’ai commencé à couvrir l’industrie de la fabrication additive, l’une des premières choses que j’ai apprises est que l’automobile reste sur la liste des trois secteurs verticaux qui adoptent le plus cette technologie. Plus je regarde de près, plus je me rends compte que les pièces automobiles ont été un espace difficile pour la croissance de la FA. Cette difficulté est-elle liée aux défis rencontrés dans les applications complexes que les industriels souhaitent réaliser ? Ou s’agit-il d’une question de modèle économique ? Nous avons répondu à ces questions en nous concentrant sur l’histoire de Toyota.
Pourquoi Toyota, me direz-vous ?
Parce que « Toyota a commencé à explorer la fabrication additive au début des années 2000, d’abord pour le prototypage rapide. L’expansion des applications de production et l’utilisation plus large des technologies de fabrication additive ont commencé à prendre de l’ampleur dans les années 2010 », a déclaré William (Dallas) Martin à 3D ADEPT Media , ingénieur en fabrication additive au sein de l’entreprise. L’entreprise a commencé son parcours à une époque où les gens ne croyaient pas beaucoup à la technologie, mais aujourd’hui, son utilisation de la technologie est globale.
« L’entreprise a intégré la FA dans diverses installations à travers le monde à des fins de prototypage, d’outillage et même de production de pièces fonctionnelles dans certains cas. Son approche globale permet de rationaliser la production, de réduire les coûts et d’explorer des conceptions innovantes sur différents marchés et dans différentes usines de fabrication », ajoute Dallas Martin.
Cette capacité à explorer la FA depuis si longtemps et à des fins différentes peut nous éclairer sur les raisons pour lesquelles les pièces automobiles ont été un espace difficile pour la croissance de la FA.
La perspective technologique
Tout d’abord, l’utilisation de la FA par Toyota dans le monde entier illustre les différents angles qui peuvent façonner l’histoire d’une entreprise avec la technologie. Alors qu’en Asie, et plus particulièrement au Japon, nous avons mis l’accent sur l’utilisation de la FA des métaux par l’entreprise, en Europe, nous avons beaucoup parlé de son utilisation de la technologie FDM en particulier.
William Dallas Martin, qui a dirigé les initiatives de l’entreprise en matière de FA au TILT Lab de Toyota – où il a contribué à créer le premier espace de création interne de l’entreprise – a déclaré à 3D ADEPT Media que le constructeur automobile « possède plus de 200 imprimantes 3D dans le monde, utilisant diverses technologies telles que la modélisation par dépôt de matière fondue (FDM), la stéréolithographie (SLA), le frittage sélectif par laser (SLS) et le frittage direct par laser de métal (DMLS) ».« Ces imprimantes sont utilisées pour le prototypage, l’outillage et même la production de pièces fonctionnelles, ce qui contribue à améliorer l’efficacité et l’innovation dans leurs processus de fabrication », explique-t-il.
Si la fabrication additive (FA) gagne du terrain dans les applications mentionnées par Dallas Martin, son utilisation dans la fabrication automobile complexe se heurte à des difficultés considérables. Les propriétés et la certification des matériaux, le contrôle et la répétabilité des processus, ainsi que la vitesse de production et l’évolutivité, restent des obstacles majeurs, en particulier d’un point de vue technologique. Une analyse complète du problème inclurait les contraintes de coût, mais ce sujet nécessiterait un chapitre entier.
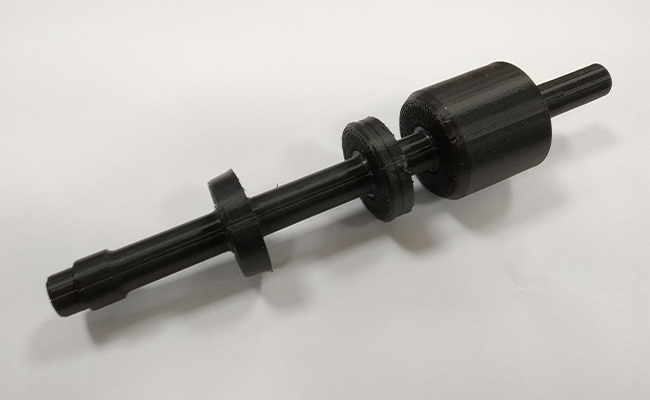
Prenons par exemple les propriétés et la certification des matériaux. De nombreux matériaux d’impression 3D ne présentent pas la solidité, la résistance à la fatigue et la stabilité thermique requises pour les applications automobiles, en particulier dans des conditions extrêmes (par exemple, les composants du moteur et les pièces structurelles).
Imaginons une entreprise qui doit produire 500 exemplaires d’une pièce spécifique sur une période donnée. Il est important que ces pièces soient fabriquées sur une imprimante 3D spécifique avec un matériau qui a été testé, certifié et normalisé pour cette application. Cependant, les choses peuvent devenir complexes si, pendant cette période, le producteur du matériau change la recette de ce matériau, obligeant toute l’équipe à recommencer le processus.
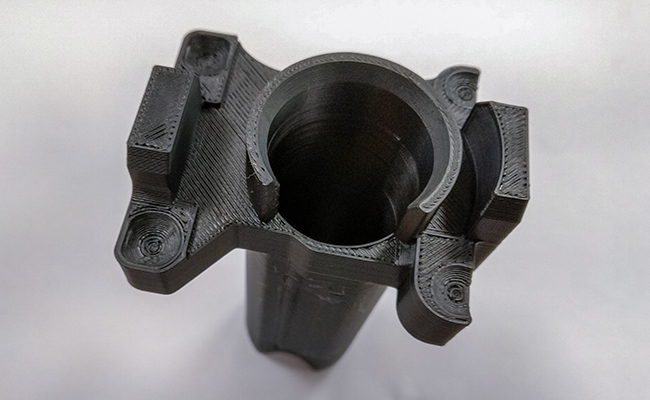
Cette difficulté est-elle donc liée aux défis rencontrés dans les applications complexes que les industriels souhaitent réaliser ? Pour Dallas Martin, une pièce complexe n’est pas souvent la plus difficile à réaliser :
« La pièce la plus complexe sur laquelle j’ai travaillé est une pièce de production qui a contribué à changer la perspective des gens sur la fabrication additive. En éliminant le besoin d’outillage traditionnel et en réduisant les délais d’exécution, elle a montré comment la fabrication additive pouvait réduire les coûts tout en respectant les normes industrielles. Le plus difficile a été de faire passer la fabrication additive par le processus PPAP ou SQAM. Le respect de toutes les normes et de tous les contrôles de qualité requis lors de la mise en œuvre de la fabrication additive en production a constitué un obstacle important, mais il s’agit d’une étape cruciale pour valider son utilisation dans le secteur de la fabrication. »
Des modèles d’entreprise en évolution ?
Comme le montre le tableau ci-dessous, si Toyota n’a pas recours à la FA pour la production de véhicules à grande échelle, elle a intégré l’impression 3D dans divers aspects de son processus de fabrication.
Dates | Phases | Détails |
Début 2000 | Phase de prototypage | Tests des designs |
2010 | Outillage et personalisation |
– Fabrication des gabarits et des fixations – Exploration des pièces structurelles légères |
2020 | Pièces de rechange et mobilité du futur |
– L’utilisation de l’impression 3D pour les pièces de rechange à la demande, en particulier pour les anciens modèles de véhicules et les voitures de collection. – L’utilisation de la FA pour les véhicules électriques (VE) et les solutions de mobilité autonome, telles que les composants de châssis légers. – En 2021, la division Lexus de Toyota a utilisé la FA pour produire des pièces légères et performantes pour des véhicules conceptuels. |
Légende : Principales étapes de l’adoption de la FA par Toyota
Dans son discours au CES 2018, Akio Toyoda, président de Toyota Motors et petit-fils du fondateur de l’entreprise, a déclaré que son objectif était de « faire passer Toyota d’une entreprise automobile à une entreprise de mobilité » – soulignant sa détermination à « créer de nouvelles façons de déplacer et de connecter [leurs] clients à travers le pays, à travers la ville, ou juste à travers la pièce. » Pour que cette vision devienne réalité, il faudrait explorer des solutions de transport qui aillent au-delà de la vente de véhicules – des solutions dont l’approche technologique met l’accent sur la connectivité, les VE ou même la conduite autonome. »
Ces idées pourraient conduire à une utilisation accrue de la FA. Si nous prenons l’exemple des véhicules électriques (VE), Dallas Martin pense que la technologie peut contribuer à réduire le poids de certaines pièces de VE, à créer des conceptions plus efficaces et à permettre un prototypage plus rapide.
« Elle est particulièrement utile pour produire des composants complexes et légers qui améliorent l’efficacité des batteries, des systèmes de refroidissement et des pièces structurelles. En outre, la FA peut permettre de fabriquer des pièces personnalisées et de réduire la complexité de la chaîne d’approvisionnement, ce qui est crucial pour la production de VE », note-t-il.
Même si je suis d’accord avec lui, je ne peux m’empêcher de penser que l’utilisation de la FA reste très théorique sur ce sujet spécifique – soit nous n’avons pas assez de conversations, soit celles que nous avons ne sont pas les bonnes.
L’un des moyens de favoriser un véritable partage des connaissances sur le sujet serait de participer à des événements industriels où les fournisseurs de technologie de FA et les utilisateurs (potentiels) pourraient discuter sans « aucune pression commerciale ». AMUG en est un en occurence, selon les termes de Martin, « c’est un environnement de collaboration avec des ingénieurs d’application et des utilisateurs comme [lui] ».
« C’est un environnement collaboratif où vous pouvez acquérir des connaissances pratiques, nouer des liens pour la vie et prendre des décisions éclairées sans être soumis à la pression des vendeurs. C’est une expérience que vous ne regretterez pas », a-t-il déclaré.
En attendant, pour répondre aux questions susmentionnées, l’utilisation de la fabrication additive par Toyota est influencée à la fois par des défis techniques et des considérations de modèle commercial. D’un point de vue technique, l’obtention des propriétés des matériaux et de la précision requise pour les pièces produites en grande quantité reste un obstacle. Sur le plan commercial, la dépendance de l’industrie automobile à l’égard des économies d’échelle rend la fabrication additive plus adaptée au prototypage et aux composants de faible volume.
Contenu rédigé en collaboration avec AMUG.