Avec des entreprises privées à l’avant-garde des récentes innovations spatiales, l’industrie spatiale connaît un changement de paradigme induit par des offres de solutions de marché perturbatrices et des approches industrielles qui n’étaient pas souvent envisagées par les gouvernements. Ce qui est intéressant dans ce nouveau paradigme, c’est qu’il ouvre de nouvelles portes aux innovations technologiques et positionne les nouveaux entrants dans le domaine spatial comme des experts dans d’autres industries verticales. Dans cette optique, 3D ADEPT Media aborde l’utilisation actuelle des technologies de fabrication additive chez Virgin Orbit et certains des défis auxquels l’industrie spatiale est confrontée dans l’adoption de ces technologies.
Il y a trois ans, Virgin Orbit a fait ses débuts dans le secteur très sélect des petits satellites avec pour objectif de fournir le lanceur de satellites le plus flexible et le plus réactif jamais inventé. Pour mener à bien cette mission, l’entreprise du groupe Virgin avait travaillé sur une fusée LauncherOne pour petits satellites, une fusée à lancement aérien vers l’orbite, conçue pour mettre en orbite des charges utiles de petits satellites de 300 kilogrammes (660 lb) et plus.
Après une première tentative infructueuse, la start-up spatiale a finalement fait honneur à son nom puisque le 17 janvier 2021, elle a atteint son orbite, déployant avec succès 10 CubeSats en orbite terrestre basse. Cette étape était d’autant plus importante pour l’expert spatial que c’était la première fois qu’il lançait dans l’espace des satellites fonctionnels pour le compte de la NASA.
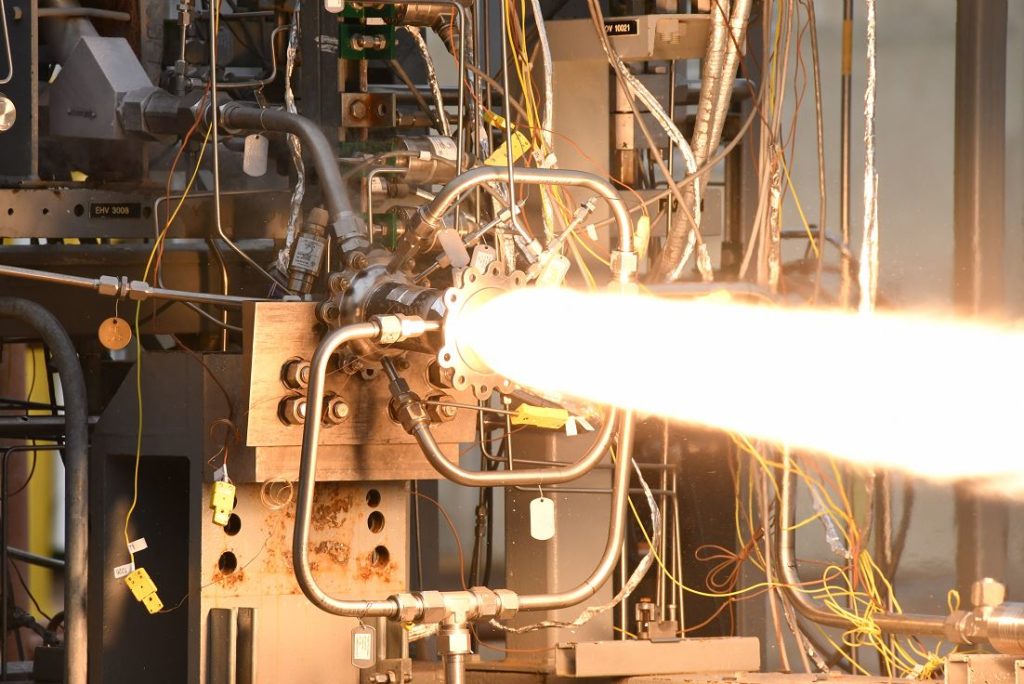
Si la réussite du lancement est due à une technique dite d’aérolancement**, la vérité est que si le fournisseur de services de lancement de petits satellites devient un pionnier très médiatisé de cette nouvelle course à l’espace commercial, c’est aussi parce qu’au cœur de certains de ses projets de fabrication, la fabrication additive a toujours été reconnue comme un facilitateur clé.
« Chez Virgin Orbit, notre objectif est de contribuer à l’avenir de l’humanité dans l’espace. Nous aidons nos clients à changer le monde en augmentant les cadences de fabrication de nos fusées tout en réduisant le coût par lancement. Pour ce faire, nous nous appuyons sur des techniques et des technologies de fabrication avancées pour fabriquer des composants de propulsion ainsi que d’autres composants complexes qui peuvent être intégrés dans une fusée, déclare d’emblée Oluseun Taiwo, ingénieur en fabrication avancée de propulsion.
Virgin Orbit est apparu pour la première fois dans notre radar lorsque le Marshall Space Center de la NASA a annoncé qu’ils devaient explorer ensemble l’impression 3D multi-métal pour construire des chambres de combustion multi-métalliques.
Le projet était d’autant plus important pour l’équipe de Virgin Orbit que les informations obtenues dans le cadre de ce partenariat seraient essentielles pour appliquer les technologies de FA « afin d’améliorer encore le coût, les performances et les délais de [ses] systèmes de propulsion pour le véhicule LauncherOne ».
Les pièces multi-métalliques constituent une amélioration significative dans la production des chambres de combustion des moteurs de fusée, car elles répondent principalement aux exigences en matière de propriétés des matériaux (telles que la résistance ou la conductivité thermique) – exigences que Virgin Orbit a pu satisfaire dans ce cas en utilisant un système interne de fabrication hybride additive-soustractive.
Ceci étant dit, nous avons remarqué que les technologies de fusion en lit de poudre et de FA DED sont aussi souvent mises en avant comme l’une des technologies de FA les plus utilisées en interne – en particulier pour la production de détails complexes et de canaux de refroidissement dans les chambres de poussée et les injecteurs. Lorsqu’on lui demande les raisons pour lesquelles ils se sont concentrés sur ces technologies, Taiwo répond :
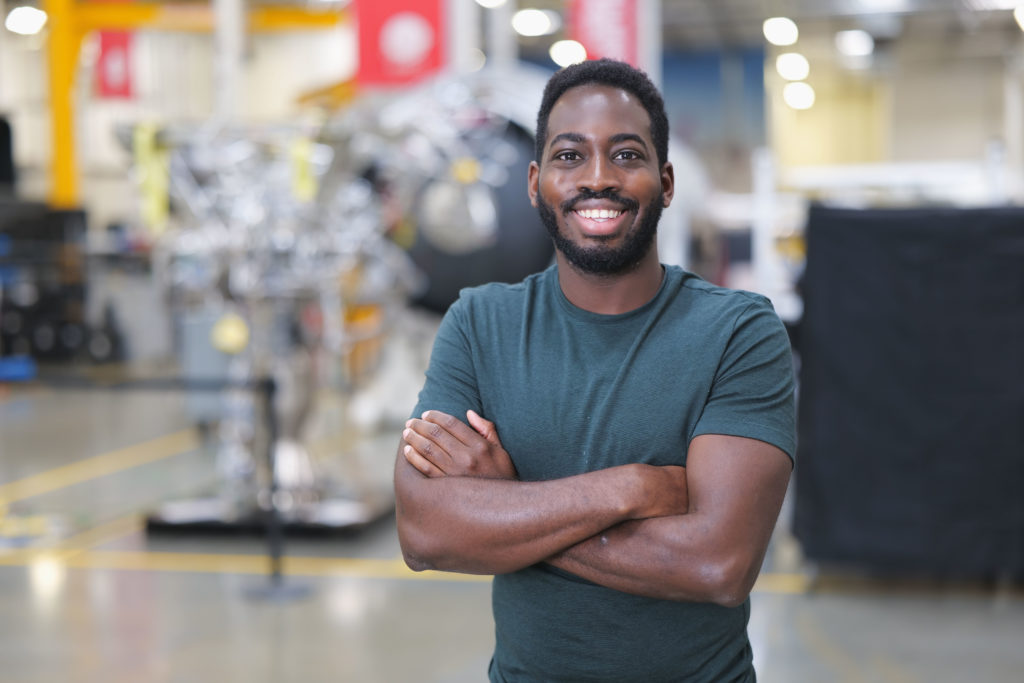
« La FA DED nous permet de fabriquer des pièces massives très rapidement. Les taux de dépôt que vous réalisez sur ces machines sont assez rapides. Il serait difficile de trouver un autre procédé de FA qui puisse battre les procédés DED en termes d’uniformité lorsqu’il s’agit de produire des pièces massives. Le DED nous permet également de créer des solutions multi-matériaux pour des processus très difficiles. Par exemple, ce procédé permet de réduire le poids de certaines pièces essentielles et d’améliorer les performances d’autres.«
« La fusion sur lit de poudre, quant à elle, permet de créer des géométries complexes de haute qualité, sans oublier qu’elle peut également traiter un grand nombre de matériaux. Nous avons souvent utilisé cette technologie pour la fabrication de chambres de poussée complexes avec canaux de refroidissement ou de turbomachines. Dans le cas des chambres de poussée dotées de canaux de refroidissement, par exemple, le fait de pouvoir fabriquer de telles pièces en une seule fois représente un gain de temps considérable », explique l’ingénieur.
Les principales complexités de l’utilisation de la FA dans l’espace.
Les satellites à bas coût et les fusées plus légères sont généralement mentionnés comme l’une des premières applications de la FA dans l’industrie spatiale, mais nous sommes encore loin d’une utilisation « naturelle » de la FA. En effet, les ingénieurs ont encore plusieurs défis de fabrication à relever.
Pour que les entreprises spatiales puissent lancer facilement des satellites, des sondes, des télescopes ou des engins spatiaux en orbite, elles doivent faire face au coût élevé par kilogramme nécessaire pour s’affranchir de l’attraction gravitationnelle de la Terre.
En d’autres termes, les coûts des missions peuvent être accélérés de plusieurs ordres de grandeur pour chaque kilogramme supplémentaire de charge utile. Le poids est sans aucun doute le premier défi que la FA peut surmonter, mais d’autres entrent inévitablement en jeu.
Selon Taiwo, l’uniformité des matériaux figure en tête des défis que les ingénieurs spatiaux rencontrent habituellement lors de la fabrication. « Nous devons être en mesure de produire des composants de propulsion ou structurels reproductibles, qui peuvent être très complexes en fonction du processus de fabrication utilisé. La complexité dépend de plusieurs facteurs et nous devrions être en mesure de tirer parti de la fabrication et de produire du matériel qui ne fonctionnera pas qu’une seule fois », explique l’ingénieur.
En outre, comme nous l’avons vu dans la plupart des industries, Taiwo décrit la « conception pour la FA » comme une autre complexité de l’utilisation de la FA dans l’industrie spatiale. La réalité montre que les applications spatiales telles que les lanceurs et les systèmes de satellites sont produites en petits lots mais qu’elles doivent faire face aux conditions et exigences extrêmes du lancement, sans oublier qu’elles peuvent être utilisées pendant plus de 15 ans après une mise en orbite réussie.
Contrairement à d’autres industries, « la FA des métaux n’en est encore qu’à ses débuts dans ce domaine. Du point de vue de la conception technique, la FA augmente la possibilité d’appliquer de nouvelles stratégies logicielles telles que l’optimisation de la topologie [car elle offre la possibilité de fabriquer avec un poids minimal en résolvant les problèmes de distribution des matériaux]. Du point de vue de la conception, nous n’en sommes pas encore là. En général, les ingénieurs spatiaux essaient encore de comprendre où ils doivent pousser dans leurs conceptions pour mieux contrôler le processus de fabrication. Cependant, j’aime l’approche que nous avons chez Virgin Orbit, car nous innovons autant que possible en posant des questions et en examinant minutieusement les processus. Nous apportons des technologies en interne et nous consacrons du temps au développement – et chaque fois qu’il y a un certain changement, nous le traitons comme un processus entièrement nouveau. Cette démarche consciente, pour certaines personnes, ne fonctionne pas, mais pour nous, elle fonctionne. »
Ce défi de la DfAM dans les applications spatiales a été confirmé par d’autres ingénieurs de l’espace. En fait, pour la plupart des ingénieurs, la conception en fabrication additive est difficile car elle implique un processus de désapprentissage des directives de conception de la fabrication conventionnelle. En outre, les procédés de fabrication additive existants révèlent une variation des produits imprimés, qui peuvent être différents d’une pièce à l’autre ou d’une machine à l’autre.
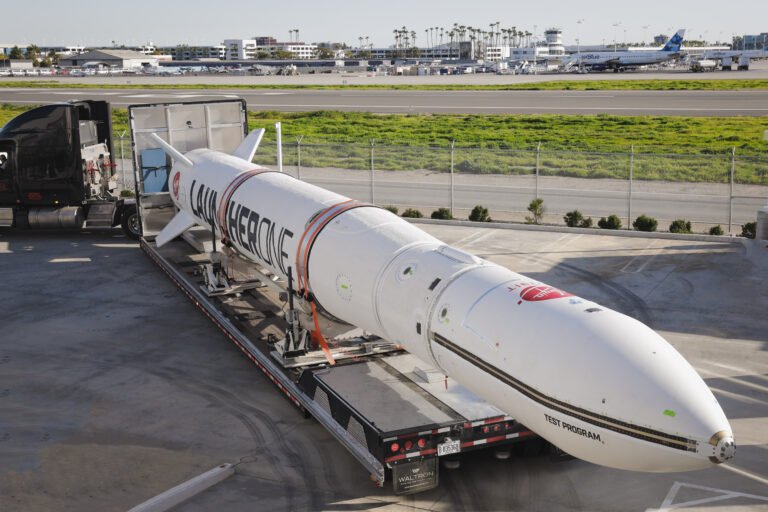
Il existe plusieurs approches différentes pour la DfAM et, comme nous l’avons compris des commentaires de Taiwo, il n’existe pas encore de ligne directrice définie pouvant être utilisée par toutes les entreprises. Cependant, une méthode souvent utilisée par les concepteurs consiste à définir la candidature à la FA par le biais de l’approche d’analyse de la conception. Cette approche consiste à identifier les pièces où la FA pourrait être appliquée efficacement en tirant parti des capacités de la DfAM. Quatre critères sont souvent pris en compte dans ce processus : l’intégration des fonctions, la personnalisation, la légèreté de la conception et l’efficacité opérationnelle.
Le point de vue de l’utilisateur par rapport au point de vue de la fabrication
En tant qu’adopteur précoce des technologies de FA dans l’industrie spatiale, Virgin Orbit occupe également une position unique pour soulever certaines des questions qui doivent encore être discutées par les fournisseurs de FA et les prestataires de services de FA.
Selon notre invité, l’une de ces préoccupations est le fait que, même si la FA est un processus très fortement automatisé, il existe encore des fonctions telles que le retrait de la poudre/le nettoyage des pièces qui ne sont pas automatisées. Toute entreprise spatiale qui cherche à augmenter son rythme de production et de lancement cherchera des moyens de contrôler et d’automatiser cette étape de fabrication.
Au fil du temps, le secteur spatial est appelé à prendre une place encore plus importante dans l’industrie de la fabrication additive. L’utilisation très stratégique de la FA par Virgin Orbit pour fournir des services de lancement de petits satellites illustre bien la manière dont une entreprise spatiale peut tirer parti de ces technologies. Si le développement de chambres de combustion et d’injecteurs par FA est tout à fait unique, la présente histoire met en lumière certaines des complexités qui doivent encore être abordées au niveau de la fabrication ; des complexités qui nécessiteront certainement de nouvelles collaborations entre les fournisseurs de technologies de FA et les entreprises spatiales pour permettre de nouveaux lancements commerciaux.
**Au cœur du succès du lancement de Virgin Orbit se trouve une technique appelée « lancement aérien », qui offre une plus grande polyvalence pour les missions spatiales, puisque l’avion porteur peut être basé dans n’importe quel aéroport disposant d’une piste suffisamment longue pour le décollage. Une technique, en bref, qui améliore la capacité de charge utile de la fusée et fait du système LauncherOne l’un des services de lancement les plus souples et les plus réactifs du marché.
Ce dossier a été premièrement publié dans le numéro de Janvier/Février de 3D ADEPT Mag.