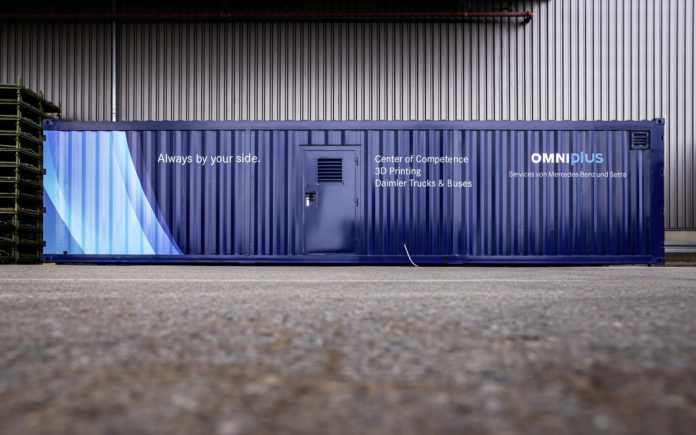
« Mobile Smart Factory« , « Portable 3D Printing Factory« , et maintenant « mini-usine » ou « centre d’impression mobile »… Les noms varient d’une organisation à l’autre mais le but ultime du concept reste le même : pouvoir réaliser de la fabrication additive in situ. Le concept arrive à un moment où la production décentralisée de pièces imprimées en 3D est devenue centrale pour soutenir certaines équipes éloignées des installations de fabrication classiques.
Derrière les deux premiers concepts cités se cachent des fournisseurs de technologies de fabrication additive, tandis que Daimler Buses et sa marque de services Omniplus sont au cœur du concept de « mini-usine ». Ce n’est un secret pour personne que Daimler Buses est un défenseur des technologies de FA, mais la question est de savoir pourquoi un fabricant de bus a besoin d’un centre d’impression mobile.
Bernd Mack, responsable du service clientèle et des pièces détachées chez Daimler Buses, apporte une première réponse : « Grâce au centre d’impression 3D mobile, nous pouvons exploiter davantage les avantages de l’impression 3D et augmenter encore la vitesse à laquelle nous fournissons des pièces de rechange. La production décentralisée de pièces selon les besoins évite les coûts de stockage et réduit les trajets de transport. Ainsi, l’impression 3D nous permet non seulement de réagir rapidement, de manière flexible et économique aux exigences des clients, mais aussi d’améliorer notre empreinte écologique pour la production de pièces de rechange. »
D’un point de vue pratique, le conteneur pilote de Neu-Ulm sera en service au centre de service BusWorld Home (BWH) à Hambourg. Le centre de service de Hambourg, qui offre déjà une gamme de services pour les autobus Mercedes-Benz et Setra, sera ainsi en mesure de produire rapidement des pièces de rechange en interne. Les trajets physiques de transport sont ainsi encore réduits et la pièce de rechange est chez le client encore plus rapidement. Grâce à l’expertise de BWH Hamburg dans le domaine de la peinture, les pièces de rechange peuvent être affinées directement, selon les besoins du client. Daimler Buses met ainsi en place une autre installation de production de pièces de rechange imprimées en 3D au BWH de Hambourg – en plus du centre industriel interne d’impression 3D pour la production de pièces à Neu-Ulm.
Q’implique la « mini-usine » ?
Disponible sous la forme d’un conteneur, la « mini-usine » intègre tous les processus de fabrication nécessaires à la production de pièces imprimées en 3D. Équipés d’une imprimante 3D industrielle qui occupe une surface de 36m2, les opérateurs pourront produire des pièces en polyamide de haute qualité, capables de répondre aux normes de production de Daimler AG en matière de moulage par injection et d’emboutissage.
Dans le conteneur de douze mètres sur trois, les opérateurs pouvaient préparer les données d’impression 3D sur un poste de travail CAO avant le processus d’impression. Le constructeur automobile explique que la poudre nécessaire est préparée dans une station de traitement où la pièce imprimée est également débarrassée des résidus de poudre dans une dernière étape. Un système de sablage et un compresseur d’air sont situés dans une pièce adjacente : le système de sablage lisse la surface des pièces pour une finition parfaite. Ici, les pièces imprimées peuvent également être peintes dans une gamme limitée de couleurs. Le compresseur alimente les systèmes en air comprimé. Le conteneur est également équipé d’un aspirateur industriel, d’un filtre à air et d’un système de climatisation.
De l’entreposage physique à l’entreposage numérique
Grâce à l’impression 3D, Daimler Buses peut réagir rapidement et avec souplesse aux demandes urgentes des clients, par exemple lorsque ceux-ci commandent des pièces rarement requises ou ont des demandes spéciales. Au lieu d’une attente de plusieurs semaines comme pour les pièces de rechange classiques, la production et la livraison d’une pièce imprimée en 3D ne prennent que quelques jours. Aujourd’hui, un peu moins de 40 000 pièces de rechange de bus sont déjà imprimées en 3D.
Ralf Anderhofstadt, responsable du « Center of Competence 3D-Printing » chez Daimler Buses, et son équipe se concentrent actuellement sur environ 7 000 pièces qui sont successivement numérisées. Certaines d’entre elles ne sont déjà disponibles que sous forme de pièces de rechange imprimées en 3D, après avoir été soumises aux étapes de numérisation, aux processus d’approbation et à de nombreux tests de produits, et sont stockées dans l' »entrepôt numérique » avec les informations d’impression nécessaires. Dans une prochaine étape, Daimler Buses a l’intention d’étendre et de décentraliser davantage le modèle commercial : les clients pourront alors acheter des licences d’impression 3D dans la section « commerce » du portail Omniplus On et faire produire les pièces correspondantes dans un centre d’impression 3D certifié par Daimler Buses.
Les centres d’impression de ce type étant encore peu répandus, ces mini-usines mobiles représentent une extension du modèle commercial prévu. Actuellement, une mini-usine mobile peut être transportée par camion jusqu’à n’importe quel endroit. Une fois sur place, seules l’électricité et une connexion internet sont nécessaires à son fonctionnement.
N’oubliez pas que vous pouvez poster gratuitement les offres d’emploi de l’industrie de la FA sur 3D ADEPT Media ou rechercher un emploi via notre tableau d’offres d’emploi. N’hésitez pas à nous suivre sur nos réseaux sociaux et à vous inscrire à notre newsletter hebdomadaire : Facebook, Twitter, LinkedIn & Instagram ! Si vous avez une innovation à partager pour le prochain numéro de notre magazine numérique ou si vous avez un article à faire connaître, n’hésitez pas à nous envoyer un email