Selon Additive Manufacturing Research (AMR), le marché de la fabrication additive électronique pourrait atteindre 7,9 milliards de dollars d’ici 2033. Cependant, l’industrialisation de la FA reste freinée par des défis techniques et économiques.
La simulation multiphysique, capable de modéliser et d’optimiser les interactions complexes entre phénomènes mécaniques, thermiques et électromagnétiques, s’impose comme un levier stratégique pour surmonter ces obstacles. En combinant FA et simulation multiphysique, l’industrie électronique peut atteindre une performance fiable et rentable à grande échelle.
La simulation multiphysique : un moteur pour optimiser les processus de fabrication électronique
La simulation multiphysique intègre des analyses mécaniques, thermiques et électromagnétiques permettant d’optimiser chaque étape de la conception et de la fabrication des composants :
- Les simulations mécaniques garantissent l’intégrité structurelle des matériaux, qu’ils soient conducteurs, semi-conducteurs ou isolants, et assurent la robustesse des dispositifs miniaturisés. Les boîtiers 3D imprimés bénéficient de cette optimisation pour répondre aux exigences de légèreté, de durabilité et de précision.
- Les simulations thermiques identifient les points chauds et optimisent la dissipation thermique, évitant les déformations dues aux fluctuations de température et améliorant ainsi la fiabilité des composants. Elles prolongent la durée de vie des composants critiques, comme les capteurs médicaux ou les dispositifs de haute précision.
- Les simulations électromagnétiques optimisent la compatibilité électromagnétique (CEM) et les performances haute fréquence, évitant les interférences indésirables. Ce point est crucial dans le développement d’antennes et de dispositifs actifs, garantissant des performances élevées tout en intégrant une architecture miniaturisée.

Une gestion des matériaux orientée vers l’économie et la durabilité
L’un des principaux défis pour les ingénieurs réside dans le choix des encres conductrices et des polymères, qui doivent allier conductivité, stabilité thermique et compatibilité avec divers substrats. Grâce aux simulations thermiques, il est possible de tester et de sélectionner des formulations performantes avant même la production, permettant des économies substantielles en matière de tests physiques et de délais de développement.
L’optimisation des paramètres d’impression, comme la vitesse de dépôt et la température, maximise la qualité de l’impression tout en maîtrisant la consommation de matériaux, ce qui s’avère précieux dans un contexte de rareté et de coûts élevés des ressources. La simulation permet ainsi de réaliser des économies tout en contribuant à la durabilité des procédés industriels.
Précision et fiabilité des procédés améliorées
La fabrication additive électronique présente encore des limitations en matière de précision, notamment pour les circuits imprimés multicouches et les composants miniaturisés. La simulation multiphysique s’avère indispensable pour anticiper et corriger les déformations mécaniques et thermiques induites lors de l’impression, garantissant ainsi une meilleure reproductibilité des composants. En modélisant les contraintes induites par le refroidissement des encres, les ingénieurs peuvent compenser les variations dimensionnelles en amont, réduisant ainsi les taux de rebut et augmentant la qualité des pièces fabriquées. Cette précision accrue est essentielle pour répondre aux standards élevés de l’aéronautique, du médical et de l’électronique grand public.
Réduction des coûts et délais de développement
La simulation multiphysique facilite le prototypage virtuel, remplaçant une partie des itérations physiques par des simulations numériques. En limitant le besoin de prototypes, cette démarche diminue les coûts et raccourcit les délais de développement, permettant aux entreprises de réagir plus rapidement aux évolutions du marché et de lancer des produits innovants dans des délais compétitifs. La capacité à adapter rapidement la conception améliore l’agilité et la flexibilité, en particulier face à des demandes de production en séries courtes. Les équipes R&D peuvent valider virtuellement les performances et ajuster leurs conceptions en amont, optimisant ainsi le temps entre la conception et la mise sur le marché.
Exemple concret : la société 3D Printing Corporation, spécialisée dans l’impression de composants électroniques en 3D, est parvenue à réduire ses coûts de production de 20 % et ses taux de rebut de 15 % en utilisant la simulation pour optimiser ses combinaisons de matériaux et ses procédés d’impression. Ces gains d’efficacité, alliés à la réduction des déchets, constituent un atout majeur pour une industrie en quête de sobriété et de durabilité.
Vers de nouveaux cas d’usage et une intégration industrielle optimisée
Au-delà de l’optimisation des procédés actuels, la simulation multiphysique favorise l’exploration de nouvelles applications électroniques en testant la viabilité de conceptions innovantes dans des environnements soumis à des contraintes extrêmes. La FA ouvre notamment des perspectives pour des secteurs exigeants comme les télécommunications, avec le développement d’antennes pour la 5G et la 6G. D’après un rapport de l’AMR, les antennes millimétriques imprimées en 3D, produites en quelques heures pour moins de dix dollars, affichent des performances comparables aux modèles conventionnels, mais à un coût drastiquement réduit. La possibilité de produire ce type de dispositifs à faible coût, tout en conservant une efficacité élevée, pourrait notamment révolutionner la couverture des zones rurales mal desservies.
Outre les télécommunications, l’impression 3D électronique bénéficie aux dispositifs médicaux, capteurs intelligents et à l’électronique grand public, répondant aux besoins croissants en personnalisation et miniaturisation. En intégrant la simulation multiphysique aux logiciels de CAO, les ingénieurs validant les spécificités de la FA dès la conception facilitent son adoption dans des chaînes de production établies et sécurisent les retours sur investissement pour les industriels.
Cet article a été écrit par Sebastian Stahn, Lead AE, Product Manager – Structural Optimization at Ansys.
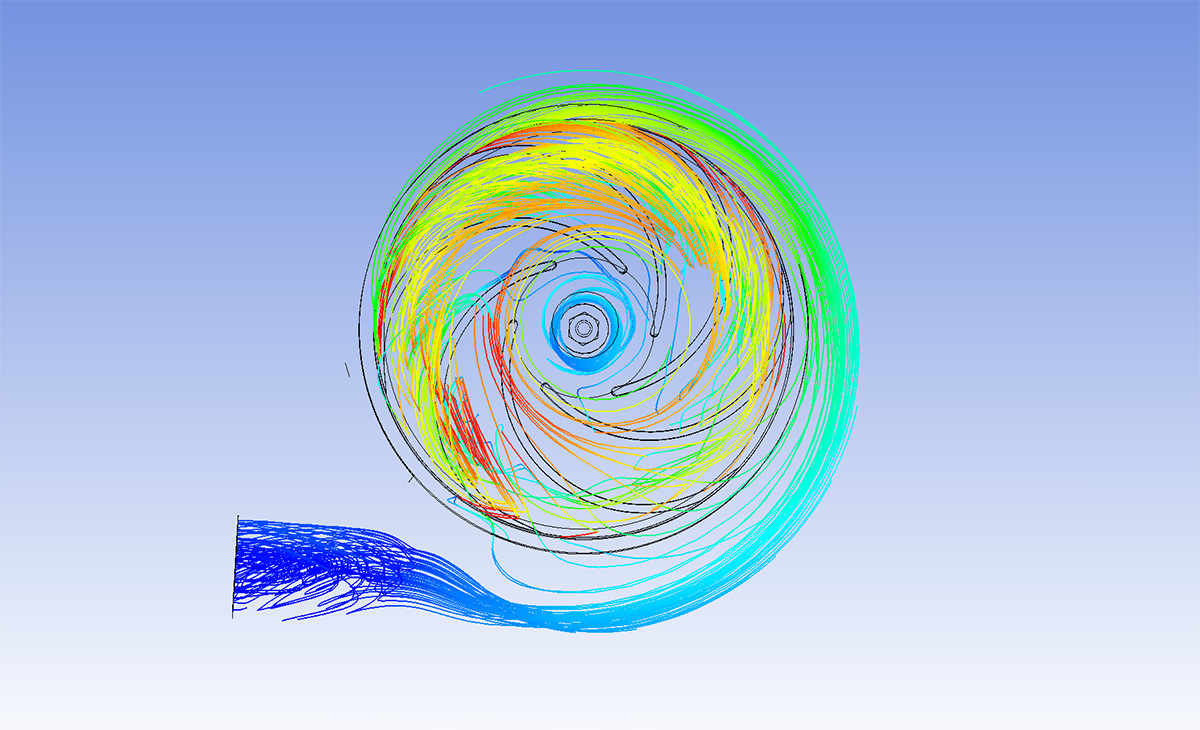