Prima Additive shares an overview of the Circular Economy Approach in Additive Manufacturing.
Prima Industrie Group specializes in the development, fabrication and commercialization of laser systems for industrial applications, sheet metal processing machinery, laser sources and additive manufacturing solutions.
To date, with over 40 years of experience in the industry, the Group has managed the installation of more than 13 000 machines in 80 countries across the world. Next to its divisions Prima Power and Prima Electro, Prima Industrie S.p.A has recently launched Prima Additive, a division that takes advantage of its longstanding experience in metal and lasers to provide industrials with additive manufacturing solutions.
For Paolo Calefati, Vice President additive manufacturing business development at Prima Industrie S.p.A., their market entry in the AM industry seems to be a logical step for the company, given the fact that AM is currently evolving in the same field where they have built trust and expertise: laser technology and sources, laser machines for cutting and welding, CNC’s and dedicated industrial electronics.
“Today, our vision of Additive Manufacturing is very similar: a highly promising technology rapidly passing from experimental use to industrial application up to its evolution into high productivity tools”, said the Vice President.
With a key focus on Powder Bed Fusion and Laser Metal Deposition technologies, Prima Additive has launched its own AM system Print Sharp 250. Surprisingly, the company seems to lay emphasis on a circular economy-based approach.
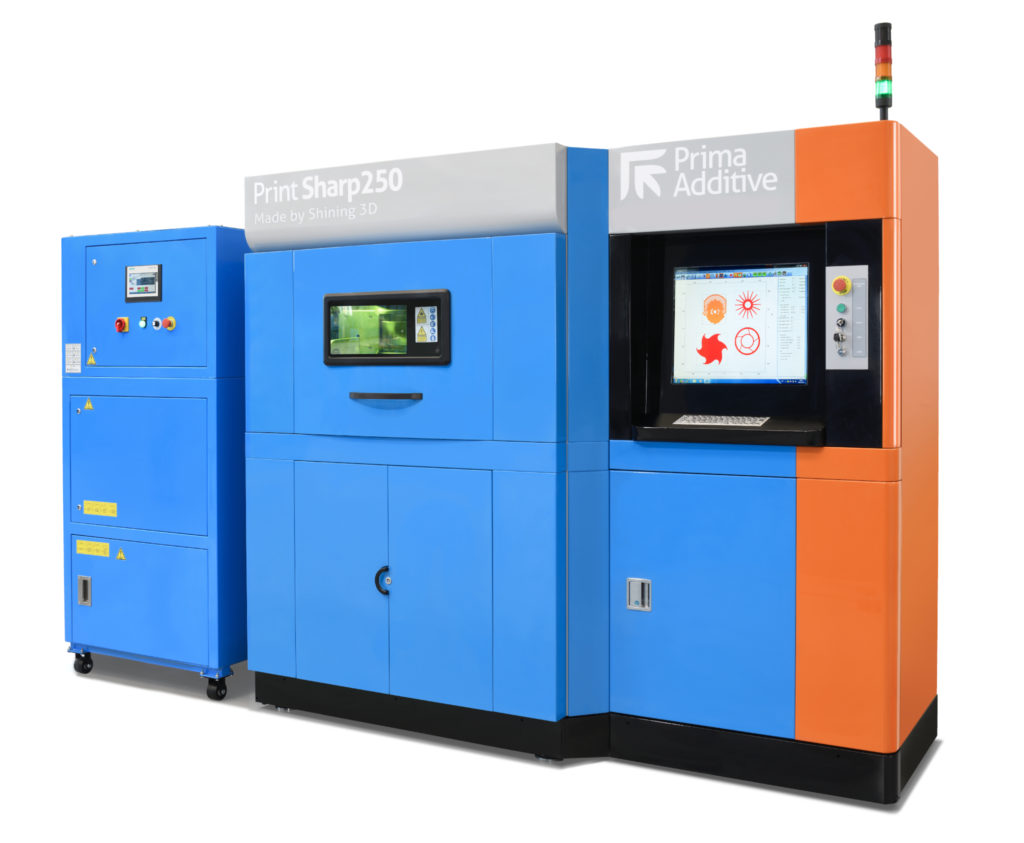
Paolo Calefati tells us the reason why a circular economy-based approach matters to the company. #OpinionoftheWeek
The circular economy concept
Generally speaking, in theory, the circular economy is a model of production and consumption, which involves sharing, leasing, reusing, repairing, refurbishing and recycling existing materials and products as long as possible. This way, the life cycle of products is extended.
In practice, this model implies reducing waste to a minimum. When a product reaches the end of its life, its materials are kept within the economy wherever possible. These can be productively used again and again, thereby creating further value.
In the manufacturing industry, producers have raised a major concern about sustainability. Indeed, this industry is a big consumer of energy and raw materials, which results in an increasing production of gas emissions and waste. Luckily, applying the concept of circular economy into AM aims to avoid further waste, especially at the materials stage.
As far as Prima Additive is concerned, Paolo Calefati explains: “In a circular economy, the value of products and materials is maintained as long as possible. The resources used and the waste are reduced to a minimum, and when a product reaches the end of its life cycle, it is modified to be used again, creating new value. This can bring great economic benefits.
Practical cases are the repairing of high added-value components with our direct energy deposition products, as it is done with our Direct Energy Deposition machine installed at ENEL.
Another example is the possibility to add features to already existing parts or recoating used parts to restore functionality.”
The Circular Economy Concept in AM has been discussed during a conference of EPMA: “the goal of the study was to apply the concept of circular economy into AM, by recovering process side-streams back to the feedstock material for Selective Laser Melting. The objective was to prepare powder from 100 % scrap feedstock following two routes: 1) mechanical milling of agglomerated residue powder, and 2) gas atomization of solid scrap without extra alloying to compensate possible alloy losses. The powder properties were analysed and test specimens for the determination of mechanical properties were made from the prepared powders and commercial reference powder. Conducted test series show that with recycled powders properties fully comparable to reference can be achieved.”
What makes then the Print Sharp 250
outstanding?
We already know the metal 3D printing system integrates a Direct Energy Deposition technology. Prima Additive Vice President also lays emphasis on the price-quality ratio, a significant factor in today’s industry given the fact that metal AM remains an expensive technology for most industrials.
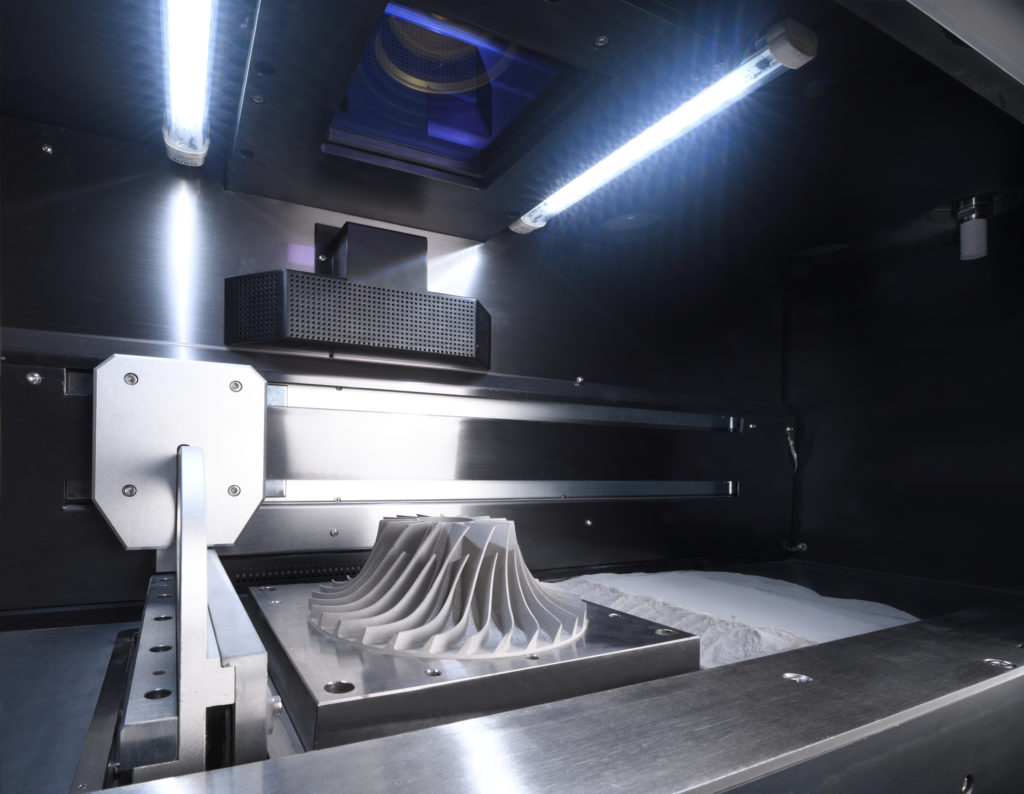
“[Our Print Sharp 250] is highly competitive, boasting the best price/performance ratio on the market. It is particularly designed for customers who wish to explore Additive Manufacturing starting with an inexpensive investment. Other [main advantages include its] surface quality and its user-friendliness, with simple use and maintenance procedures. But I would say that the biggest reason why [Prima Additive machines stand out from the crowd is because we focus on] our customers. We build a true partnership with our customers, offering an all-round support, from the design phase to prototyping, up to manufacturing optimization.
Further to the Powder Bed Fusion technology, covered by the Print Sharp product family, Prima Additive offers solutions for Laser Metal Deposition, covered with systems based on our well proven Laserdyne platform”, adds Paolo Calefati.

The next step for the company
In order to move closer to high productivity, Prima Additive is working on innovative models to complete their production portfolio. The company intends to build its next generation of products while keeping in mind the price-quality ratio. As per Paolo Calefati’s words, their goal is to “lower the barriers to entry for this new technology, which at the moment is mainly the prerogative of large companies, and allow smaller companies to explore the potential of these systems.”
In the meantime, Prima Additive’s experts can reply to any questions professionals might have during the next conferences and exhibitions (RM Forum in Arese (Italy) and Formnext (Frankfurt)) where they will showcase their products, online or on site at their application centre in Turin (Italy).
In a nutshell
With the help of Prima Additive, we tried to provide a quick overview of the circular economy concept in additive manufacturing. The topic is broad and can’t be discussed in-depth in a single Opinion of the Week.
Among all manufacturing techniques that can be exploited in the industry, early studies show that additive manufacturing holds substantial promise for sustainability and the creation of a circular economy (CE) but there is no guarantee yet that it will be effective for all AM technologies.
The truth is CE principles were embedded into the new manufacturing system before the adoption of AM reaches a critical inflection point in which negative practices become entrenched.
So, maybe the next strategy consists in analyzing a key point: while the current trajectory of AM adoption creates more circular material flows, what enablers and barriers do they really raise in the integration of CE by additive manufacturing?
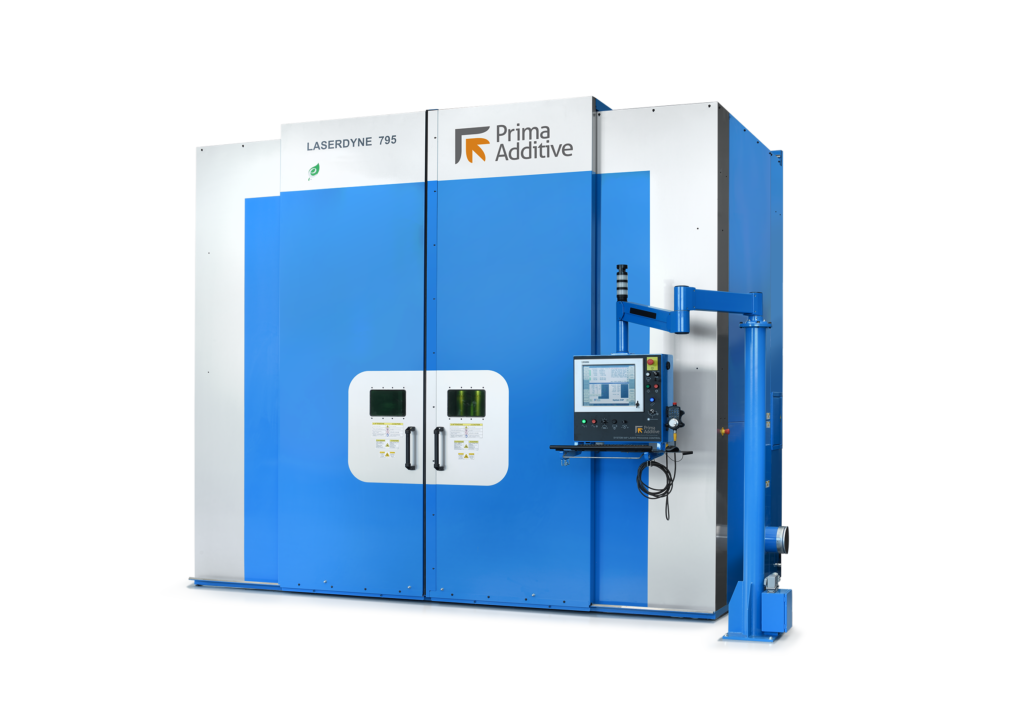
You can now post free of charge job opportunities in the AM Industry on 3D ADEPT Media.Would you like to be featured in the next issue of our digital magazine? Send us an email at contact@3dadept.com