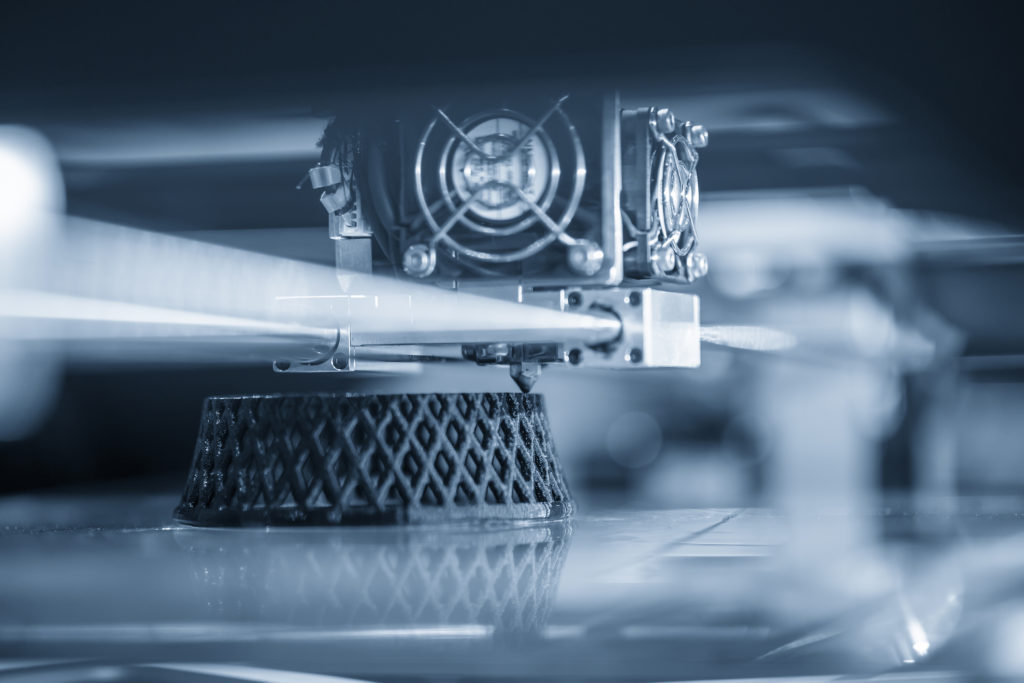
Binder jet 3D printing or binder jetting is one of the latest 3D printing technologies. Binder jet (BJ) printing is done with powders and liquid binder agents. These two are bound together to produce solid parts. From this perspective, you can safely say that BJ printing is a combination of material jetting and SLS.
The similarities with material jetting can be seen in the use of binder droplets to bound particles jetted out of the machine. On the other hand, the powder is similarly used in SLS. However, this is not everything there is to this type of 3D printing.
There are many differences in how it works, what kind of results it gives, and how it can be applied. Luckily for you, we are going to talk about these things and help you understand the potential behind this technology.
How binder jet 3D printing works
A typical binder jetting printer consists of a powder bin, powder re-coater, container for material, a build platform, and several print heads. Similarly to SSL 3D printing, the powder bin needs to be loaded with materials before the actual printing process starts.
However, the powder doesn’t need to be heated up. BJ printing doesn’t include any heat during the whole process. The first step is the deposition of the first powder layer throughout the platform. Print heads sweep the powder, and binder agent droplets get jetted.
The binder agent acts as glue for powder. When powder and droplets come in contact, their particles combine and become solid. When the whole first layer has fused, the platform switches to the second layer, and the entire process is repeated.
This happens several times until the part is finished. In the end, the whole region is covered with powder.
Materials used for BJ 3D printing

Another essential difference between SLS and BJ 3D print is that, with binder jetting, all of the powder used is good for recycling. This is very important for the environment and the manufacturing industry, especially now when everyone is becoming conscious about nature.
BJ parts can be made with metal or sand powders. There are many options available for both types of powders, and the choice is different from one application to another. BJ printing can be used for printing complex metal parts.
Sand binder jetting is an excellent technique as it can be used for making sand molds and full-color parts. It comes with low costs and can create great pieces with the utmost complexity. In general, metal binder jetting is more expensive than sand binder jetting.
General advantages of binder jet 3D printing
Comes with full-color abilities
To this point, only material jetting and multi-jet fusion had full-color capabilities. However, BJ printing also supports this option and does it precisely with the lowest costs possible. This is especially true for sand materials.
Parts don’t shrink or warp
FMD and BJ printers don’t use any heat during production. This means that there is no risk of parts getting warped during the process. This makes this printing technique an excellent option for manufacturing scalable parts.
Still, it’s important to mention that some shrinking can happen during sintering. Still, the chances are minimal, and the whole process is very efficient.
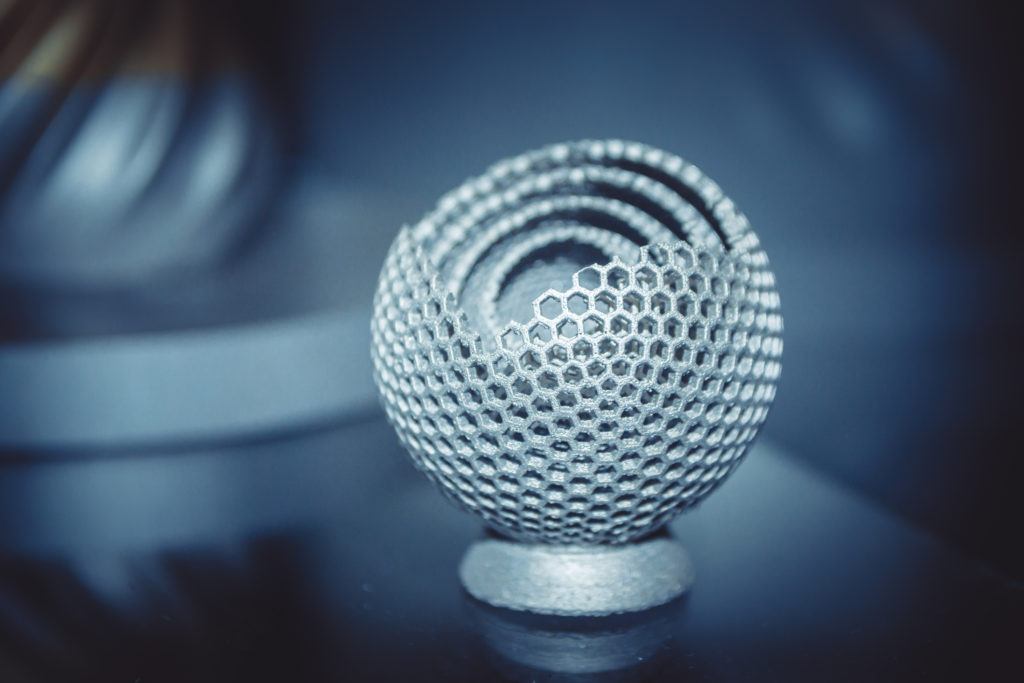
Reduced costs
Earlier, we mentioned that all of the extra powder during the production could be used in the future for more parts. Not only is this good for the environment, but this means you won’t waste money getting new powder.
This is the first 3D printing technology which completely preserves powder during operation. SLS 3D printers save around 50% of powder that can be used in the future. At the same time, binder jetting is overall more cost-effective compared to other additive methods and can print more substantial parts.
Faster operation
Binder jetting requires no support. Overall, this means that you will use less material on average for producing the same parts. It also means that you will have to waste less time on post-processing operations and that your pieces will be ready to go a lot faster.
The overall precision and high speed could make metal binder jetting the new standard production method for high volume manufacturing. However, even though the speed is there, many are concerned about whether it disrupts quality.
How speed affects density and surface quality
The popularity of jet 3D printing is growing fast, and one of the reasons is speed. But more research is needed to understand how the increase in speed affects density and surface quality. This is why a team of researchers decided to learn more about these issues.
First of all, it’s essential to understand how these printers can achieve higher speeds during operation. The overall printing time can be decreased by increasing printing modules within the printer. On the other hand, it’s also possible to increase the speed of the print head to achieve similar results.
Still, a faster-moving print head reduces dimensional accuracy. With higher powder speed, the printer showcased greater density. However, slower speeds gave better consistency when it comes to the surface evenness. Still, the surface roughness wasn’t terrible, and it came out in solid shape.
This means that binder jet 3D printing could be used for high-speed production while retaining density and overall quality. When it comes to the surface, it would just require a bit of post-processing to get everything in shape.
Conclusion
BJ printing has a bright future ahead. 3D modeling experts are already preparing new projects for this kind of printing technique, and we can see huge advancements. We are only scratching the surface with the potential this technology has to offer.
Images via dreamstime – This article has been written by John Victor.