Versatile & impact-resistant on the one hand, weather- & UV-resistant on the other hand, ABS and ASA, the two new BigRep certified, engineering-grade materials, are intended for the automotive and consumer products industries. Both materials can be leveraged on the manufacturer’s STUDIO G2 and PRO (ACE) 3D printers.
Since the launch of its latest 3D Printers, BigRep has been working on new materials, which would be cost-efficient and environmental-friendly. The Large-format 3D Printing specialist has optimized its ABS (Acrylonitrile Butadiene Styrene) for mobility applications and a wide range of consumer applications. Indeed, with high temperature- and warping-resistance, ABS enables the production of complex, ready-to-use parts such as end-use, factory tooling and functional prototypes with demanding geometries.
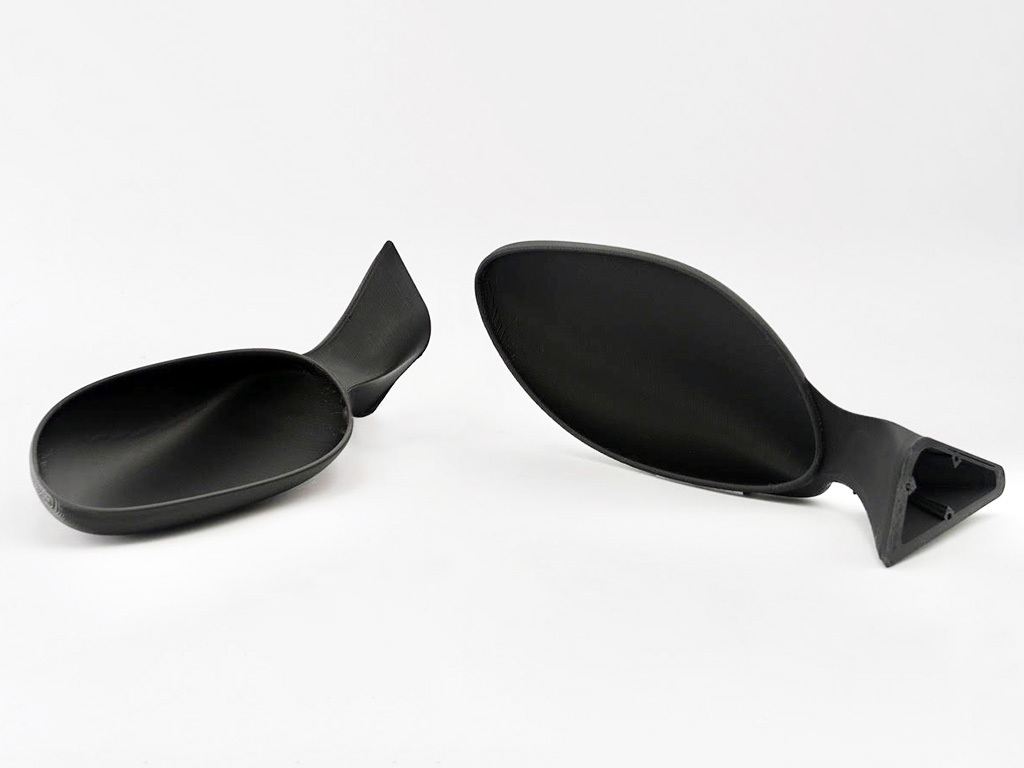
ASA (Acrylonitrile Styrene Acrylate) on the other hand offers high mechanical resistance, low shrinkage and superior layer adhesion. Its main difference with ABS is that it delivers a greater heat resistance. According to the manufacturer, it is also very easy to get the desired result at the end of the printing process with ASA as the material gives a natural aesthetics look to the part. Since the part rendering does not show age or fade in colour with prolonged UV exposure, ASA becomes the best candidate for industrial or automotive end-use parts.
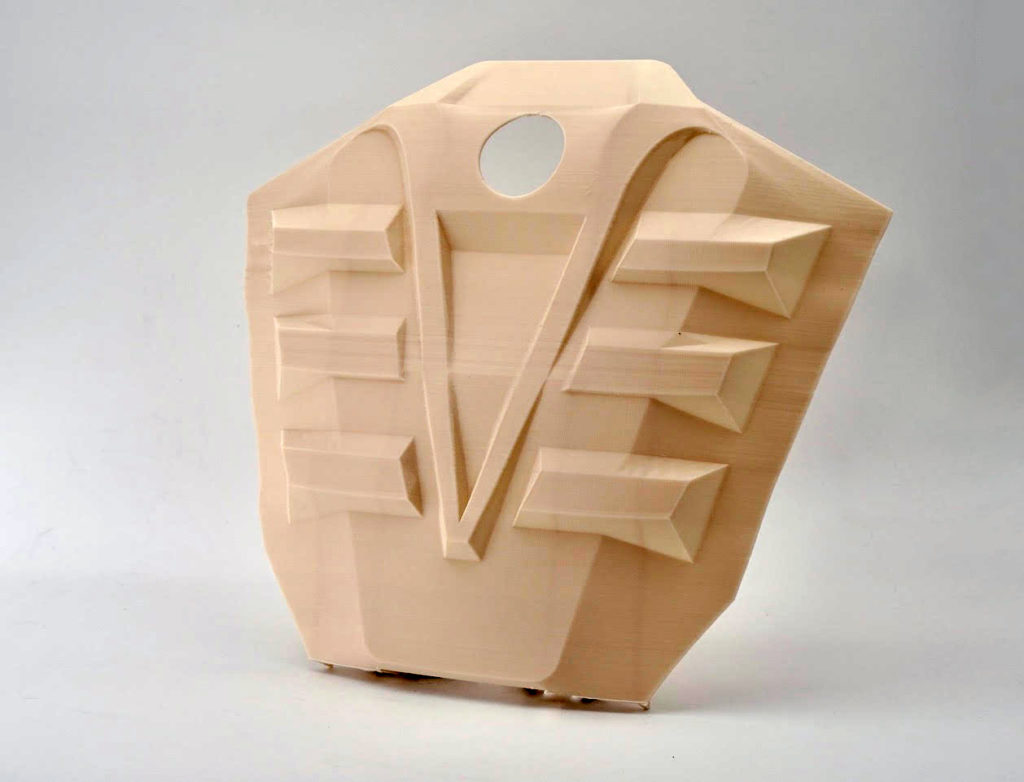
“With these two new engineering-grade materials, customers will now be able to use industry-standard ABS and ASA materials in large-format 3D printing, taking full advantage of our 3D printers’ speed, precision and quality,” said BigRep Managing Director, Martin Back. “Our customer- and applications-focused development of AM systems and materials, combined with our deep understanding of the entire industrial value chain, pill be pivotal in the continued evolution of our digital solutions empowering production.”
ABS/ASA present some real added value to AM – both can be chemically affixed to themselves or similar plastics, for example. ABS is a lightweight (1.08g/cm³) material also suitable for injection molding and extrusion, making it a key element in AM. Last but not least, both ABS/ASA are laid out for easy post-processing using standard machining techniques; they can be easily cut with standard shop tools and line-bent with standard heat strips.
Remember, you can post free of charge job opportunities in the AM Industry on 3D ADEPT Media or look for a job via our job board. Make sure to follow us on our social networks and subscribe to our weekly newsletter : Facebook, Twitter, LinkedIn & Instagram ! If you want to be featured in the next issue of our digital magazine or if you hear a story that needs to be heard, make sure to send it to contact@3dadept.com