Have automotive parts been a difficult space for AM to grow? : The Toyota case
When I started covering the AM industry, one of the first things I learned was that automotive remains on the list of top three verticals adopting the technology. The closer I look, the more I realize that automotive parts have been a difficult space for AM to grow. Is this difficulty linked to the challenges encountered in complex applications that industrials want to achieve? Or is it a business model matter? We assessed these questions with a key focus on Toyota’s story.
Why Toyota, you may ask?
Because “Toyota began exploring Additive Manufacturing around the early 2000s, initially for rapid prototyping. The expansion into production applications and broader use of AM technologies started gaining more momentum in the 2010s,” William (Dallas) Martin, Additive Manufacturing Engineer at the company, told 3D ADEPT Media. The company started its journey at a time when people did not believe that much in the technology, but, today, its use of AM is global. “The company has integrated AM into various facilities worldwide for purposes like prototyping, tooling, and even producing functional parts in some cases. Their global approach helps streamline production, reduce costs, and explore innovative designs across different markets and manufacturing plants,” Dallas Martin adds.
This ability to explore AM for so long and for different purposes may provide insights into the reasons why automotive parts have been a difficult space for AM to grow.
The technology perspective
First and foremost, Toyota’s use of AM across the world embodies the different angles that can shape the narrative of a company’s journey with AM. While in Asia – in Japan particularly, we highlighted the company’s use of metal AM, in Europe, we covered a lot of the company’s use of FDM technology.
William Dallas Martin who spearheaded the company’s AM initiatives at Toyota’s TILT Lab – where he helped establish the company’s first internal maker space – told 3D ADEPT Media the car manufacturer “owns over 200 3D printers globally, utilizing various technologies such as Fused Deposition Modelling (FDM), Stereolithography (SLA), Selective Laser Sintering (SLS), and Direct Metal Laser Sintering (DMLS).” “These printers are used for prototyping, tooling, and even producing functional parts, helping improve efficiency and innovation in their manufacturing processes,” he explains.
While Additive Manufacturing (AM) is gaining traction in the applications Dallas Martin mentioned, its use in complex automotive manufacturing faces significant challenges. Material properties and certification, process control and repeatability, as well as production speed and scalability, remain key hurdles—especially from a technological perspective. A complete analysis of the problem would include cost constraints, but that topic would require an entire chapter.
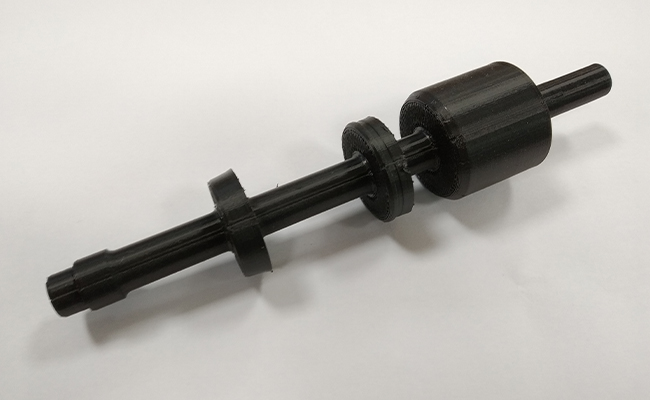
Let’s take material properties and material certification for instance. Many 3D printing materials lack the strength, fatigue resistance, and thermal stability needed for automotive applications, especially under extreme conditions (e.g., engine components, and structural parts).
Imagine a company that needs to produce 500 items of a specific part over a given period. It’s important that those items are fabricated on a specific 3D printer with a material that has been tested, certified, and standardized for this application. However, things can get complex if during that time, the material producer changes the recipe of that material – making the entire team start over the process.
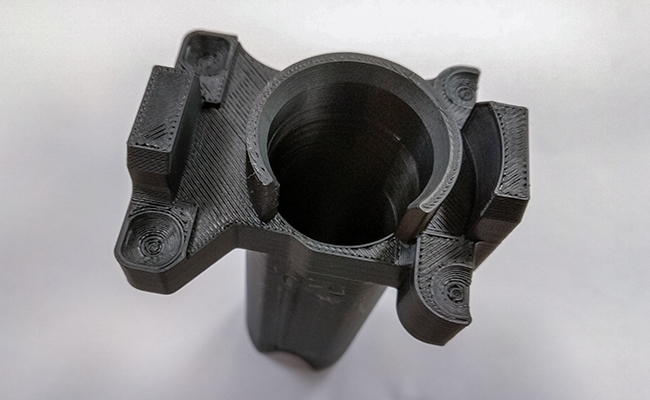
Is this difficulty therefore linked to the challenges encountered in complex applications that industrials want to achieve? For Dallas Martin, a complex part is not often the most challenging:
“The most complex part I’ve worked on is a production part that helped change people’s perspective on additive manufacturing. By eliminating the need for traditional tooling and cutting lead times, it showed how AM could reduce costs while adhering to industry standards. The most challenging part has been getting additive manufacturing through the PPAP or SQAM process. Ensuring compliance with all required standards and quality checks while implementing AM in production has been a significant hurdle, but it’s a crucial step to validate its use in manufacturing.”
Evolving business models?
As the table below illustrates, while Toyota does not rely on AM for full-scale vehicle production, it has been integrating 3D printing in various aspects of its manufacturing process.
Dates | Phases | Details |
Early 2000s | Prototyping phase | Testing designs |
2010s | Tooling & customization |
– Manufacture jigs, and fixtures – Explore lightweight structural parts |
2020s | Spare parts & future mobility |
– Use of 3D printing for on-demand spare parts, especially for older vehicle models and classic cars. – Use of AM for electric vehicles (EVs) and autonomous mobility solutions, such as lightweight chassis components. – In 2021, Toyota’s Lexus division used AM to produce lightweight, high-performance parts for concept vehicles. |
Legend: Key milestones in Toyota’s adoption of AM
In his 2018 CES speech, Akio Toyoda, President of Toyota Motors and grandson of the company’s founder, said his goal was to “transition Toyota from an automobile company to a mobility company” – emphasizing his determination “to create new ways to move and connect [their] customers across the country, across town, or just across the room.” Making this vision a reality would mean exploring transportation solutions that go beyond selling vehicles – solutions with a technology approach that emphasizes connectivity, EVs or even autonomous driving.
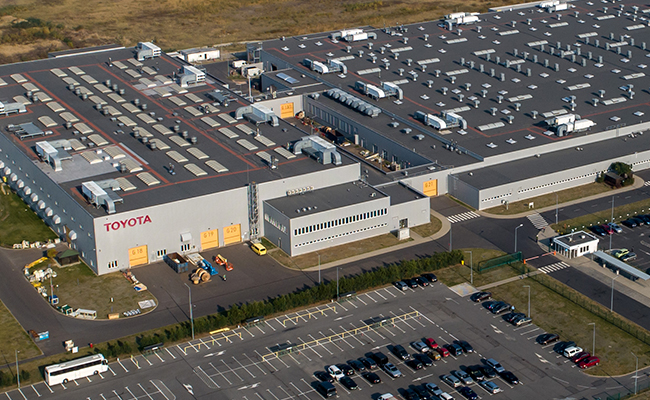
These ideas may drive an increasing use of AM. If we take the example of electric vehicles (EVs), Dallas Martin thinks the technology can help reduce the weight of some EV parts, create more efficient designs, and allow for faster prototyping.
“It’s especially valuable for producing complex, lightweight components that improve battery efficiency, cooling systems, and structural parts. Additionally, AM can enable customized parts and reduce supply chain complexities, which is crucial for EV production,” he notes.
While I agree with him, I can’t help but think that the use of AM remains very theoretical on this specific topic – we either don’t have enough conversations, or the ones with have are not the right ones.
One way to foster genuine knowledge-sharing on the topic would be to take part in industry events where AM technology providers and (potential) users could discuss with “no high-pressure sales”. One such event remains AMUG which is as per the words of Martin “ a collaborative environment with application engineers and users like [him].”
“It’s a collaborative environment where you can get hands-on knowledge, build lifelong connections, and make informed decisions without the pressure of sales pitches. It’s an experience you won’t regret!” he said.
In the meantime, to answer the aforementioned questions, Toyota’s use of Additive Manufacturing (AM) is influenced by both technical challenges and business model considerations. Technically, achieving the material properties and precision required for high-volume production parts remains a hurdle. Business-wise, the automotive industry’s reliance on economies of scale makes AM more suitable for prototyping and low-volume components.
This content has been written in collaboration with AMUG.