Authentise and nebumind have merged data capture and visualization capabilities to strengthen additive manufacturing users’ tools when it comes to part data.
Authentise specialises in data-driven workflow tools for additive manufacturing whereas nebumind provides visualization and analytics tools for manufacturing data.
The integration of nebumind’s tools into the Authentise Manufacturing Execution System (AMES) would enable engineers to review data at a single glance.
According to Franz Engel, co-CEO at Nebumind, engineers currently deal with long and complex tables of sensor data that are difficult to make head or tail of.
With this integration, they can get this data automatically and fuse it with the shape being produced. “That way the user can see an instant heatmap of potential problem areas, and deep dive into every voxel to understand the underlying data if necessary. This view can help customers identify rework needs up to 10 times faster and reduce production rejects by up to 90%. Integrating this view with AMES makes sense, since that’s where production is managed, and data is held”, Engel said.

nebumind produces ‘digital twin’ visualizations, which fuse machine parameters and sensor data with the original part geometry. The integration of these visualizations with AMES will help users identify problem zones of each part more easily and lead to less time intensive and more accurate inspections. In addition, real-time alerts generated by the nebumind system inside AMES will help the user address any deviations during the process, reducing waste. Since AMES already captures data from the machines and manages the printable geometry, the system passes this information on to nebumind automatically, saving the user from locating and uploading this information separately. The insight generated is appended to the existing AMES part report to ensure end-to-end traceability.
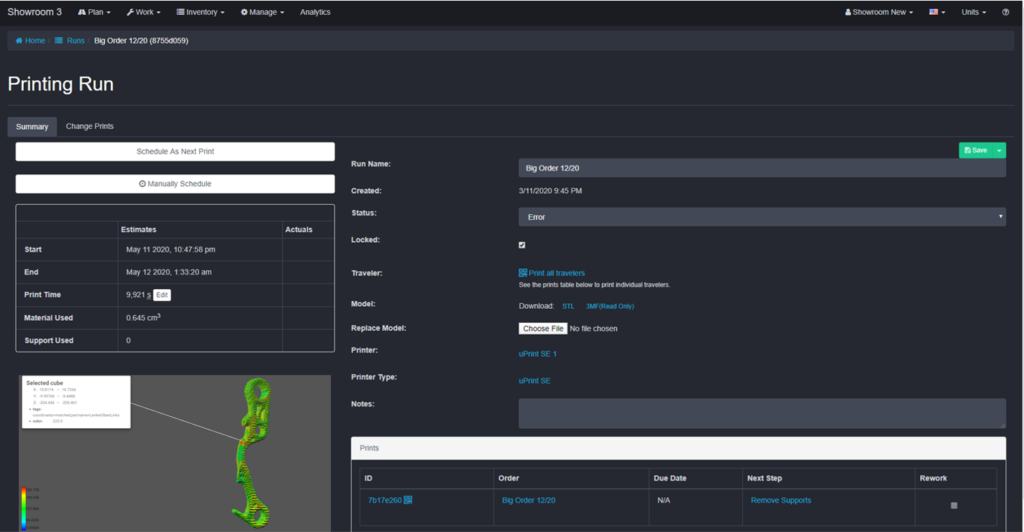
“We’re excited to be welcoming nebumind to the Authentise platform,” says Andre Wegner, CEO of Authentise. “Together we can accomplish the goal of a seamless, failproof additive process. The collaboration proves once again that trying to do so single-handedly leads to failure and harms customers. For years they have had to put up with sub-optimal data analysis, in several different software tools. Now it’s all in one place, instantly accessible, and cutting edge. This partnership proves once again how much we can move this industry forward if industry leaders work together, and not against one another.”
Remember, you can post AM job opportunities for free on 3D ADEPT Media or look for a job via our job board. Make sure to follow us on our social networks and subscribe to our weekly newsletter: Facebook, Twitter, LinkedIn & Instagram! If you want to be featured in the next issue of our digital magazine or if you hear a story that needs to be heard, make sure to send it to contact@3dadept.com