Parmi les diverses solutions d’impression 3D que les centres d’enseignement et de recherche explorent, très peu sont souvent consacrées aux filaments céramiques. Un travail récent effectué par le Centre des Matériaux a révélé des informations intéressantes sur l’utilisation des filaments Zetamix dans l’une de leurs expériences.
Cette gamme de filaments a été développée par Nanoe, un expert français de l’impression 3D en céramique. « Zetamix est la première gamme de filaments céramiques. Ils sont principalement composés de céramiques et d’un liant polymère en minorité. Une telle composition confère au filament une certaine flexibilité. Les filaments sont très faciles à utiliser et à intégrer, des caractéristiques qui permettent aux entreprises de se lancer plus facilement dans la FA céramique », déclare Guillaume de Calan, fondateur de Nanoe, dans une conversation avec 3D ADEPT Media.
Le Centre des Matériaux est une unité de MINES ParisTech – PSL et est également une Unité Mixte de Recherche du CNRS (UMR 7633 ) du CNRS, spécialisée en Science des Matériaux et Modélisation Mécanique avec une attention particulière aux nouveaux matériaux obtenus à partir de procédés tels que la FA. La plupart des recherches du centre visent à évaluer l’influence des procédés de fabrication sur les propriétés des matériaux tels que produits ou avec des conditions de vieillissement impliquant un environnement sévère. Malgré l’utilisation d’échantillons spécifiques pour les environnements à haute température, les porte-échantillons habituels ne permettent pas de réaliser ces expériences. C’est pourquoi, l’équipe de recherche a décidé d’explorer les filaments d’alumine Zetamix dans leurs expériences.
« Afin d’étudier les différences de propriétés entre un métal fabriqué par fonderie et un métal fabriqué par SLM (Selective Laser Melting), MINES ParisTech a dû s’équiper de porte-échantillons hautement personnalisés pour les tests de traction. En effet, la réalisation d’une pièce métallique par SLM est loin d’être aisée et nécessite un post-traitement au four : après l’impression, les éprouvettes de traction doivent être recuites », peut-on lire dans un rapport.
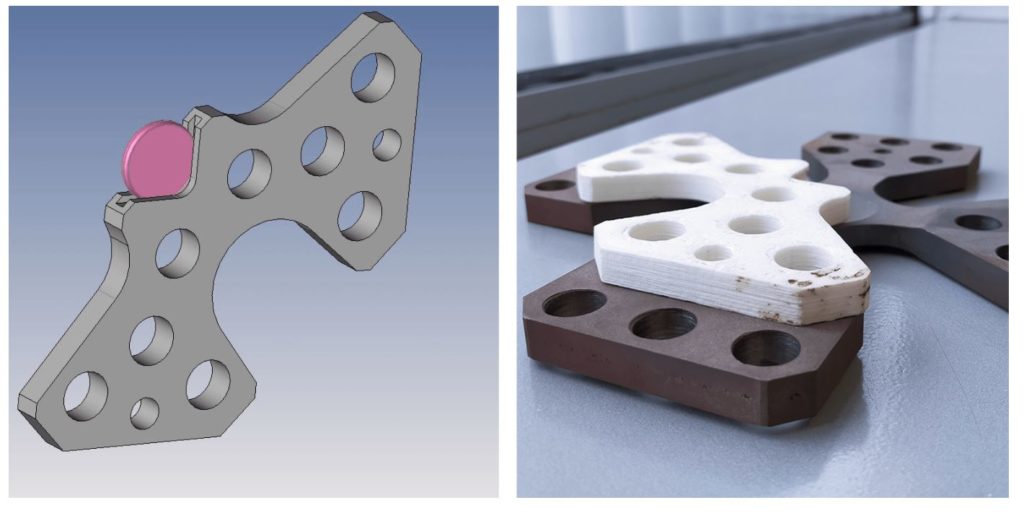
Or, l’un des experts en essais mécaniques à haute température, Sylvain Gailliegue, souhaitait recuire simultanément plusieurs échantillons SLM dans un four tubulaire afin de gagner du temps et de s’assurer que toutes les pièces étaient chauffées dans les mêmes conditions. Cette idée soulève un certain nombre de problèmes, comme le fait que les échantillons ne doivent pas se toucher dans le four tubulaire, ou qu’ils doivent rester au centre du four tubulaire où la température est homogène, d’où la nécessité d’un porte-échantillon personnalisé. Cet échantillon doit résister à une température élevée et doit être non-conducteur pour le système inductif.
« En effet, pour résister au traitement thermique, ils doivent être dans une céramique réfractaire et stable comme l’alumine. Grâce à Zetamix, Sylvain a réussi à produire un porte-échantillon en alumine parfaitement adapté qui a résolu tous les problèmes mentionnés précédemment », explique le rapport.
Le porte-échantillon personnalisé a été produit dans un matériau qui remplit ces deux contraintes : L’alumine.
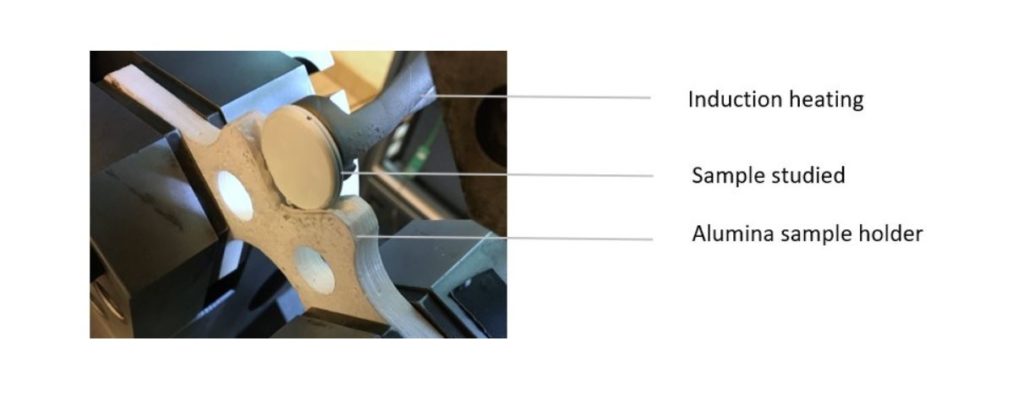
« Une fois de plus, l’alumine est un matériau coûteux lorsqu’il est produit en petite quantité, et Sylvain ne peut se permettre de sous-traiter la production de ce porte-échantillon. De la même manière que pour le porte-échantillon précédent, Sylvain a imprimé une pièce en alumine parfaitement adaptée à la machine grâce à Zetamix », conclut le rapport.
N’oubliez pas que vous pouvez poster gratuitement les offres d’emploi de l’industrie de la FA sur 3D ADEPT Media ou rechercher un emploi via notre tableau d’offres d’emploi. N’hésitez pas à nous suivre sur nos réseaux sociaux et à vous inscrire à notre newsletter hebdomadaire : Facebook, Twitter, LinkedIn & Instagram !