À l’exception des systèmes de propulsion électrique utilisés pour les satellites de communication commerciaux, la plupart des moteurs-fusées en service aujourd’hui sont des fusées chimiques. Cela signifie qu’ils reposent sur des réactions de combustion entre un carburant et un oxydant pour produire des gaz d’échappement à grande vitesse. Or, ce type de système de propulsion présente plusieurs défis qu’il convient de relever en priorité afin d’offrir une valeur élevée au marché de la propulsion spatiale. Dans sa liste de priorités, Agile Space Industries aborde les défis pour lesquels la fabrication additive joue un rôle essentiel.
Pour moi, l’exploration de l’espace se résume à la distance que nous pouvons parcourir, à la rapidité et au coût de notre voyage, et à ce que nous pouvons emporter avec nous. Les systèmes de propulsion spatiale étant au cœur de la nouvelle économie de l’espace, Agile Space Industries est l’une des rares entreprises à miser en permanence sur la fabrication additive.
Même si la société a été fondée en 2009, Agile Space Industries est apparue sur notre radar pour la première fois en 2021 lorsqu’elle a acquis le bureau de services d’impression 3D Tronix3D, un fournisseur de longue date basé à Pittsburgh, en Pennsylvanie, aux États-Unis. Ceux qui suivent l’entreprise depuis le tout début ont probablement été témoins de son changement de nom, d’AMPT – son premier nom – à Agile Space Industries.
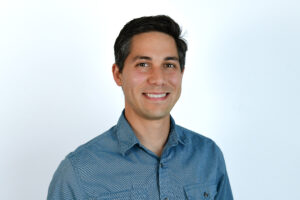
« AMPT a obtenu l’un des premiers SBIR pour la fabrication additive d’injecteurs de fusée en 2009, mais à l’époque, la technologie de fabrication additive n’était tout simplement pas au même stade de maturité qu’aujourd’hui. Avec l’évolution du domaine de la fabrication additive métal et l’émergence d’une nouvelle génération d’alunisseurs nécessitant des solutions de propulsion innovantes, le moment était idéal pour commencer à concevoir nos propres modèles. En 2019, AMPT est devenu Agile Space Industries, et nous avons commencé à développer nos propres propulseurs qui sont conçus uniquement pour la fabrication additive », ont déclaré Ben Graybill, responsable des opérations de fabrication additive, et Dustin Crouse, ingénieur de FA en chef du processus et du développement chez Agile Space Industries, à 3D ADEPT Media.
Avec l’acquisition de Tronix3D, ce qui avait commencé comme une opération visant à optimiser les performances des systèmes de propulsion utilisés pour les missions lunaires de la NASA et de SpaceX est devenu une autre activité principale de l’entreprise.
« Même si nous sommes notre principal client en matière de fabrication additive et que nous sommes pleinement satisfaits des résultats, nous nous engageons également dans plusieurs projets additifs externes, en maintenant généralement 3 à 4 programmes pluriannuels à un moment donné.
Notre champ d’action est très varié, allant des systèmes de propulsion dans l’espace aux applications navales en passant par les systèmes d’extraction du pétrole. L’un des aspects essentiels de nos services consiste à tirer parti de l’expertise de nos ingénieurs en matière de conception pour la fabrication additive (DFAM). Le projet implique des défis complexes en matière de conception de produits et l’utilisation d’alliages spécialisés et exotiques.
En outre, lorsque cela correspond à nos objectifs stratégiques, notre équipe de développement des processus se charge d’intégrer de nouveaux alliages dans notre flux de travail. Cela nécessite de définir et de mettre en œuvre de nouveaux processus de production à partir de zéro, qui sont adaptés à chaque étape pour répondre aux exigences uniques du matériau et de l’application. Cette approche nous permet d’étendre continuellement nos capacités et d’offrir des solutions de pointe à diverses industries », expliquent Graybill et Crouse.
À ce jour, Agile Space est connue pour la fabrication de propulseurs et de moteurs de fusées, fournissant un ensemble de services allant de la conception, aux services de FA, à la fabrication soustractive et aux capacités d’essai.
Les défis des systèmes de propulsion spatiale
Ceux qui n’ont pas de formation d’ingénieur peuvent se rappeler que la propulsion spatiale est une branche de l’ingénierie aérospatiale qui met en lumière les méthodes et les technologies permettant de propulser les engins spatiaux et les satellites dans l’espace extra-atmosphérique.
Le problème est que les méthodes utilisées pour propulser les engins spatiaux et les satellites sont complexes et parfois difficiles à combiner avec les nouvelles technologies de fabrication. Elles comprennent la propulsion spatiale par gaz froid, la propulsion nucléaire, la propulsion spatiale électrique et la propulsion spatiale chimique – la méthode la plus utilisée et la spécialité d’Agile Space Industries. Comme indiqué ci-dessus, cette technique de propulsion repose sur des réactions de combustion entre un combustible et un oxydant pour produire des gaz d’échappement à grande vitesse.
Avec l’intégration des technologies de fabrication dans le processus de développement, les entreprises spatiales doivent faire face à des obstacles majeurs qui sont à la fois économiques (économies d’échelle) et technologiques (science des matériaux et miniaturisation).
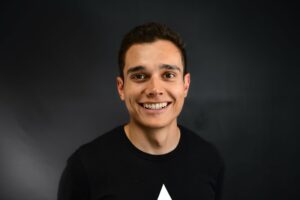
« Les cinq principaux défis pour la propulsion spatiale sont la gestion thermique, les capacités d’essais au sol, les performances sur des durées supérieures à un an, les taux de vol, et enfin la science des matériaux (qui joue un rôle dans la gestion thermique) », ont déclaré Graybill et Crouse.
En outre, au-delà du développement, ce qui compte vraiment, c’est la taille de votre système et la cadence de production. Selon Graybill et Crouse, « la FA n’est pas favorable à la production de BEAUCOUP de moteurs par an, mais pour les composants de niche, elle convient parfaitement (géométrie complexe des canaux de refroidissement, etc.), même à des volumes plus élevés. Elle peut être très utile pour la miniaturisation, en particulier si ce qui doit être miniaturisé se trouve dans un endroit difficile à fabriquer. »
Fabrication Additive (FA): applications et défis clés
Avant de nous pencher sur la valeur ajoutée spécifique que la FA apporte à Agile, il est important de considérer les investissements qu’Agile a réalisés jusqu’à présent pour mener à bien ses opérations de FA. Le centre de fabrication avancée basé à Mount Pleasant, qui est certifié ISO9001 et AS9100, enregistré auprès de l’ITAR et conforme à la norme NIST-SP-800-171, prend en charge les opérations de FA qui vont du développement du processus initial à la production en série de matériel de vol qualifié. Pour ce faire, elle s’appuie sur une large gamme d’équipements spécialisés qui comprennent des solutions de métallographie et d’inspection, telles que la Keyence VHX7100 qui répond aux besoins de développement et de caractérisation des processus.
En ce qui concerne les imprimantes 3D, on trouve les imprimantes 3D FDM et SLA de base dans leur environnement de production, ainsi qu’une gamme d’imprimantes 3D industrielles de TRUMPF. Dans la liste des matériaux qualifiés que ces imprimantes 3D peuvent traiter, l’équipe d’Agile se concentre sur neuf alliages manufacturables uniques, dont l’alliage réfractaire sensible à l’oxygène Nb C103.
« Nous rencontrons parfois des situations dans lesquelles les composants ou les systèmes disponibles sur le marché ne répondent pas à nos exigences spécifiques. Dans de tels cas, notre équipe a conçu et fabriqué de manière innovante des systèmes propriétaires de mélange de lots et de rinçage de dépotage, améliorant ainsi le rendement de nos pièces et notre efficacité globale », soulignent Graybill et Crouse.
Si l’on s’en tient aux activités d’Agile en tant que fournisseur de solutions de propulsion spatiale, la FA peut être utilisée pour le développement de tout nouveau produit :
« Son principal avantage réside dans sa capacité d’exécution rapide, qui nous permet d’itérer les conceptions en quelques semaines. Cette souplesse nous permet d’amener un nouveau produit au banc d’essai en un mois seulement. En fait, nombre de nos produits sont composés de plus de 85 % de composants additifs en poids, ce qui démontre l’utilisation extensive de l’AM dans notre processus de production ».
Il est intéressant de noter qu’Agile va au-delà des avantages largement connus de la FA pour souligner sa force lorsqu’il s’agit de fabriquer des pièces spécifiques. Pour nos experts, cette force réside dans la capacité à produire des collecteurs internes complexes à différentes échelles au sein d’une même machine :
« Cette capacité est particulièrement cruciale pour les composants tels que les injecteurs et les chambres, qui nécessitent souvent des structures internes complexes. Par exemple, certains de nos injecteurs comportent plus de 50 collecteurs courbes internes, chacun se terminant par des orifices d’un diamètre inférieur à 0,5 mm. Ce besoin de haute précision contraste avec les exigences à plus grande échelle d’éléments tels que les chemises de refroidissement régénératif de notre moteur A2200, qui mesurent plus de 5 mm de large », précise Graybill.
Et Crouse poursuit : « Pour garantir la cohérence et atténuer tout risque de variation dimensionnelle ou de processus, nous utilisons les mêmes imprimantes pour le développement et la production. Avant de passer du développement à la production, une imprimante est soumise à une série de contrôles rigoureux afin d’être qualifiée pour la production. Ce passage en douceur du prototypage à la production souligne notre engagement à maintenir des normes élevées de qualité et de fiabilité dans nos processus de FA, ce qui en fait une pierre angulaire de nos opérations de fourniture de solutions innovantes de propulsion spatiale. »
En outre, pour donner un exemple tangible du rôle essentiel de la FA et de sa capacité à accélérer la vitesse de production, les experts partagent l’histoire d’une nouvelle chambre qui se trouvait dans la file d’attente d’usinage et qui devait faire l’objet d’un essai de tir à chaud dans la semaine qui suivait. Le problème est qu’en raison du profil de surface unique et des collecteurs externes, aucune de leurs fraiseuses ou tours ne pouvait accueillir le composant pour une opération de coupe nécessaire. En l’espace de 48 heures, ils ont conçu une coquille en trois parties à partir de zéro, l’ont imprimée en 3D en Ti64 et ont fabriqué des copeaux sur le tour.
Malgré ses nombreux avantages, nous devons être conscients des limites potentielles de la technologie. Même si ces limites sont différentes d’un utilisateur de FA à un autre, certains défis sont communs à tous ceux qui cherchent à industrialiser la FA. Il s’agit notamment de l’intégration et de la gestion des données.
Pour rappel, la gestion des données est cruciale pour établir la traçabilité des pièces, comprendre les processus de FA et prendre des décisions au cours du cycle de développement du produit. Dans cette optique, la conservation, l’intégration, la fusion, le partage et l’analyse des données deviennent complexes lorsqu’il faut faire face au volume, à la vitesse, à la variété et à la véracité de ces données.
Lorsqu’on leur a demandé comment ils relevaient ce défi, les experts d’Agile ont répondu qu’ils s’appuyaient sur une combinaison de stratégies internes et d’applications tierces :
« Ces outils sont conçus pour traiter la quantité importante de données collectées in situ et les mettre en corrélation avec les données en amont et en aval du processus.
Par exemple, nous mettons en œuvre une approche statistique de conception d’expériences pendant le développement du processus, en nous concentrant sur les paramètres clés du processus. Nous recueillons des données en cours de processus, principalement des signatures thermiques, pendant l’impression et nous les analysons pour identifier les propriétés clés du matériau, telles que la porosité. Ce processus nous permet d’optimiser nos opérations sur la base de preuves empiriques. Notre centre d’essais de propulsion interne, qui est très bien équipé, nous permet de valider les propriétés des matériaux par des essais fonctionnels des composants réels, plutôt que de nous fier uniquement à des coupons ou à des échantillons représentatifs. Cette approche permet une évaluation plus précise et plus directe de la manière dont les matériaux se comporteront dans les applications finales pour nos clients.
Bien que nos solutions internes Agile puissent accélérer le développement et la qualification des processus, nous ne sommes pas une société de développement de logiciels. C’est pourquoi nous restons vigilants et adoptons agressivement les avancées en matière de logiciels et de matériel qui peuvent encore améliorer notre capacité à transformer de vastes ensembles de données en informations exploitables ».
Même si elle se concentre sur les technologies de FA, Agile reconnaît que « la FA n’est pas une panacée », ce qui est essentiel pour définir une stratégie de fabrication plus large. Comme je l’ai déjà dit, la FA ne bénéficie pas du siècle de recherche sur la production de composants qui caractérise les techniques soustractives de précision. Cela signifie qu’à un moment donné, malgré la médiatisation actuelle de la FA, tout au long de la chaîne de valeur de la fabrication, il y a encore certaines choses que les processus de fabrication soustractive font mieux, et qui nécessitent encore beaucoup d’améliorations du côté de la FA.
Chez AGILE, il s’agit d’assurer une approche synergique de la production :
« L’équipe chargée de la fabrication additive tient à remercier Oqton et TRUMPF de nous avoir permis d’y arriver. Être une entreprise ‘agile’, c’est notamment pousser les logiciels et le matériel au-delà des capacités actuelles. Nous apprécions que les équipes d’application et de développement des entreprises travaillent avec nous pour ajouter des fonctionnalités là où nous en avons besoin. Les lecteurs de ce magazine [3D ADEPT MAG] peuvent vivre et respirer la fabrication additive, mais presque tous les programmes nécessitent des opérations d’usinage. Il s’agit donc d’un autre rappel pour considérer et remercier vos machinistes. »
Perspectives d’avenir
Avec une décennie d’expertise dans les essais à chaud et la conception et le développement de systèmes, Agile Space n’a rien à envier aux autres. Si son utilisation croissante de la FA en fait une entreprise à suivre en cette ère dédiée au nouvel espace, j’espère la voir explorer des processus de FA qui vont au-delà du procédé « LPBF » et je suis curieuse de découvrir les leçons qu’elle aurait tirées de cette exploration.
Toutefois, l’entreprise est impatiente d’explorer bientôt une gamme de technologies qui étendent les capacités de la fusion laser sur lit de poudre.
« Même si les choses amusantes restent secrètes, nous pouvons vous faire part de notre intérêt croissant pour l’incorporation d’alliages plus réfractaires et des perspectives passionnantes d’expérimentation avec des matériaux conçus par calcul. Notre objectif est de faire progresser notre expertise en matière de compensation thermo-mécanique et de logiciels de conception additive afin de créer des propulseurs innovants. Par exemple, les nouveaux composants peuvent incorporer des caractéristiques complexes qui sont restées difficiles à qualifier, telles que le treillis fonctionnel, ou nécessiter des orifices répétables d’un diamètre inférieur à 100 microns. En outre, à mesure que nous progressons vers 2024, certains de nos anciens composants pourraient s’éloigner de la fusion laser sur lit de poudre et s’adapter à des technologies additives plus récentes qui correspondent mieux à l’évolution de nos besoins de production.
Au-delà du domaine de notre département de FA, l’expérience d’AGILE dans le développement de propulseurs pour divers clients nous a permis de mieux comprendre les divers besoins du marché de la propulsion de satellites. En tant que leader dans le développement de moteurs de fusées spatiales, nous avons acquis une compréhension complète des exigences de nos clients en matière de réalisation de missions. La FA, pierre angulaire de notre processus de fabrication, jouera un rôle essentiel dans ces projets. Nous prévoyons d’exploiter les capacités de la FA dans ces nouvelles applications, et nous prévoyons de partager d’autres mises à jour à ce sujet dans un avenir proche. Notre orientation stratégique pour 2024 ne consiste pas seulement à faire progresser notre technologie de FA, mais aussi à l’aligner sur les besoins et les aspirations plus larges de nos clients, afin de rester à la pointe des solutions de propulsion spatiale », ont conclu Graybill et Crouse.
Cet article a initialement été publié dans le numéro de Janvier/Février de 3D ADEPT Mag. Images: Agile Space Industries