Titanium and its alloys have been readily used in many industries to great effect however it is the aerospace sector which has seen the main benefits. Titanium has very high strength and low mass giving the coveted high strength-to-weight ratio alongside its chemical and corrosion resistance and ability to work in high-temperature environments. Titanium has been and continues to be an important alloy across civil and defence aviation.
In a world post-Brexit, Covid and amid conflict in the Ukraine, alongside increasing tensions in the South Pacific, there is a geopolitical situation in which the future needs for titanium within the aerospace sector are put at risk for supply. Russia and Ukraine have long since had key contributions to the titanium supply market and within the whole of the West of Europe there is not a single capability that can process titanium in its rawest form, sponge. In the US the Department of Defence has addressed similar concerns with significant funding for operations looking to produce this critical mineral in land. The Western world feels the same pinch.
The graphics below shows the standard flow of titanium from source to end of life:
The US has a much better utilization of titanium from end of life and scrap on shore already compared to the UK and Ireland. This is of course a great thing however it does not truly support high-value manufacturing need for security in supply and to minimize the impact that conflict can have on access and cost.
Focussing in on the UK and Ireland, we can see the relative quantities of titanium and the flow in which they take through processing and industrial vertical routes. Whether the end of life is short or long term there is not any significant recycling capability. That is until now.
Additive Manufacturing Solutions Ltd (AMS), based in Lancashire, UK has developed a solution to the titanium supply problems facing the supply of metal powders for Additive Manufacturing.
AMS are an expert in metal additive manufacturing with its training academy, the AMA, alongside its process excellence. The final addition to this is their material development capability. AMS has metal powder AM processes in house in which the energy source, electron beam or laser, melts the powder in these selectively defined areas.
The titanium powder market globally is worth just a fraction of the global titanium market and the supply fluctuations induced by conflicts have a larger impact on the titanium powder market. Over recent months, the availability of titanium powder and prices have ranged from $150-275/kg and lead times up to 5 months for supply in some instances. With the Global Combat Aircraft Programme (GCAP), AUKUS alliance for submarine supply and a buoyant market in the UK and the US for space manufacturing the need for titanium and the opportunity for AM are large but the risk in supply is also high.
AMS has therefore developed a solution called R2. AMS was awarded funding from Innovate UK to build technical feasibility into its theoretical approach to turning aircraft parts into powder. This project was successful, and the process was optimized. AMS’ first major customer was the Ministry of Defence (MoD), due to the availability of titanium aircraft parts as a potential supply the MoD, wants and can play a key role in the future supply of AMS’ high-value circular economy product, a recycled titanium powder. Used in 100% recycled or a recycled blend (like many food packaging), AMS can support the supply chain risk mitigation for the UK and its allies but perhaps more importantly is a key enabler in a more sustainable future.
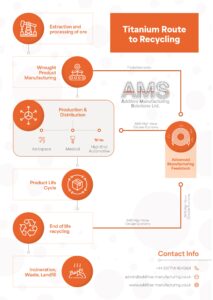
AM is often touted as a sustainable manufacturing process due to its minimal waste capability. Though one could argue that the energy used to create powder versus the energy waste in the production of scrap from a machining process for example makes them very similar a process.
The unique opportunity for remaking powders and creating a fully circular opportunity does provide a potential significant energy saving. The feedstock for the R2 process does not need to be mined, sponge created, cast, wrought and moved thousands of miles so the footprint left by the material reduces significantly. AMS estimates that the R2 process creates just 3% of the embedded carbon of a virgin-produced powder.
Supply chain security, minimizing the environmental impact, increased resilience, and the development of a UK feedstock supply, all developed in the UK. AMS has future developments underway for alternate critical metals, and other forms, like rod and wire underway, AMS’ tag of innovative solutions for a sustainable future seems to be very fitting. AMS is also developing a deployable variation of this capability allowing at point of need capability.
With a critical mineral supply at its heart and unaffected by the geopolitically turbulent world we live, AMS believes its technology has a bright future. AMS’ Founder and CEO, Robert Higham states, “AMS was created to bring our process expertise for material development and AM to support the growth of our industry. To do this, the need for a controlled supply of feedstock became our mission. We now have proven what is possible for innovation and sustainable-minded companies. Please reach out to us if you want to work with us across material supply or AM. Let’s change the world of advanced manufacturing together”.
Contact details:
This article has first been published in the May/June edition of 3D ADEPT Mag. Featured image:The image shows the laser interaction with powders at AMS’ facility
admin@additive-manufacturing.co.uk
www.additive-manufacturing.co.uk