Among the various 3D printing solutions that education and research centres explore, very few are often dedicated to ceramic filaments. A recent work performed by The Centre des Matériaux revealed interesting insights into the use of Zetamix filaments in one of their experiments.
The range of filaments has been developed by Nanoe, a French ceramic 3D printing expert. “Zetamix is the first line of ceramic filaments. They are mainly composed of ceramics and polymer binder in a minority. Such composition gives the filament a certain flexibility. The filaments are very easy to use and to integrate, features that make it easier for companies to delve in AM ceramics”, Nanoe’s founder Guillaume de Calan states in a conversation with 3D ADEPT Media.
The Centre des Matériaux is a unit of MINES ParisTech – PSL and is also a Joint Research Unit of the CNRS[3] (UMR 7633 ) the CNRS, specialized in Materials Science and Mechanical Modeling with a particular attention to new materials obtained from processes such as AM. Most of the centre’s researches aim to assess the influence of the fabrication processes on material properties as-produced or with aging conditions involving severe environment. Despite the use of specific samples for high temperature environments, regular sample holders do not allow to achieve these experiments. That’s the reason why, the research team decided to explore Zetamix alumina filaments in their experiments.
“In order to study the differences of properties between a metal made by melting foundry and one made by SLM (Selective Laser Melting), MINES ParisTech had to equip themself with highly customized sample holders for tensile test. Indeed, producing a metal part by SLM is far from easy and needs a furnace post treatment: after the printing process, tensile test specimens had to be annealed”, a report reads.
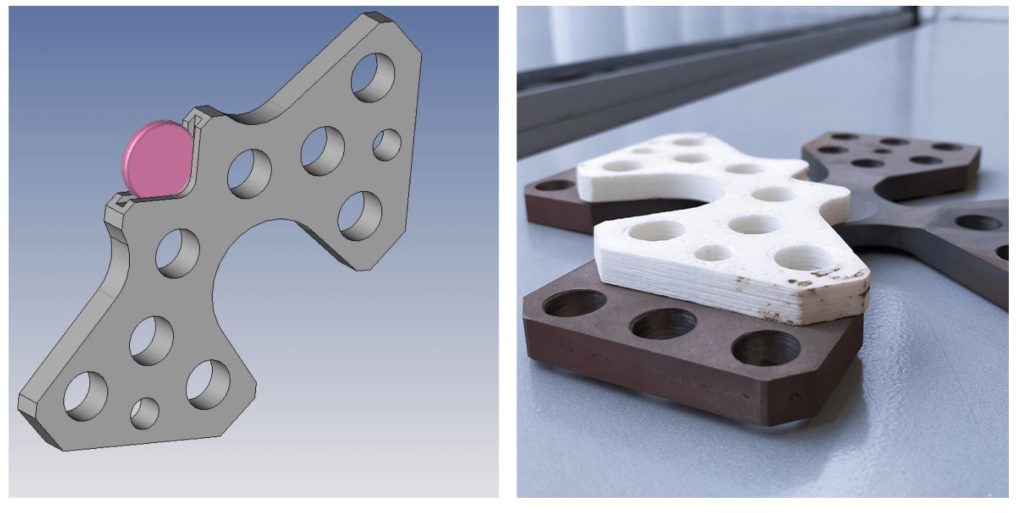
However, one of the high-temperature mechancial testing experts, Sylvain Gailliegue wanted to anneal several SLM samples in a tubular furnace simultaneously in order to save time, and make sure all the parts were heated with the same conditions. This idea raises a number of issues such as the fact that test samples must not touch each other in the tubular furnace, or the fact that they have to remain in the centre of the tubular furnace where the temperature is homogeneous, hence the need for a customized sample holder. This sample must withstand high temperature and must be non-conductive for the inductive system.
“Indeed, to resist to heat treatment, they have to be in a refractory and stable ceramic like alumina. Thanks to Zetamix, Sylvain succeeded to produce a perfect fit alumina tensile test specimen holder that solved all the issues previously mentioned”, the report explains.
The customized sample holder has been produced in a material which fills this two constraints : Alumina.
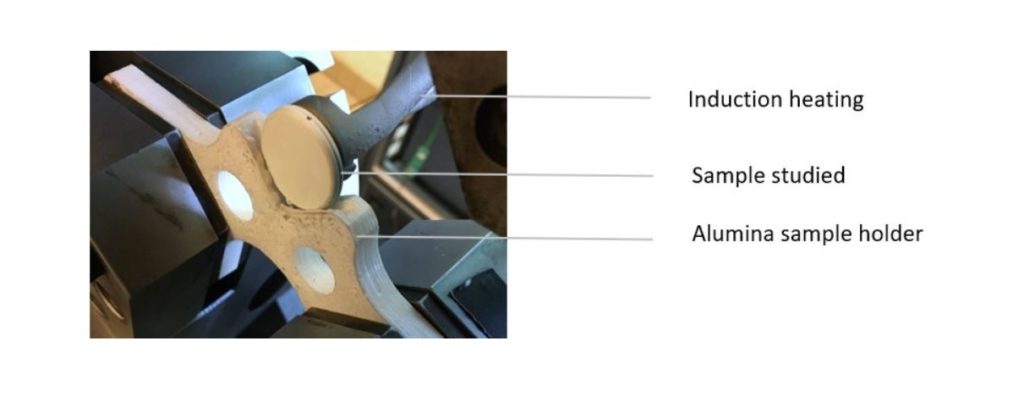
“Once again, alumina is an expensive material when it is produced in small quantities, and Sylvain cannot afford to outsource the production of this sample holder. In the same way than for the previous sample holder, Sylvain printed an alumina part perfectly adapted to the machine thanks to Zetamix”, the report concludes.
Remember, you can post job opportunities in the AM Industry on 3D ADEPT Media free of charge or look for a job via our job board. Make sure to follow us on our social networks and subscribe to our weekly newsletter : Facebook, Twitter, LinkedIn & Instagram ! If you want to be featured in the next issue of our digital magazine or if you hear a story that needs to be heard, make sure to send it to contact@3dadept.com