Remember MANTLE, the start-up that develops a hybrid metal 3D printing based on metal pastes? Well, ever-since it unveiled its Trueshape technology, the company decided to focus on tooling to demonstrate its capabilities. As you may know, tooling is the backbone of the manufacturing industry and the latest collaborations the company worked on, revealed that there are always new things to learn from these applications.
As part of collaborations with WESTMINSTER TOOL, WEPCO PLASTICS, as well as Precision Laser Technology and Craftsman Manufacturing, MANTLE demonstrated value of conformal cooling for bio-based, 65% glass-filled polymer, surface finish superior quality and the ability of its H13 material to undergo welding and/or machining without any change.
In each collaboration with industry partners, Mantle tool components printed with its H13 Flowable Metal Paste material showed equivalent performance to conventional H13 tool steel. Together, these studies underscore the benefits of Mantle’s TrueShape technology in quickly printing precision components for prototype and production tools, molds, and dies – and going from designs to molded parts in weeks, a press communication reads.
Conformal cooling handles demanding bio-based polyamide
For a better assessment of a 3D printing technology, it’s often interesting to compare what is usually done with a conventional manufacturing process.
As part of the project with Westminster, the producer of manufacturing tools for injection molding machines wanted to make tooling inserts (core and cavity) so they could quickly mold medical forceps sample parts. Usually with drilling conventional metal tooling, they produce straight lines and right angles. With Mantle’s technology on the other hand, they can print spiral cooling/heating channels that wrap around former hard-to reach or tall-and-deep geometries. Also known as conformal cooling, this permits molders to 2 control mold temperatures better, shorten cycle times from 25 to 75 percent, improve dimensional stability and surface finish, and facilitate demolding.
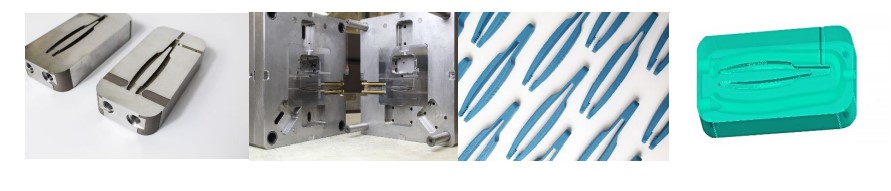
Westminster Tool wanted to mold the forceps from a highly glass-filled, bio-based PA11 called Rilsan® FKZM 65 O TD MED, made by Arkema. The material, supplied by a third collaborative partner, Foster Compounds, is focused on surgical device applications and features USP Class VI and ISO 10993 biocompatibility. Healthcare device manufacturers have embraced sustainability goals, and the new bio-based material aligns with this demand.
According to Westminster Tool’s Manufacturing Engineer, Eddie Graff, a traditional aluminum prototype tool would present difficulties in molding the highly glass-filled PA11. To solve the problem, he turned to Mantle. Graff designed the tool inserts to include conformal cooling channels. “These are more effective at controlling the cavity temperature, which is critical to molding this particular material,” says Graff. Mantle then printed the inserts in only 86 hours. “In the end, it took us three weeks to go from design to FOT, quality medical parts on a prototype tool. It’s incredible,” he adds. Mantle’s metal 3D printed inserts held a tolerance of +/- 0.0015”. Because they were made with H13 steel, they allowed Westminster to add a subgate so that they could mold thousands of parts without the risk of gate erosion.
Surface finish superior quality
The collaboration with Wepco Plastics (Middlefield, Connecticut), a prototype injection molder, ambitions to evaluate the technology when molding a cellphone stand representative of the consumer market, in which surface finish is often critical to quality.
Mantle’s TrueShape™ technology therefore fabricates inserts with a smooth matte surface finish suitable for molding, with a mere 1-3µm Ra surface roughness. Wepco Mold Designer Steven Kronenberger worked closely with Mantle’s Senior Application Engineer Scott Kraemer to design the inserts and conformal cooling channels. Mantle then printed them in about 80 hours.
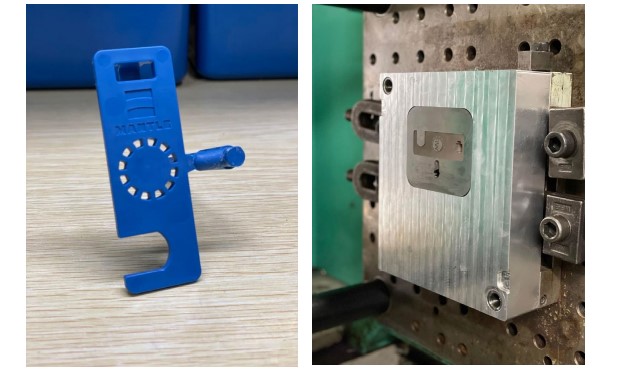
Processing setup was swift, and molding the parts in both blue and black ABS plastic produced smooth surface finishes without the time required for polished aluminum, according to Amanda Wiriya, Manufacturing Support Director at Wepco. Not only that, but the machine operators were impressed with how easily parts came off the tool. “We’ve had issues in the past demolding parts from 3D printed plastic inserts,” says Wiriya. “This was a totally different experience.”
Machining and welding like tool steel
While Mantle’s TrueShape technology produces highly accurate tools, these tools may still require welding and/or machining to address engineering changes or reconditioning over a 4 tool’s life cycle. A third project sought to verify that Mantle’s H13 material could undergo these processes without any change to existing machining and welding processes.
This study was conducted with Precision Laser Technology (PLT, Rochester, New York), a service provider focused on laser welding, engraving, texturing, and direct part marking for injection molds and molded plastics.
For the test, Mantle printed four H13 test bars, and Natale turned to another partner, Kevin Contestabile of Craftsman Manufacturing (Rochester, New York), to precision mill and grind them. “We wanted to replicate a real-world environment for mold components, one we see as a service provider in the industry,” said Natale. “This would enable us to test how Mantle’s inserts held up to engineering changes or worn parting lines that require welding. We also wanted to test how easy it would be to machine the insert to tighten up tolerances.” Contestabile performed CNC machining to add a notch and ground three of the four sides. “There was zero evidence of pitting, and the material showed no signs of wheel loading or heat generation using conventional grinding methods,” adds Natale.
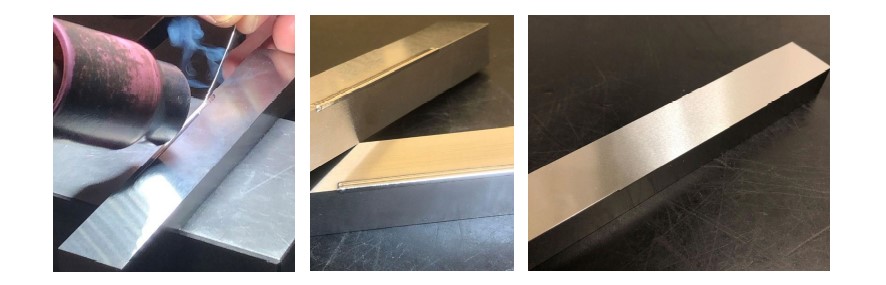
PLT welded the notch to simulate adding material for an engineering change or building up a worn parting line in a mold. The material accepted the filler wire readily, and Contestabile post-ground the bar again. The end results were indistinguishable from traditional H13 tool steel. Natale says, “It was a seamless experience, and didn’t disrupt any of the processes in our shop. There were no requirements for special tooling or alterations to the process because of the material. Performance was consistent with conventional H13.”
Remember, you can post job opportunities in the AM Industry on 3D ADEPT Media free of charge or look for a job via our job board. Make sure to follow us on our social networks and subscribe to our weekly newsletter: Facebook, Twitter, LinkedIn & Instagram ! If you want to be featured in the next issue of our digital magazine or if you hear a story that needs to be heard, make sure you send it to contact@3dadept.com