Sugar is not always meant to be edible. Its applications can also serve science and bring a significant contribution in biomedical engineering, cancer research and device manufacturing. Today’s discovery starts with the manufacturing of a specific 3D printer. The 3D printer we are talking about today has been especially manufactured to produce a network of thin ribbons of hardened isomalt (it is the type of sugar alcohol used to make throat lozenges.)
Through a technique called Free-form printing, the nozzle of the 3D printer moves through space, the melted material hardens, leaving a sturdy structure behind – like drawing in midair.
“This is a great way to create shapes around which we can pattern soft materials or grow cells and tissue, then the scaffold dissolves away,” said Rohit Bhargava, a professor of bioengineering and director of the Cancer Center at Illinois. “For example, one possible application is to grow tissue or study tumors in the lab. Cell cultures are usually done on flat dishes. That gives us some characteristics of the cells, but it’s not a very dynamic way to look at how a system actually functions in the body. In the body, there are well-defined shapes, and shape and function are very closely related.”
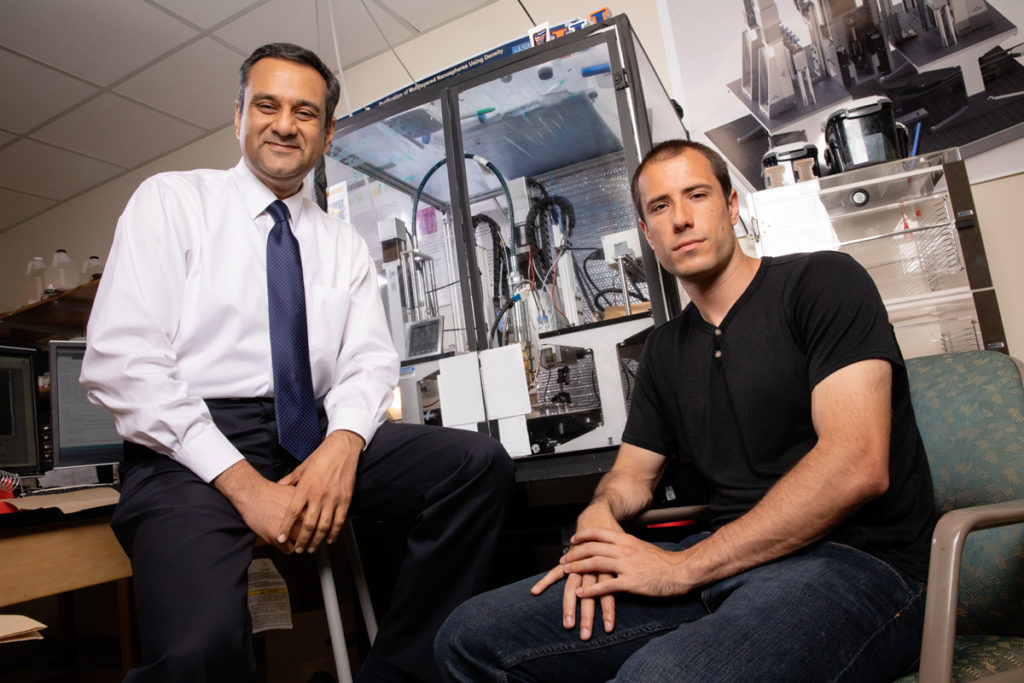
Photo by L. Brian Stauffer
However, it should be noted that other types of sugar printing could have been used in this research; the only thing is that researchers would have faced problems with the sugar burning or crystallizing hence their choice for the sugar alcohol isomalt. This is also the reason why they needed a specific 3D printer that could accurately print stable isomalt structures.
Two main advantages are observed with such type of 3D printing:
- The capacity to manufacture thin tubes with circular cross-sections, which is not possible with conventional polymer 3-D printing. Indeed, while dissolving, the sugar “leaves a series of connected cylindrical tubes and tunnels that can be used like blood vessels to transport nutrients in tissue or to create channels in microfluidic devices.”
-
A 3-D printed bunny made of isomalt sugar mixed with a glowing red dye used in biomedical imaging.
Photo by Troy Comi - The possibility to control the mechanical properties of each part of the structure without drastic changes in the parameters of the 3D printer.
The scaffolds are used today in microfluidic devices and cell cultures.
This research is part of Matthew Gelber’s thesis work who gave further details on the manufacturing of algorithms. Rohit Bhargava and Matthew Gelber hope that their models can be used to develop other applications for isomalt structures.
For further information about 3D Printing, follow us on our social networks and subscribe to our newsletter
Would you like to be featured in the next issue of our digital magazine? Send us an email at contact@3dadept.com