Engineering design and manufacturing company Triton Space Technologies, LLC has invested in METHOD X 3D printer to produce 3D printed functional components for the 2021 lunar mission.
Lunar missions are landers that carry small payloads and experiments to the lunar surface. Such type of missions involves the production of rocket propulsion systems. Commissioned by NASA, the mission will allow two companies to carry out the landings under NASA’s Commercial Lunar Payload Services (CLPS) program.
The team at Triton Space Technologies on the other hand, has been commissioned to build some valves that will be used as part of this mission.
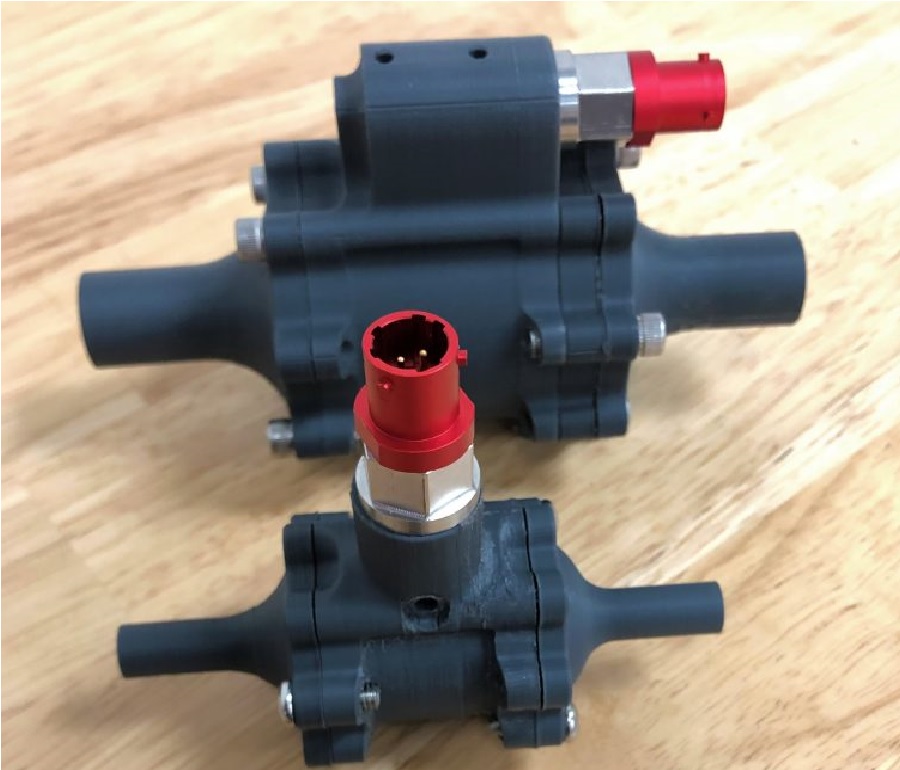
“We wanted to create a functional prototype of the valve, to check that all the parts fitted together properly, and that the internal parts could slide and move as they should. We went into it not really expecting that the METHOD X would be able to keep the tolerances needed for the sliding parts to move, but it did”, states Luke Colby, Founder and CEO of Triton Space Technologies.
The expert in the production of rocket propulsion systems usually provides prototype manufacturing services using an in-house CNC machine shop. As propulsion engineer, the founder of Triton Space Technologies had only used large-scale industrial 3D printing machines throughout his career. The use of MakerBot METHOD X™ 3D printer made him realize that desktop machines could be used to produce truly functional prototypes.
“The METHOD X 3D printer has evolved as a tool, providing us with a high level of reliability during part production. In our line of business, this is essential – especially in comparison to other 3D printers where there’s a risk that the final part will not come out as you’d expect. METHOD X mitigates risk by helping us to answer questions much earlier on in the design phase, so that’s very valuable,” said Colby.
“We also used the METHOD X to create a prototype of an injector head assembly for the manifold of a small rocket engine,” explained Colby. “The idea was that it should have one common, sliding surface that would open up flow passages for both propellants at the same time. That would not have been possible with traditional manufacturing methods, as you end up with an assembly of many different parts coming together with a whole lot of seals in between them.”
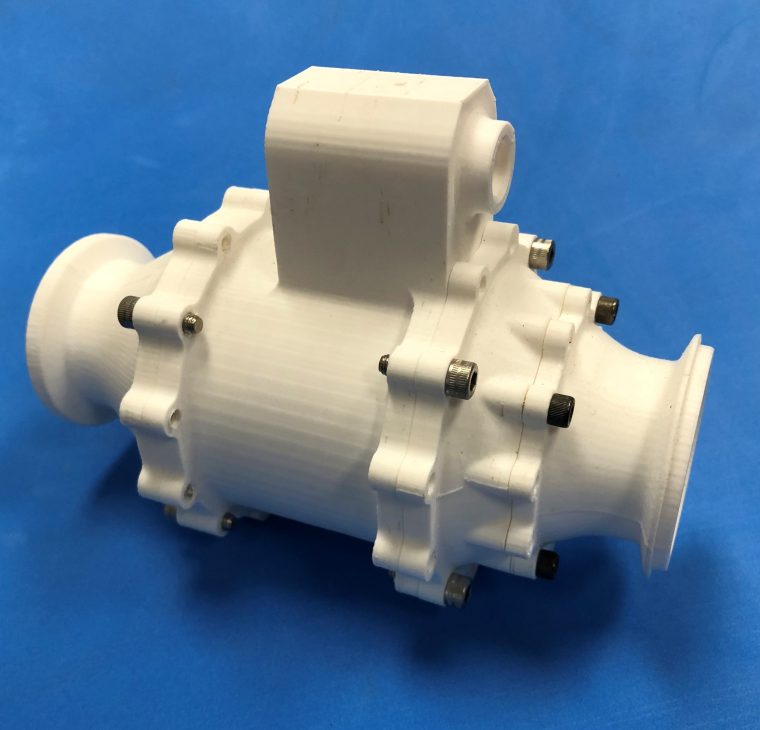
Using the Stratasys® SR-30 soluble support material, the team achieves prototypes with the tolerances required for the demanding aerospace industry. They explain that if they do not use supports, or if they use snap-off supports, parts would have to be filed and sanded, greatly reducing their utility.
As for materials, the engineering company outlines the benefits of real engineering-grade ABS and MakerBot Nylon Carbon Fiber to print prototypes. However, as most products quickly become obsolete, they are keen to further investigate on what they can do with different materials using the modularity of the METHOD extruders.
Remember, you can post free of charge job opportunities in the AM Industry on 3D ADEPT Media or look for a job via our job board. Make sure to follow us on our social networks and subscribe to our weekly newsletter : Facebook, Twitter, LinkedIn & Instagram ! If you want to be featured in the next issue of our digital magazine or if you hear a story that needs to be heard, make sure to send it to contact@3dadept.com