Avoir une idée, c’est facile, la mettre en œuvre l’est beaucoup moins. Dans l’industrie manufacturière et technologique, des idées surgissent tous les jours. Cependant, la plupart des fondateurs choisissent de rester en mode furtif jusqu’à ce qu’ils aient un MVP (Minimum Viable Product) à présenter au marché – à juste titre, étant donné les risques qui sont souvent impliqués. Il est intéressant de noter que, cette année, dix start-ups se sont démarquées et ont présenté leurs produits et services pour la première fois au secteur de la FA « glocale » ( mot valise combinant les mots « global » et « locale »). Les voici.
Q.big 3D GmbH
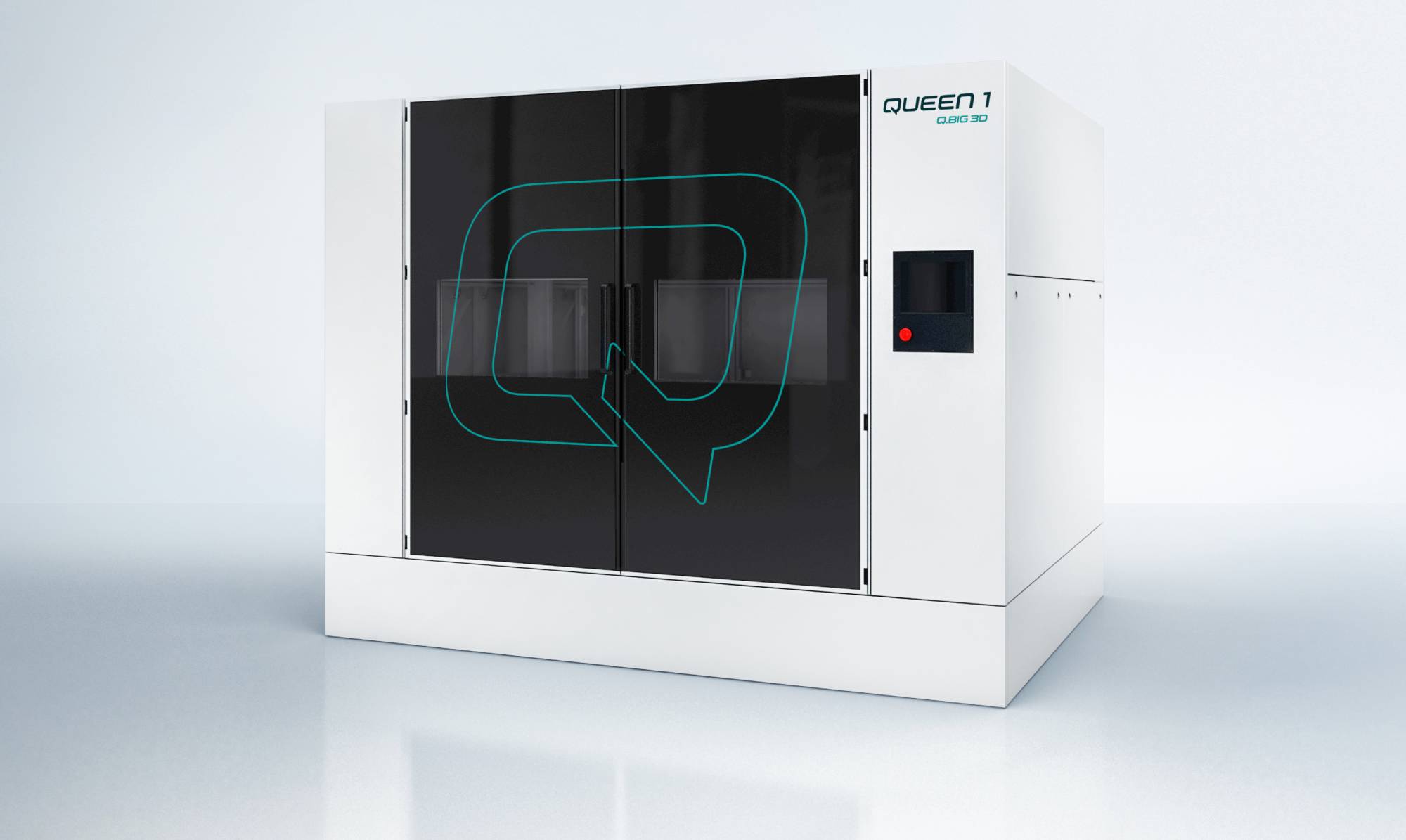
Fondée en 2019, cette startup basée en Allemagne développe des imprimantes 3D à grande échelle basées sur un procédé appelé VFGF (Variable Fused Granular Fabrication). Je les ai vus pour la première fois à AM Forum de Berlin. Leur technologie traite des granulés de polymère (plastique) dans une seule extrudeuse. Variable parce que l’impression haute résolution n’est utilisée que lorsque les contours les plus fins et les bonnes qualités de surface sont nécessaires. Partout ailleurs, le débit de matière est beaucoup plus élevé, affirme l‘entreprise. Leur produit phare s’appelle Queen 1. Je ne sais pas ce qui a inspiré ce nom, mais je l’aime bien. Il est facile à retenir, et il implique quelque chose de majestueux – ce qui est le sentiment que les grandes choses devraient susciter. J’espère maintenant que leur produit sera à la hauteur de ce sentiment.
L’équipe semble ouverte aux relations commerciales avec toutes les entreprises du monde, mais ses actes montrent que sa principale zone d’intérêt est la région DACH pour l’instant, car la communication se fait principalement en allemand.
Additive Assurance
J’ai de bons sentiments pour ces gars. L’équipe est expérimentée et intéressante. Marten Jurg et le professeur associé Andrey Molotnikov, l’équipe fondatrice de l’entreprise basée en Australie, ont mis au point une solution d’assurance qualité compatible avec la fusion laser sur lit de poudre (LPBF). Baptisée AMiRIS, elle permet aux fabricants de s’assurer de l’intégrité structurelle des composants au fur et à mesure de leur fabrication et de corriger toute anomalie lorsqu’elle se produit.
Ils travaillent déjà avec quelques clients dans les industries aérospatiales et de fabrication avancée pour permettre l’utilisation de pièces imprimées en 3D dans la production en série. L’entreprise a terminé son année sur une note positive en obtenant un financement de 4,1 millions de dollars pour faire avancer ses activités de recherche et de développement et embaucher des équipes internationales de développement commercial.
AM Extrusion GmbH
Basée à Radebeul, en Allemagne, l’idée d’AM Extrusion est devenue réalité début 2021 lorsque Felix Alber, Aljoscha Roch et Sven Halank ont uni leurs forces pour développer une gamme de filaments métalliques et céramiques pour l’impression 3D.
« La disponibilité des matériaux est un seuil élevé pour l’utilisation industrielle de la modélisation par dépôt fondu, par ailleurs si avantageuse. Grâce à notre système de liant unique AM-Xcomp, nous sommes en mesure d’abaisser ce seuil et de transformer presque toute poudre métallique ou céramique disponible en matériaux frittables pour l’impression 3D. Nos filaments thermoplastiques AM-X, dont le brevet est en instance, se caractérisent par des taux d’enrichissement de la poudre sans précédent, d’excellentes propriétés d’impression et une application facile à une température presque ambiante. Les problèmes de déformation des pièces, les normes élevées de sécurité au travail, l’élimination des matières toxiques excédentaires et d’autres inconvénients des procédés de FA conventionnels appartiennent désormais au passé », indique la société.
Avec des capacités de production allant de 500 g à plusieurs centaines de kg, leur portefeuille de filaments comprend actuellement des métaux légers ou durs, du cuivre, de l’acier inoxydable ou des céramiques ; il peut être personnalisé si un filament doit répondre à des exigences particulières.
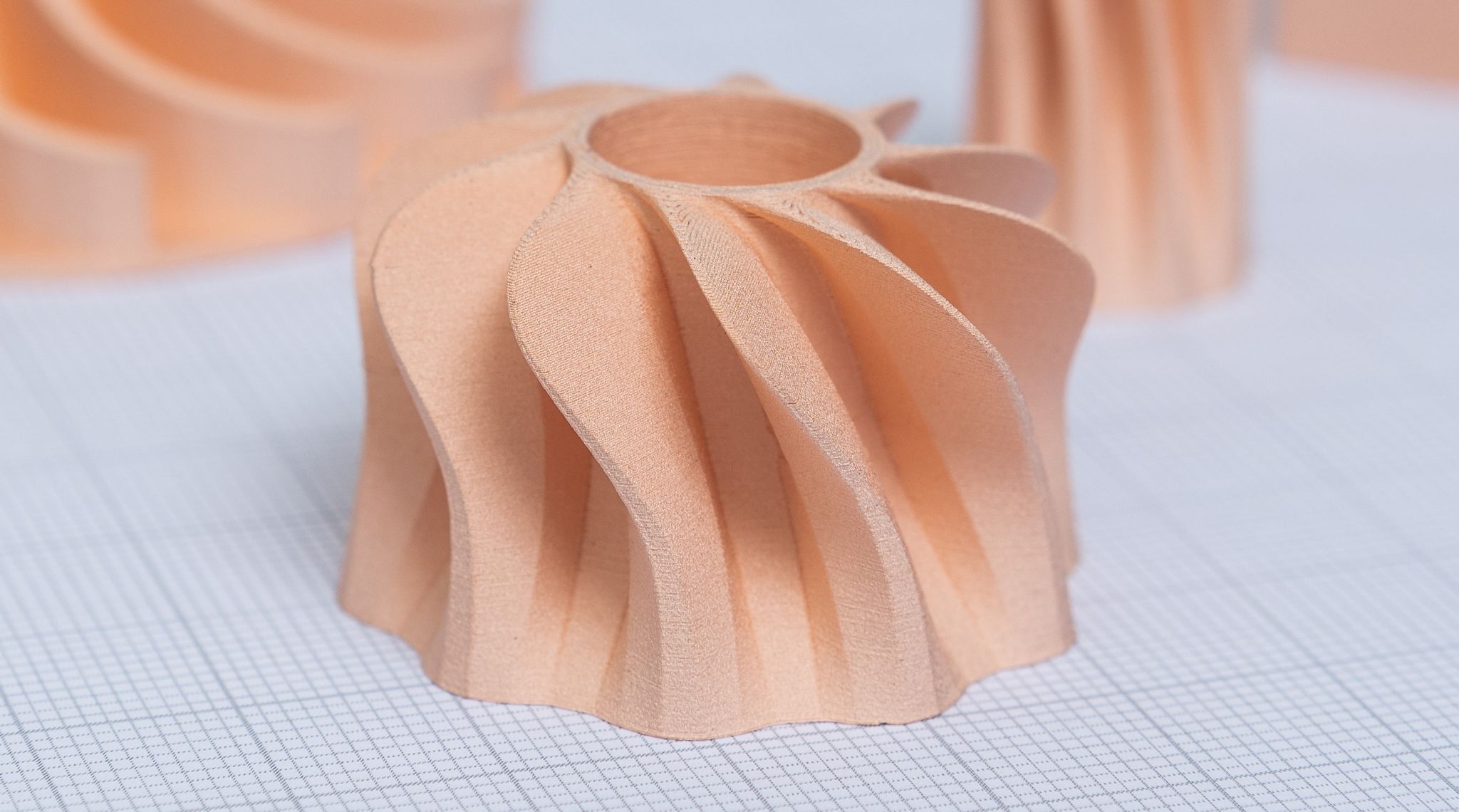
AM Extrusion a inventé un outil permettant d’imprimer facilement du cuivre. Pas de poudre en suspension dans l’air, pas d’exigences de sécurité élevées pour les employés, ni d’équipement de protection individuelle. Leur filament de cuivre spécial est introduit dans la tête d’impression d’une imprimante 3D. L’imprimante fait fondre le filament et extrude le matériau sur une plateforme de construction.
« Pour l’impression 3D de pièces en cuivre pur, nous avons inventé le filament AM-X Cu 99,97% qui contient un polymère rempli d’une poudre de cuivre de haute pureté à haute fraction volumique. La particularité de notre matériau est que le polymère peut être entièrement retiré après l’impression et que la poudre de cuivre peut être frittée facilement dans un four. Cela permet de consommer 100 % du matériau pour obtenir des pièces en cuivre. Nous évitons tout gaspillage de matériau et avons un processus de fabrication économe en ressources. Le matériau est utilisé de manière additive, exactement là où il est nécessaire », explique l’entreprise.
Namma
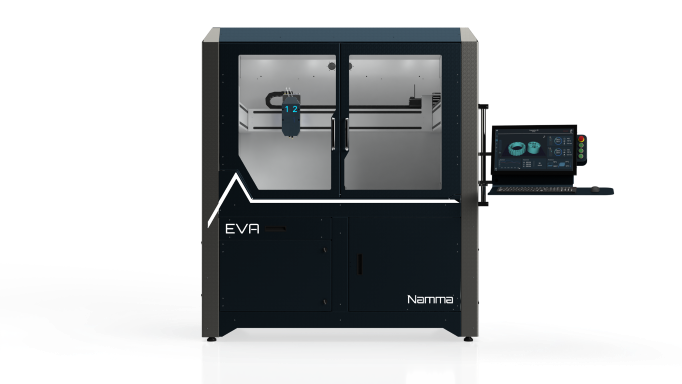
Namma est une autre startup que nous n’avons pas mentionnée l’année dernière dans notre liste des startups d’impression 3D créées dans une ère post-COVID-19. Basés en France, les ingénieurs derrière Namma croient au meilleur des deux mondes de la fabrication additive et de la fabrication soustractive. Leur produit phare est EVA, une imprimante 3D hybride qui combine l’impression 3D, l’usinage CNC et la gravure laser sur une seule plateforme. La machine intègre deux têtes distinctes qui peuvent fonctionner simultanément – l’une peut être une tête d’impression, et l’autre, une tête de fraisage ou de gravure laser ; ou vous pouvez avoir deux têtes d’impression uniques travaillant en même temps. EVA est livrée avec N-Center, sa propre suite logicielle qui permet à ses utilisateurs d’optimiser leur production à chaque étape du processus de fabrication.
TriTech Titanium Parts
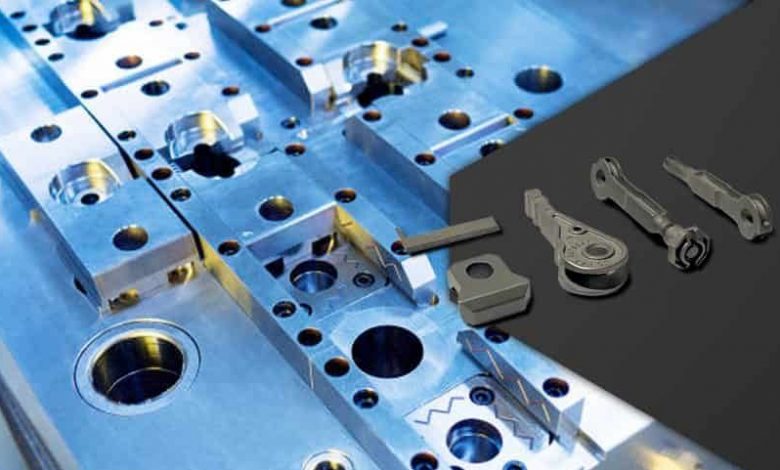
Les fabricants qui ont dans leur environnement de production l’impression 3D par jet de liant, le moulage par injection de métal et la fonderie de précision ont compris la puissance de leur complémentarité. Pour moi, ils ne peuvent qu’être à l’origine de quelque chose d’intéressant et qui vaut la peine d’être suivi.
TriTech Titanium Parts, un nouveau venu sur le marché, combine ces technologies dans son environnement de production. Lancée le 5 avril 2022, l’entreprise est une spin-off de l’ancienne société de son président, AmeriTi Manufacturing. Cette dernière a été vendue à Kymera International, également le 5 avril 2022.
Organisée en réponse aux besoins du marché, TriTech produit des pièces en titane de forme nette en utilisant la technologie la plus appropriée pour la pièce et le client. L’éventail unique des trois technologies de production de TriTech comprend l’impression 3D par jet de liant, le moulage par injection de métal et le moulage à la cire perdue. L’impression 3D est le dernier ajout, et le processus de jet de liant est un processus de fabrication unique et de pointe pour la production de pièces complexes en titane.
Fractal Additive
Fondée cette année par Olivia Krueger, cette start-up américaine propose deux services principaux : Les services contractuels d’ingénierie de conception et le remplissage fractal. Ma curiosité est éveillée pour ce dernier service : une solution qui crée des structures adaptatives et optimisées pour chaque pièce qui passe dans le slicer. Les économies de matériaux augmentent à mesure que l’échelle de la pièce s’accroît, sans que la résistance globale de la pièce ne soit compromise. Pourquoi est-ce que je trouve cela intéressant ? Parce qu’il est difficile d’innover dans le domaine de l’extrusion de matériaux (impression 3D FDM) et j’ai très envie de découvrir où Krueger peut aller avec cette solution…
Filaret
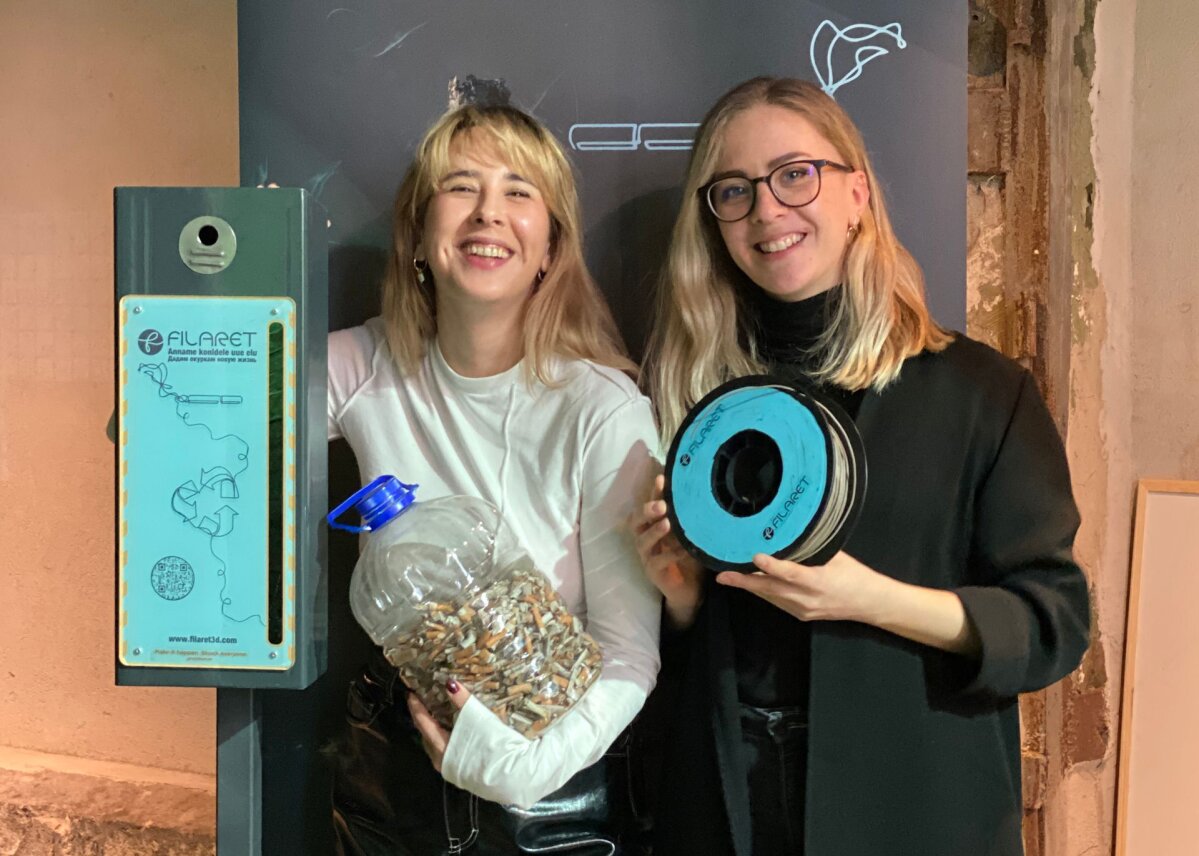
Saviez-vous que les mégots de cigarettes sont l’un des types de déchets marins les plus courants en mer Baltique ? Outre le plastique, la plupart des déchets trouvés dans la mer Baltique et dans les zones côtières sont des mégots et des filtres de cigarettes, qui sont toxiques et non biodégradables. Un seul mégot de cigarette peut polluer jusqu’à 1 000 litres d’eau, et les toxines libérées par le filtre dans l’eau peuvent persister jusqu’à 10 ans et devenir mortelles pour la vie aquatique.
C’est la raison pour laquelle Ines-Issa Villido et Kristina Jacqueline Leon, les dames dures à cuire derrière Filaret – basé en Estonie – se sont lancées dans une mission noble: faire des déchets recyclés une norme dans le secteur de l’impression 3D en collectant et en recyclant les mégots de cigarettes pour en faire un filament d’impression 3D durable, compostable et respectueux de la nature. Pour ce faire, ils ont installé des poubelles spéciales sur les plages du district de Põhja-Tallinn afin d’empêcher les mégots de cigarettes de finir dans la mer. Pour l’instant, aucune information n’a été donnée sur la transformation de ces mégots en filament. De plus, nous ne savons pas si le filament pourrait être utilisé à des fins de prototypage ou de production. Espérons que ces informations seront partagées à la fin de ce projet pilote par Filaret ou l’un de ses partenaires (le port de Tallinn et l’aéroport de Tallinn).
DUPLEX
Juste au moment où vous pensez qu’il n’y a plus grand-chose à attendre de l’impression 3D FFF, une entreprise vient vous prouver le contraire. Une tendance de fabrication très intrigante dans ce segment provient d’un nouvel entrant : DUPLEX. La marque rose présente MAP™ (production additive multidimensionnelle = multi-dimensional additive production), une technologie qui permet une impression multidirectionnelle. Non seulement cela accélère le processus de fabrication, mais ce procédé bidirectionnel réduit ou élimine également l’utilisation de matériaux de support, et facilite l’impression de géométries organiques. Parmi le large éventail de fabricants d’imprimantes 3D FDM présents sur le marché, je pense que DUPLEX est celui qui pourrait avoir un impact important.
Sinterjet
Basée en Turquie, Sinterjet est présente depuis quelques années sur le marché mais a fait sa première apparition cette année à Formnext. L’entreprise souhaite se positionner sur le marché des imprimantes 3D en métal abordables. Son produit phare, la Sinterjet M60, dont le prix est de 65 000 euros (68 000 dollars), est une imprimante 3D industrielle en métal d’un volume de 160 x 60 x 60 mm qui utilise la technologie d’impression 3D de jet de liant, un processus dans lequel une solution de liant liquide est déposée de manière sélective sur des couches de poudre jusqu’à la création d’un objet complet.
Comme vous pouvez le deviner, aucun matériau de support n’est nécessaire ici, car la poudre libre environnante fournit un support pour les surplombs. Avec une résolution de 1 200 x 1 200 ppp, la machine peut construire à une vitesse de 50 cc par heure. C’est assez rapide pour ce type de volume, non ? La machine est compatible avec une solution logicielle développée en interne qui serait facile à utiliser selon Sinterjet.
The Industry Sweden AB
C’est l’une des entreprises que nous avons rencontrées lors de la dernière édition de Formnext. (Comme nous l’avons dit dans le segment « EVENEMENT », il faut toujours laisser de la place à la promenade). En fait, ils sont sur le marché depuis un certain temps. Vous les avez peut-être connus sous le nom de BLB Industries – développant des imprimantes 3D pour les portes ; ils se sont mis en mode silencieux et nous avons perdu la trace de leur activité, puis ils se sont rebaptisés » Industry » l’année dernière dans le but d’adopter une nouvelle stratégie. Pour être honnête, il est difficile de dire si l’on doit toujours considérer l’entreprise comme une nouvelle start-up dans le secteur – étant donné qu’elle opère désormais avec un nom et une catégorie de produits différents. Quoi qu’il en soit, ce qu’il faut retenir, c’est que The Industry Sweden AB développe actuellement des systèmes FGF (fused granule fabrication), qui utilisent des granulés thermoplastiques plutôt que des filaments pour imprimer des pièces en plastique 3D.
Avec une zone de construction de 1500x1200x1200 mm, le système FGF est idéal pour l’utilisation de plastiques recyclés, car le nombre d’étapes de traitement est réduit pour convertir la matière première en matière première par rapport aux filaments. Il sera également capable d’imprimer des caoutchoucs et certaines charges en biofibres comme le bois, le chanvre et le lin.
L’entreprise affirme que son changement de marque est le début d’un nouveau modèle commercial évolutif qui se concentrera sur le développement d’une forte reconnaissance de la marque, avec de nouveaux produits et des stratégies de lutte contre la pollution plastique.
Disclaimer : Un certain nombre de grandes entreprises ont également décidé de créer leur division de FA cette année, elles ont été volontairement exclues de cet article pour mettre en avant les PMEs et les fondateurs qui construisent leur entreprise à partir de zéro.