Needless to recall the monumental changes that helped many industries appreciate and consider the potential of additive manufacturing. With over 300 metal additive manufacturing (AM) systems available on today’s market, most of them being closed and proprietary systems, we cannot help but think to the long road ahead and the challenges that still need to be addressed. How can operators access knowledge about additive manufacturing processes? How can they address the limitations in terms of materials and achieve more applications? How can they have greater control over the manufacturing process? For a niche of experts on the AM market, the answer to these questions is to: “rely on open additive manufacturing platforms”.
This feature discusses the rise and the reasons that led companies to consider “Open Manufacturing”. Most importantly, it aims to give manufacturers in various industries another option to consider when it comes to investing in metal additive manufacturing technologies.
The concept of “open manufacturing” is not new. On the contrary, it is relatively simple to understand. The term is linked to the idea of democratizing technology as embodied in the maker culture and other areas for grassroot innovation such as hackerspaces. It consists in combining new production tools, processes (3D printers) and protocols for manufacturing.
As far as AM is concerned, manufacturers struggle to understand and apply it to the current industrial environment. WHY? To answer this question, we invited two of the “must know” companies that are currently paving the way to more “openness” in additive manufacturing: Dyndrite and Open Additive.
Dyndrite™ is on a mission to delivering advanced technology for the future of digital manufacturing. Founded in 2016, the company has developed the Dyndrite Kernel, an accelerated geometry kernel that enables companies to build next generation software or additive manufacturing hardware easier and faster than ever before. Next to this flagship product, the company has been acknowledged for its Dyndrite Developer Council, central component to the Dyndrite Developer Program which provides tools, resources and community for original equipment manufacturers (OEMs), independent software vendors (ISVs), service providers and educators.
Open Additive is another one to watch when it comes to open additive manufacturing systems. With the goal of providing affordable metal AM systems, Open Additive stands out from the crowd by providing customizable solutions to the additive manufacturing industry.
Harshil Goel, founder and CEO of Dyndrite™ and Ty Pollak, President and CEO of Open Additive share key insights into this topic.
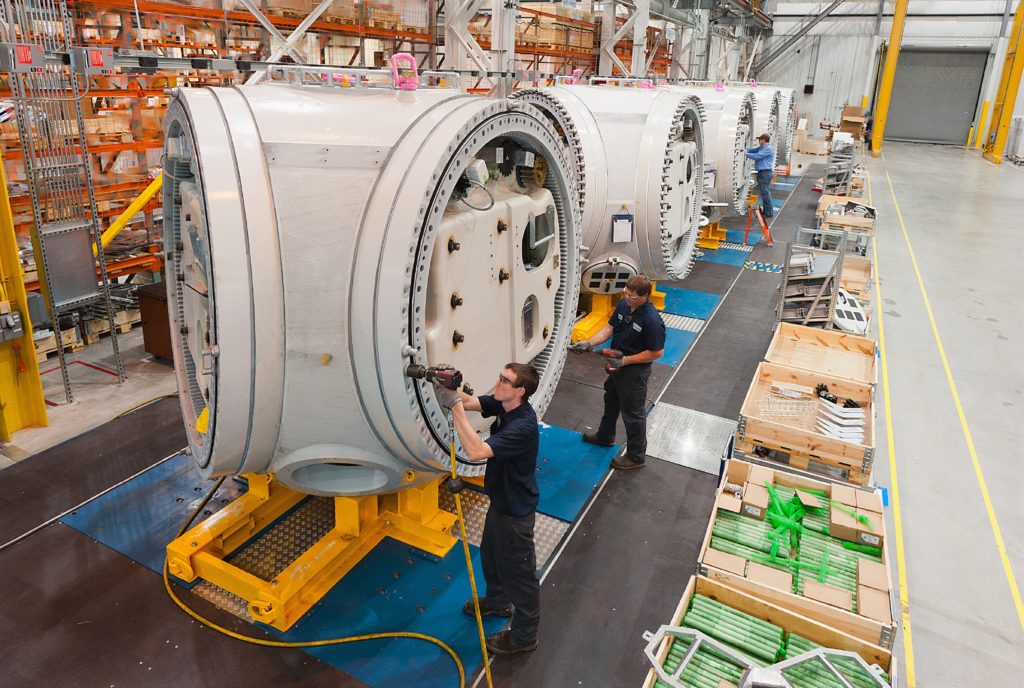
How should we recognize an “open” additive manufacturing platform?
First, there is not yet a standard definition of “open additive manufacturing platforms”. 3D printer manufacturers that are currently developing and providing open additive manufacturing platforms first aim to meet the demand for better quality materials, more applications, thus customisation. This issue has become inherent for many manufacturers including Origin, Arburg or even Freemelt.
Let’s take the example of polymer 3D printing. 3D printer manufacturers Origin and Arburg have opened the doors to material companies that are now adapting a wide range of materials usually leveraged in injection moulding. Operators can for instance, choose between different amorphous injection-molding granulates to produce not just mockups, but real functional components.
In the same vein, to broaden the Electron Beam Powder Bed Fusion (PBF-EB) material portfolio and application areas, Sweden-based manufacturer Freemelt AB develops an open source material development system that enables operators to try new materials and innovative beam scanning strategies. That’s a wise strategy, especially in PBF-EB where the biggest hurdle that slows down the wider adoption of this process is material development.
Reality is, unlike polymer-based 3D printers, which essentially require the development a whole range of materials, metal 3D printers are known for the use of wire (metal powders) and feedstocks from industries that already existed. As a matter of fact, the rule says, if a metal welds or casts well, then it should also be amenable to additive manufacturing. However, what this rule does not take into account is the virtuous cycle of the AM industry. This virtuous cycle states that “the more designers design products, the more applications we will have. The more applications there are, the more materials will be developed, and the more printers will evolve or be introduced to the market.” Ultimately, this cycle reinforces the growth of the industry but it also raises many of its challenges.
While looking at the development of metal AM systems, part of these challenges shows that materials cannot be the only factor that should be taken into account to qualify an open additive manufacturing system.
Other key characteristics of an open additive manufacturing platform
In addition to “open materials”, other elements should be kept in mind while looking for an open AM platform, elements that have strong counterarguments raised by manufacturers of well-established Industrial 3D printers.
Open Architecture VS Closed Architecture.
Closed systems have been the standard across industrial additive manufacturing. The only thing is that such option often locks manufacturers into one vendors’ hardware, processes and materials. Simply put, open architecture and closed architecture can be seen as two faces of the same coin.
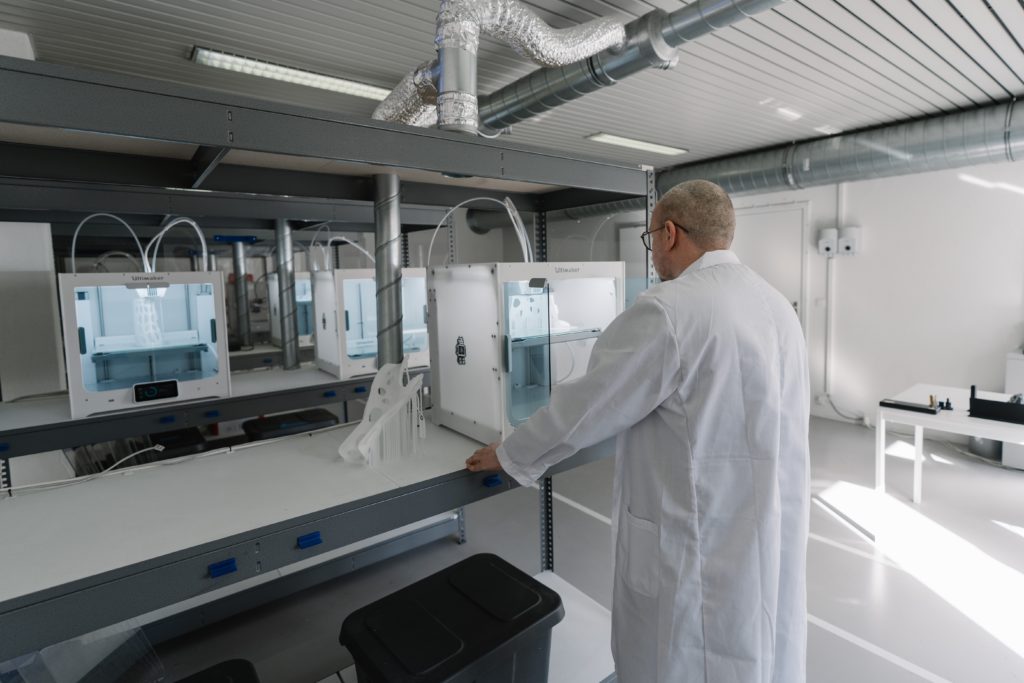
Understandably, companies that have been at the forefront of AM technology are protecting the intellectual property they’ve developed over the past years. They are also uniquely positioned to capitalize on this market.
“The intellectual proprietary argument” makes perfect sense; not to mention that proprietary systems are known for their ability to provide stability, repeatability and traceability that give industrial manufacturers confidence in the choices they perform.
The argument of companies that develop an open architecture system is to provide “a tool for more than just making parts, but also for making advances in the industry.”
This argument might certainly be more appealing not only for manufacturers but also for researchers, as such system enables more flexibility. Operators that use these systems have more freedom to modify, develop, and/or integrate hardware or software components.
“Ideally, the platform should be designed with openness in mind from the outset, with adequate physical space, available information about the configuration, and ability to access system data”, Open Additive explains. Furthermore, truly open additive manufacturing systems enable users to integrate their own proprietary technology, which has nothing to do with “open materials or parameters”.
Open configuration vs Closed configuration?
Let’s focus on powder-bed systems for example. Depending on the project that is being achieved, operators might need to achieve a certain performance with the laser(s), optics, build plate, powder deposition or sensors.
These features are usually configured prior to the sale and they cannot always be changed in AM systems with a closed architecture. To optimize the industrial manufacturing process, operators often tune machine settings by relying on simulation – which in the end, leads to greater control of the manufacturing process.
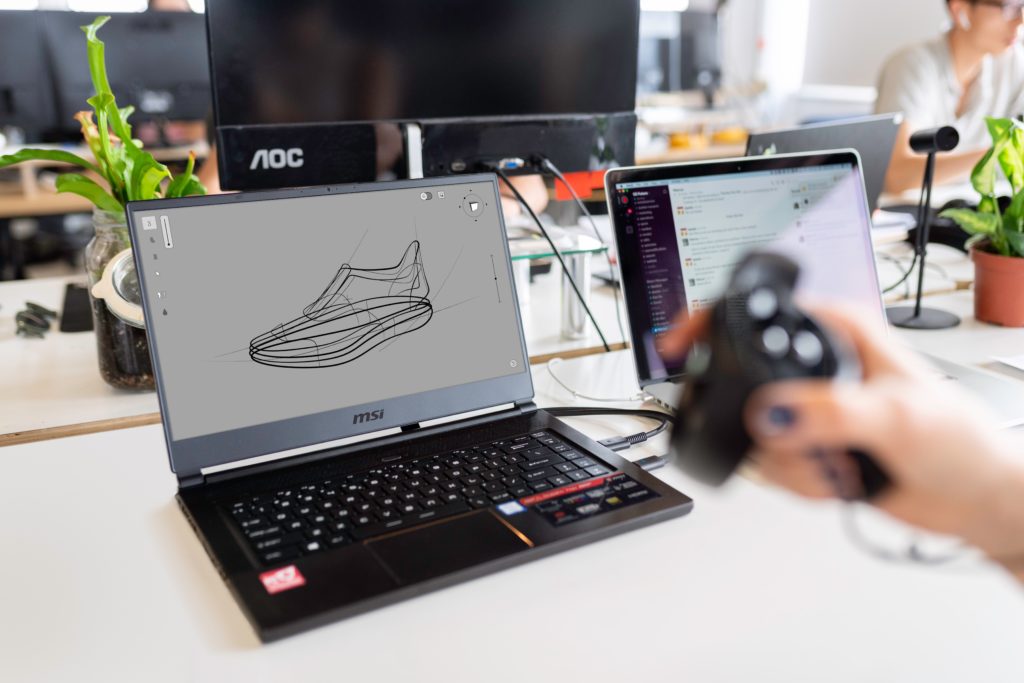
Truth is, be it in open AM systems or closed AM systems, the list of factors that can impact the quality of a final part is lengthy and these process variables must be strictly defined and controlled to enable a successful print each and every time, no matter the machine is.
However, one thing that anyone should appreciate in open AM systems is flexibility. Indeed, one cannot predict all the types of project that could be performed with a machine and the ability to adapt the machine before or after sale is definitely valuable.
This list of pros and cons is certainly not exhaustive as the debate is just emerging. However, the key stakeholder that is driving the conversation is the customer.
What does the customer want?
The client wants options. In a 2018 survey carried out by 3D printer manufacturer Essentium, 162 managers and executives from manufacturing companies across the world shared their current experiences, challenges and trends with 3D printing for production manufacturing.
The survey reveals that despite the optimism regarding the use of AM technology, some companies still face obstacles including the high cost of 3D printing materials (51%); expensive 3D printing hardware (38%); and current 3D printing technology does not scale (31%).
To overcome system inflexibility and to use the materials of their choice, manufacturers demand open ecosystems. 50% of respondents state they need high quality and affordable materials to meet the growing demand for industrial 3D printed parts. On the other hand, for 85% of manufacturers, industrial-scale additive manufacturing has the potential to increase revenue for their business, 22% said vendor lock-in has hampered needed flexibility.
Harshil Goel and Ty Pollak could not agree more as they strongly believe this is the time to accelerate the shift towards “Open” Metal Additive Systems.
Why are open systems and advanced software the future for the industry? – Insights from Harshil Goel and Ty Pollak
Harshil Goel, founder and CEO of Dyndrite™ Ty Pollak, CEO of Open Additive
While legacy business models have driven the growth of the industry to its current state, they are not suitable to propel and sustain the industry in today’s environment, in which dozens of vendors now compete, offering hundreds of hardware and software options to be optimized for a dizzying array of applications by a much more sophisticated user base. In this new climate, the model of closed, highly proprietary metal AM solutions limits the ultimate promise of AM to its end users—greater design freedom, lower costs, and better part quality. Thus, more open hardware and software solutions are key to the future growth of the industry.
The Primacy of Toolpath
At its most basic level, 3D printing comes down to tracing a path (e.g., a line or area) with an active tool (e.g., print head, laser, etc.) to join bits of matter into a solid piece. Today, the metal AM industry currently has more than 300 metal systems available, and most are closed and proprietary systems, with their own unique toolpath strategies which are generally difficult to understand, let alone control. This means that even if you can run the same process parameters across different vendors’ machines, it will too often produce markedly different parts from both a metallurgical and geometric standpoint, making standards and process control difficult and costly. Compare that to traditional machining tools that can run the same toolpath on different machines, resulting in similar parts. More open hardware/software systems which allow understanding and control of toolpath are thus critical to the acceleration of AM to improve quality and reduce costs.
Metal Additive Parts are way beyond “Lawn Mower Brackets”
We are stuck in a catch-22 situation: Machine systems vendors are developing new materials, and process parameters on a yearly basis while tying this development to their core intellectual property strategy. Machine systems manufacturers and their software/engineering teams are being pushed to the limit for developing these parameters. But they are using generic/representative parts to test and validate. However, end users are pushing the limits of these printers by producing ever more complex and sophisticated geometry harnessing the true mandate of 3D printing:- with geometry significantly more exotic than generic parts. End users view these new advanced parts as a core part of their intellectual property strategy, and thus are unwilling to share this geometry with anyone.
So now, the metal additive industry is stuck in a scenario where the intentions of the system vendors and their customers are at odds. Quite frankly, something has to give. The systems manufacturer needs better tools to develop better machines. The end user needs solutions that meet their evolving needs. An open-architecture is one of the key ways to get out of this predicament
Reducing Risk of Obsolescence
While open systems have been mostly beneficial to the R&D community thus far, they also enable producers, from major suppliers to the small machine shop, the opportunity to modify their system configuration as needs and technology evolve. As a result, risk of obsolescence decreases, and a wider range of future applications may be supported. This may spur organizations to commit to getting in the game sooner, knowing they can get started on developing expertise and use cases, but not get locked into existing capabilities. Thus, open-architecture systems can reduce one of the key barriers to entry in metal AM—the fear of making a major capital investment which locks down future capabilities in an industry that is rapidly evolving.
Towards Smarter Systems
A key element in the development of AM standards and improved process control strategies is the integration of various sensors and analytics to monitor, and even modify, the build process. To develop and make the most use of such capabilities, users must be able to access the raw and processed sensor data, understand any available analytics or create their own. This delivers the capability to inform the operator and control the machine to take actions based on this resulting information. Closed architectures place barriers to each of these steps, resulting in the dearth of useful process information available on today’s metal AM machines. On the contrary, open hardware and software systems are key to realizing the future state of the industry, in which metal AM platforms become smarter production tools.
Connecting the Digital Ecosystem
Today, metal AM machines are increasingly part of a digital ecosystem, which will only become ever more connected. While the machine’s software controls everything about the build process – parameters, process controls, resolution, speed, feeds, etc. – it needs to be integrated with other tools that allow pre-build setup and optimization, efficient utilization of available assets, collection and analysis of real-time and post-build data, etc. The machine thus needs to be able to accept and output a variety of format standards, compatible with different software tools used across this digital landscape. Software frameworks are thus needed which accept both open standards in addition to proprietary standards, and deliver greater flexibility for the user to control the machine through custom software plug-ins and APIs as needed. Open software frameworks with APIs that are accessible to people beyond in-house software developers are key to future growth.
Building Bridges Through Standards and new geometry kernels
“We can’t possibly have 30, 40 or 100 separate printer companies all with different competing standards.” Harshil Goel, at the Dyndrite Developer Council 2020 event in April.
All the participants agreed. Standards are a topic central to the future growth of the metal AM industry. Without standards working across the industry, the industry’s collective growth is held back, affecting each OEM individually. Dyndrite is working to address the issue of standards through the development of the core geometry kernel aimed to power the AM industry forward and develop critical integrated ecosystems that power digital manufacturing. In addition, it has also launched the Dyndrite Developer Council to work with industry vendors to develop standards that all can work to and help develop the Dyndrite kernel to meet collective needs. A key, critical task being handled by the Developer Council right now is the development of a standard toolpathing API to help solve the toolpathing issues described earlier. Members span the industry, from established companies such as 3D Systems, EOS, SLM, Renishaw and ANSYS, to newer players on the market including Open Additive, Aconity3D, and Impossible Objects. Interest in having more open systems is growing throughout the council, including SLM and EOS.
The Council is now up to 20 members and still growing as vendors take notice of the need for collaboration even while in competition. Alongside Dyndrite, Open Additive is a champion for accelerating innovation through more open solutions, and seeks to expand the development and application of AM standards to its metal AM machine control strategies as well as its multi-sensor data collection and analytics tools.
Concluding thoughts
Some AM companies have started acknowledging the need for open and independent machines. However, despite the predictions, the market does not seem ready to drop the intellectual proprietary paradigm. Right now, several factors play to open systems’ strengths. If Harshil Goel and Ty Pollak are correct, it’s only a matter of time before industries follow this move.
This feature was initially published in the September/October issue of 3D ADEPT Mag.
Remember, you can post job opportunities in the AM Industry on 3D ADEPT Media free of charge or look for a job via our job board. Make sure to follow us on our social networks and subscribe to our weekly newsletter : Facebook, Twitter, LinkedIn & Instagram ! If you want to be featured in the next issue of our digital magazine or if you hear a story that needs to be heard, make sure to send it to contact@3dadept.com