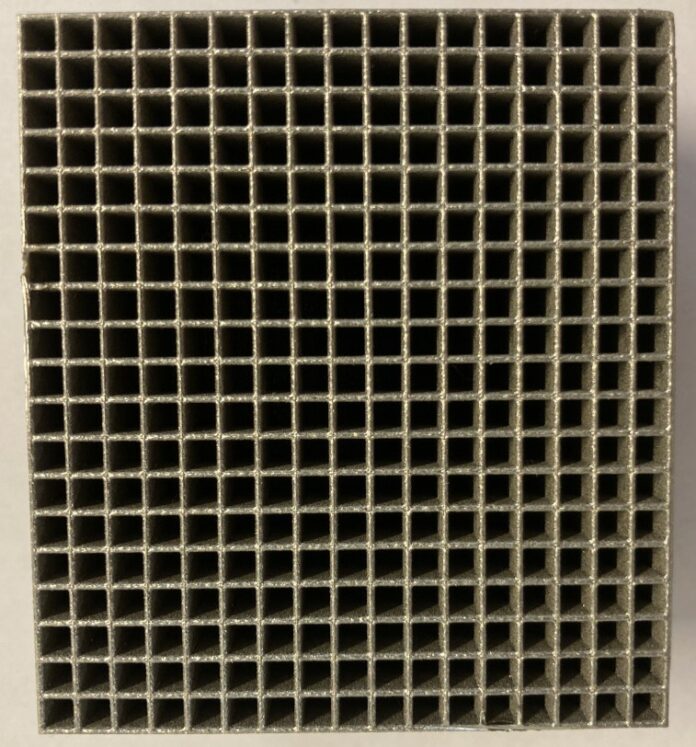
The first application of additive manufacturing in the nuclear industry was a 3D printed thimble plugging device fabricated by Westinghouse and installed at Exelon’s Byron Unit 1 nuclear plant. that was two years ago.
In the meantime, the industry did not rest on its laurels. Several conferences have been held to discuss the use of AM in this pivotal industry – 3D ADEPT Media even recently held a panel discussion on this topic with ORNL and Burloak Technologies – and several projects are currently in progress to advance this specific field of activity.
The truth is, and that’s what has been highlighted in the Additive Talks session dedicated to this topic, the nuclear industry is so much more conservative than other demanding industries and there are so many complexities to take into account to explore AM applications in this field.
Despite these complexities, Westinghouse seems to carve out a place in this niche market. The provider of advanced nuclear plant designs, nuclear fuel, service and maintenance as well as instrumentation and control systems has just installed its StrongHold® AM 3D-printed nuclear fuel debris filters in two Nordic Boiling Water Reactor (BWR) units – Olkiluoto 2 in Finland, and Oskarshamn 3 in Sweden – to further improve the plants’ operational reliability.
Created in close cooperation with plant operators Teollisuuden Voima Oyj (TVO) and OKG, the use of AM in the manufacture of the StrongHold AM filter gives the part enhanced capture features to prevent debris from entering the fuel assembly and potentially damaging the cladding. Without this protection and the use of this technology, unplanned and expensive outages could easily occur.
“We can now gain important practical experience in the use of 3D-printed metal products which will become an ever more important operational solution going forward. It is important to have a strong network of partners like Westinghouse who deploy additive manufacturing to drive enhanced capability,” said Arttu Knuutila, TVO Fuel Procurement Team Leader.
Westinghouse did not mention the metal 3D printing process leveraged for this production. Our guess is that the manufacturing team used a laser powder-bed system – as it’s the technology that was previously used for the first application and that seems to provide the most satisfying results so far.
“Fuel damages can force us to temporarily suspend operations, which affects security of supply and entails unnecessary costs,” said Andreas Roos, Oskarshamn 3 Plant Manager. “Reducing the risk of fuel damages is very positive for our business.”
“As the first 3D-printed fuel debris filter for insertion in a nuclear power plant, the StrongHold AM marks a major milestone in our effort to further improve the BWR fuel reliability by leveraging advances in manufacturing technology,” said Dr. Carina Önneby, Westinghouse Vice President EMEA Fuel Delivery.
Remember, you can post job opportunities in the AM Industry on 3D ADEPT Media free of charge or look for a job via our job board. Make sure to follow us on our social networks and subscribe to our weekly newsletter : Facebook, Twitter, LinkedIn & Instagram ! If you want to be featured in the next issue of our digital magazine or if you hear a story that needs to be heard, make sure to send it to contact@3dadept.com