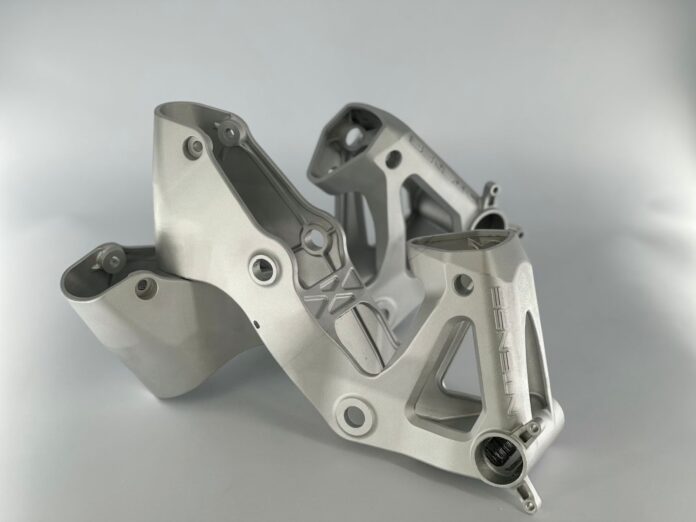
Founded in 1993, INTENSE helps to develop the geometry, suspension, and look of mountain bikes by producing high-end carbon fiber and aluminum rides. To reinforce its M1 downhill race bike, the downhill bike leader called upon the expertise of material producer Elementum3D and OEM TRUMPF.
As a designer, artist, and craftsman with a hands-on approach, INTENSE founder and CEO Jeff Steber works and ‘thinks’ in aluminum, therefore he is enthusiastic about integrating AM into bike frame and part production. “We say INTENSE merges artistry and engineering, and I am no longer limited to metal sheets and tubes. I have the freedom to create almost any shape I want,” he adds.
The company shared that to reconceive the M1 downhill bike, a model that has edged other riders and their sponsors off the winners’ podium since the mid-1990s, Steber’s team planned to design and produce the M1’s backbone from one piece of 6061 Aluminum. The part and the material are critical to optimizing the bike’s suspension performance. The new design incorporates internal ribbing to make it stronger and lighter; but this made it impossible to create using traditional machining techniques.
That’s where AM comes into play
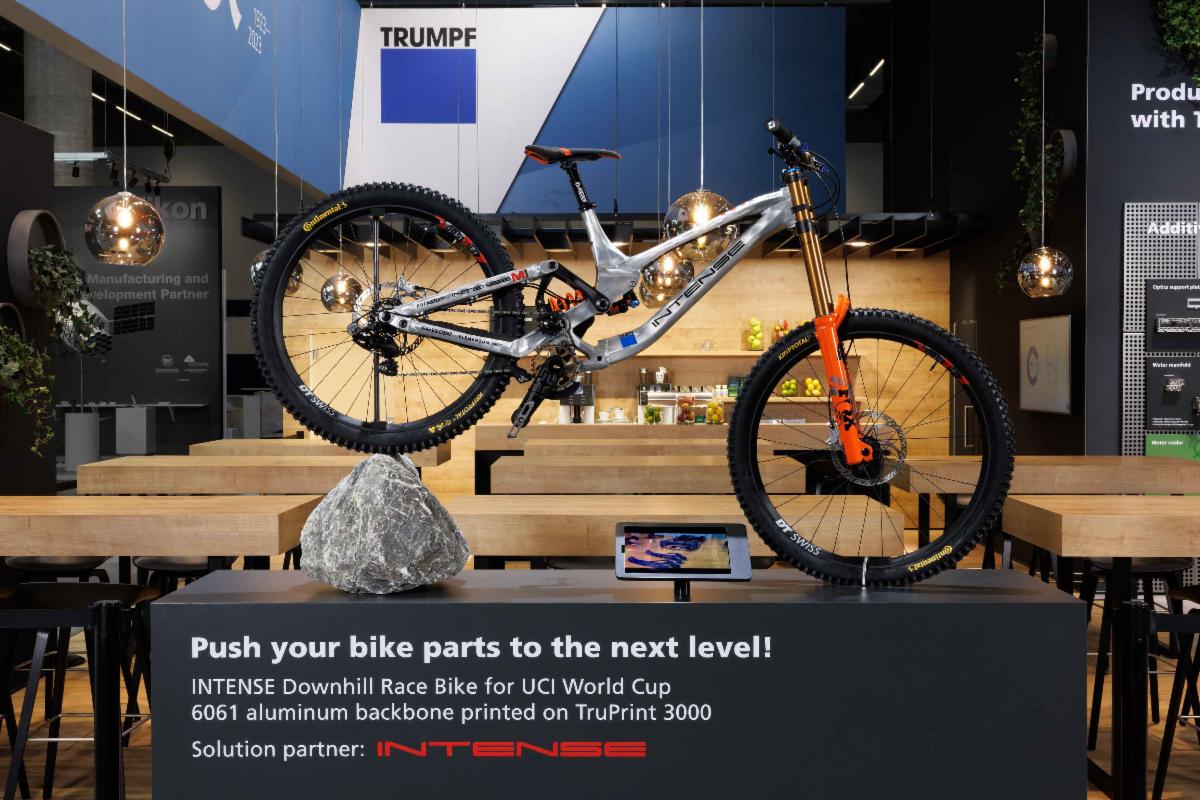
TRUMPF who has already a solid experience in the bike industry, was able to print the bike parts using weldable 6061 aluminum – Elementum 3D’s A6061-RAM2 – the same alloy INTENSE already used for its aluminum frames.
The first backbone designs were not ideal for printing, so TRUMPF advised INTENSE engineers on removing low-angle overhangs to improve printability. TRUMPF’s updated build processor, “TruTops Print,” increased downskin printability from 45° to 25° so the backbone printed with much less overhang-supporting material, reducing the chance for errors, material use, and post-processing effort.
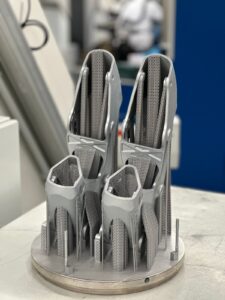
TRUMPF contacted Elementum 3D for delivery of its A6061-RAM2 feedstock material. Delivery and finalizing technical details were completed faster than expected, allowing TRUMPF to immediately confirm the powder performed well with their existing infrastructure. It convinced INTENSE A6061-RAM2 was well-suited for in-house bike frame prototyping because it is easily welded and heat-treated with other frame parts, including thin-wall tubing.
From the first test build, INTENSE appreciated A6061-RAM2’s weldability, finding it exactly like working with billet-machined 6061, with no porosity or contamination issues. TRUMPF liked the predictable processability, which enabled developing a working print parameter in two weeks and required printing just two DOEs (designs of experiments) to reach the material’s expected relative density value.
Both companies found A6061-RAM2 ideal for this project, particularly given the printed parts’ surface finish and accuracy. After the backbone was welded to the frame it was nearly impossible to determine which parts were printed, machined, or forged, a press release reads.
Remember, you can post job opportunities in the AM Industry on 3D ADEPT Media for free or look for a job via our job board. Make sure to follow us on our social networks and subscribe to our weekly newsletter: Facebook, Twitter, LinkedIn & Instagram ! If you want to be featured in the next issue of our digital magazine or if you hear a story that needs to be heard, make sure you send it to contact@3dadept.com