Even though (additive manufacturing) AM is a driven factor of the next industrial revolution, work still needs to be done to reach a full-production ready technology.
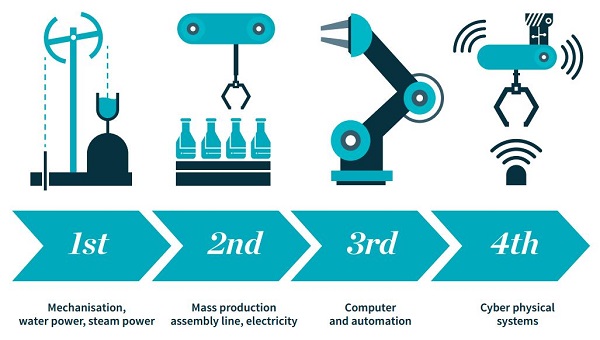
The issue tackled by researchers of Tennessee Technological University and the National Institute of Standards and Technology (NIST) shows that “lack of data manageability through information management systems, traceability to promote product producibility, process repeatability and part-to-part reproducibility” on the one hand; on the other hand the “accountability through mature certification and qualification methodologies” are the main challenges faced by specialists of the sector.
The recommended model could to a certain extent form a standard for 3D printed metal parts and aid additive manufacturing through the certification process.
The truth is that numerous projects implement industrial 3D printing for the production line, the goal being to succeed to integrate and mix both traditional and modern methods of manufacturing techniques.
How to solve the repeatability problem?
The repeatability problem often occurs while using a 3D printer. The miracle solution for 3D printing techniques like DMLS and EBM would be to create complex and unique metal parts.
However, the big issue now is to ensure the repeatability of this solution to allow customers to receive identical parts from batch to batch.
NIST and TTU’s repeatability solution consists in integrating more precision into the metal 3D printing process. The three different hypothesis’ testing show that researchers add more data to the process each time.
The basic test
A scenario in which a customer asks for a metal 3D printed part from one company providing electron beam melting (EBM) and another providing direct metal laser sintering (DMLS) was set up.
The only specifications in the test are the object’s .stl file, and the material to be used – the titanium /aluminum alloy Ti6Al4V.
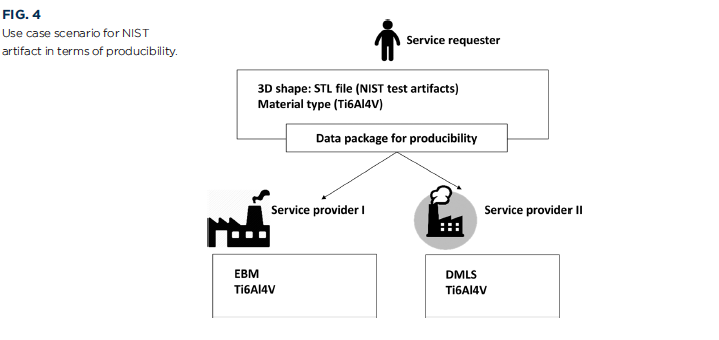
According to the resulting 3D prints, there are inconsistencies between one another, a consequence of service providers producing the parts using different processes and plans. These inconsistencies can result for instance from the positioning of supports, or the way the model is sliced and the scan strategy used by different 3D printers.
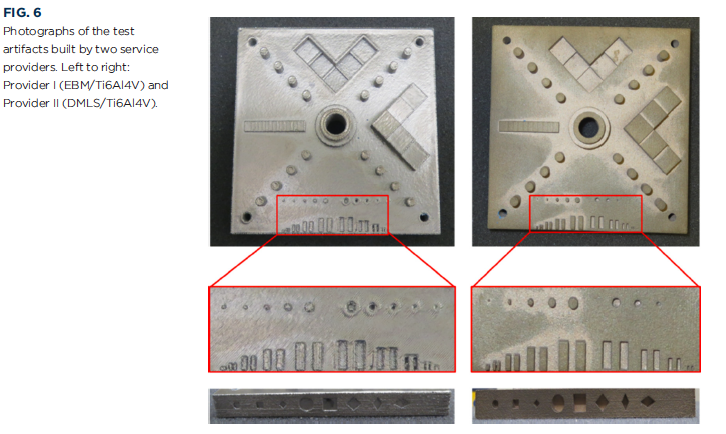
The second test
Once support and slice information are integrated to the data package alongside the base .stl file, the user can request the same parts from 3 different suppliers of EBM 3D printing.
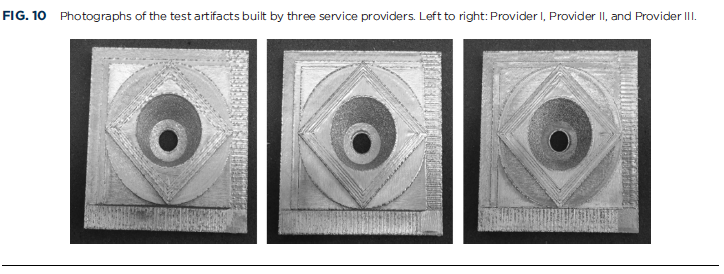
The final case study
Specifications such as post-process information, test plans, and average surface roughness are given alongside the previous package.
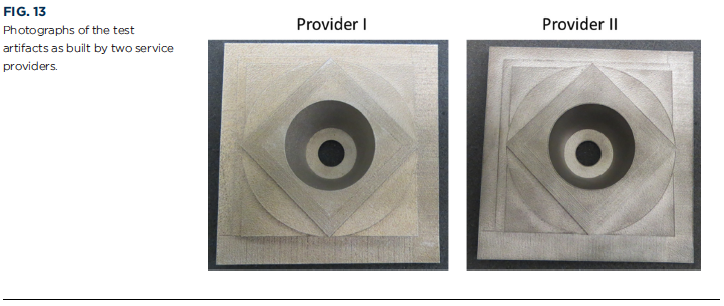
According to experts, “the established data packages and digital thread provide a foundation on which future validation and conformance methodologies can be built.”
For further information about 3D Printing, follow us on our social networks!
//pagead2.googlesyndication.com/pagead/js/adsbygoogle.js
(adsbygoogle = window.adsbygoogle || []).push({});