Manufacturing technologies can be a true game changer in the production of parts if all components of the manufacturing process are used properly. Materials play a key role in this revolution: producers must not only find the appropriate material for their application; they also need to have a 3D printer that can process it.
The challenge is big as all types of materials are involved: metals, polymers, ceramics, concrete and biological cells. This article aims to observe the growing use of polymers in additive manufacturing. A key focus will be made on PEAK materials.
The use of PEAK materials
There are two main categories of materials in the family of high-performance thermoplastics: polyaryletherketone (PAEK) and polyetherimide (PEI) better known under the brand name ULTEM.
Mainly used in the form of poly-ether-ether- ketone (PEEK) and poly-ether-ketone-ketone (PEKK), PEAK materials have a unique set of mechanical and thermal properties that are compatible with powder bed melting processes such as laser sintering, or with extrusion processes such as filament melting.
According to Martin Court from Victrex, the key for processing PAEK is to be able to get the polymer over its high melt temperature of 300-400C, and carefully control cooling with heated chambers and process control.
Speaking of PEKK materials in particular, the executive director at Victrex explains:
“PEEK differs from other polymers in that it is one of the highest performing thermoplastics available. Its excellent mechanical and chemical characteristics mean that it uniquely supports
a combination of multiple requirements. For example, the versatile light weight, high strength PEEK polymer provides high resistance to wear, temperature, fatigue and aggressive fluids/chemicals.”
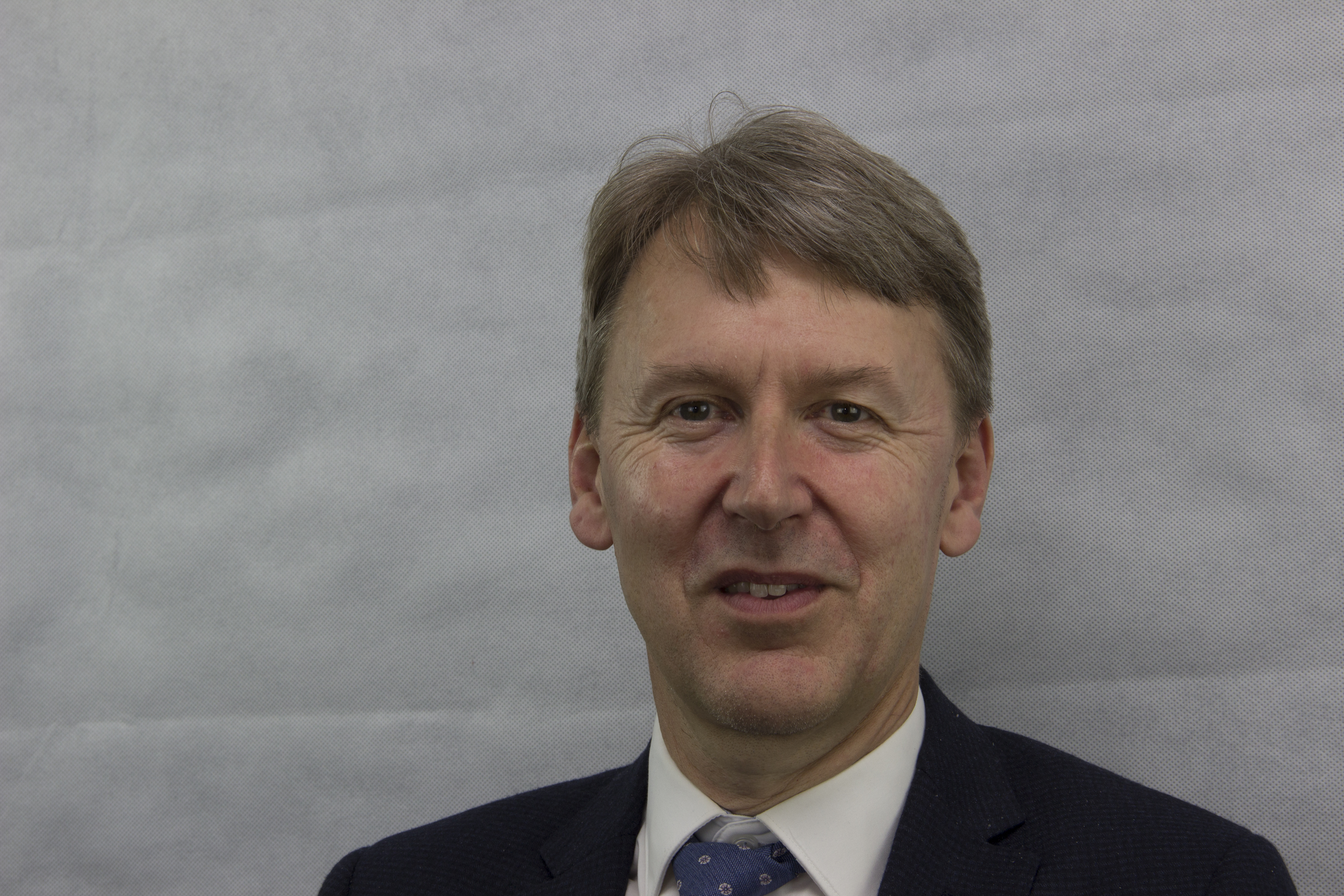
Indeed, given their mechanical properties, PAEK materials are very coveted and are mostly used in demanding applications for the automotive, the aerospace or even the medical industries.
When asked about the importance of polymers for these industries, Harold van Melick, R&D Director, DSM Additive Manufacturing said:
“Polymeric materials are widely used in many industries (maybe all industries). Although many applications are cost-driven mass-manufacturing (e.g. injection molding), in many cases the properties of the polymers are decisive in the choice of materials. For instance, it’s impossible to make a connector, a circuit breaker, a tyre, a flexible CVJ boot out of metals. This quest for functionality will drive designers to make applications out of polymers in many industries. The most obvious ones are medical/dental, transportation/automotive, electronics and sports.”
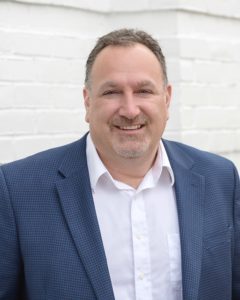
Matt Torosian also lays emphasis on the need to combine the economic point of view with technical requirements. According to the Director of Product Management for Materials at Jabil, OEMs have applications that they feel are a good commercial fit for polymer AM. The issue is, the material set available does not meet the physical requirements. “They have aligned on the DfAM benefits and quantities needed and cost model benefits but if the final part cannot meet the engineering requirements, the application will have to be redesigned into conventional processes where the material set is more aligned with the requirements.
If OEMs and all participants up and down the AM Supply Chain want to satisfy those customer requirements, we have to develop Materials, Process and Machines to meet those requirements. Leave one of those three critical pieces out, and you don’t have an ecosystem that can thrive”, adds Matt Torosian.
Even though we understand the importance of using polymeric materials, the reality of the market shows that metal AM remains the technology that pushes the industry forward the most.
How can this situation be explained?
Unlike polymer 3D printing, metal Additive Manufacturing is more mature when it comes to deliver desired mechanical properties that one can obtain using conventional manufacturing techniques.
For DSM, predictability of part properties and performance are some factors that foster the adoption of metal 3D printing within industries. However, Harold van Melick explains that all applications cannot only be achieved using metallic powders. Various reasons can explain the need for plastic materials: weight, flexibility, accuracy, versatility of properties. All of these reasons drive investments in the development of AM technologies that can deliver functional parts and materials that can provide these property profiles.
Victrex on its side points out the technical aspect, while comparing metallic powders and PEAK materials: “compared to metals, PEEK-based materials are very light in weight, easily shaped, resistant to corrosion and can have considerably higher specific strength (strength per unit weight). In addition to that, potential benefits of using members of the PAEK family of polymers for AM could also include in the future:
– improved economics through elimination of machining waste, improved refresh rates in powder bed fusion (PBF), and improved material utilisation in filament fusion (FF) or
– patient customized implants and improved outcomes through new features and better fit.”
Jabil on its side also mentions an interesting point: there is a limited number of players that can address the latent demand of the polymer 3D printing market on the one hand, on the other hand, an already existing market for metal 3D printing that contributes to the growth of the industry: “Polymer materials in the Additive Manufacturing market, especially powders for SLS and HSS are restrained by a lack of participants. As new applications have emerged, the number of Engineered Materials available has not significantly changed. Beyond the resin producers that offer 3-10 grades of SLS powders each, only a handful of producers globally produce reinforced, custom engineered powder products for SLS. If you compare that to the conventional polymer process market, injection molding and extrusion, there are literally hundreds of compounders that fill that need in the AM market. Therefore, companies are investing to fill that gap in the fundamental building block of functional parts i.e. polymer materials. In relation to metals, the number of materials involved in polymer AM is much fewer. Also, in metals, there is an established market for powdered metals.”
There is a clear need for plastic materials that integrate an array of mechanical, thermal and chemical properties that can meet the needs of the industry. The portfolio of polymer materials in AM is still quite limited; about 1% of what is available for injection molding is currently exploited. We therefore understand the increasing investments that can be made to deliver appropriate polymeric materials and technologies.
Let’s speak about the thermoplastic PEEK
In the plastics industry, PEEK is regarded as one of the top materials of the pyramid and this rank is mainly due to both its properties and cost. The engineering material is recognized for its chemical resistance, high temperature as well as flammability properties. Using this material in AM enables to deliver these properties in addition to usual advantages of polymers.
However, it should be noted that there is an array of polymers that are made available on the market: polyamide, polyester, PPA, PPS and more. Each of them has its own strengths and weaknesses. The set of requirements that an application must meet will determine the choice of material that must be used.
A huge potential for the medical sector
3D printing allows the production of custom-made implants and facilitates communication between participants in the supply chain. This new way of working drastically transforms preoperative planning and surgery. PEEK-based implants are the ones that are mostly used because of the benefits they can bring to patients. Current researches on this material and its applications include dental, knee, spinal and trauma implants.
Among the solutions that are currently delivered in the medical field, there is for example, PEEK-OPTIMA polymer from Invibio Biomaterial Solutions, “Victrex’s medical business, enables artefact-free monitoring and assessment of patient healing sites. Additionally, PEEK has a modulus closer to bone which, compared with metal, which helps minimize stress shielding and stimulate bone on growth.”
Although additive manufacturing is still at its early stage in the medical sector, there is every reason to believe that this technology can be a game changer in terms of speed and accuracy in the manufacturing of implants.
The few issues that need to be tackled
Despite the strong interest from industrials in PEAK materials, a number of issues still need to be tackled to achieve a wide range of applications. Existing and new entrants should work on how new materials can fit with new processes and new machines.
For Matt Torosian from JABIL, this means working with independent suppliers: “the Polymer materials market needs more entrants that are open and independent of machine manufacturers and the entire machine manufacturers’ supply chain. When you link the material supplier to the machine supplier, you limit the ability for OEMs and Processors to optimize and innovate both the material and the process. This in turn limits innovation at the machine level because they are not pushed to develop new machine technology to fit an ever-changing materials and process landscape. If you look at this like conventional processes, the independence of compounders, resin producers, mold makers and machine producers has propelled the technology to its current state.
The four critical aspects of the process continuously expand the envelope of what can be done, pushing each other to innovate and to be able to use a unique material, complex tools or machine technology that exploit some attributes previously not possible by the current state of the technology.
Our feeling is, the market always wins when it is not restricted. Open platforms and markets should be the focus of the AM ecosystem in order to reach the maximum level of innovation and adoption.”
Unlike Jabil, DSM presents a more holistic approach to develop the market. For the producer of materials, the key to develop this part of the market lies in “the way one translates the application requirements into material properties (that determines material selection) and a 3D printing technology that will be able to convert those materials.”
Standardization of materials
To be part of the industrial world, additive manufacturing technologies and materials will have to meet application requirements. From design to production, standards are essential because they enable the various stakeholders to speak the same “language”. Furthermore, they ensure a good quality control of the final product.
International standards organizations have been collaborating for the development of additive manufacturing standards. Although several standards have already been published, there is still a long way to go for materials. The variety of technologies and players does not make things easier but there is no doubt that the future of polymer materials for AM partly depends on this standardization process.
Lastly, enabling high-quality standardization also means strengthening the image of these technologies and giving them more credit. Finally, it means accelerating their integration and strengthening the competitiveness of companies.
Initially published on September 13, 2019. You can now post free of charge job opportunities in the AM Industry on 3D ADEPT Media. For further information about 3D Printing, follow us on our social networks and subscribe to our newsletter! Would you like to be featured in the next issue of our digital magazine? Send us an email at contact@3dadept.com