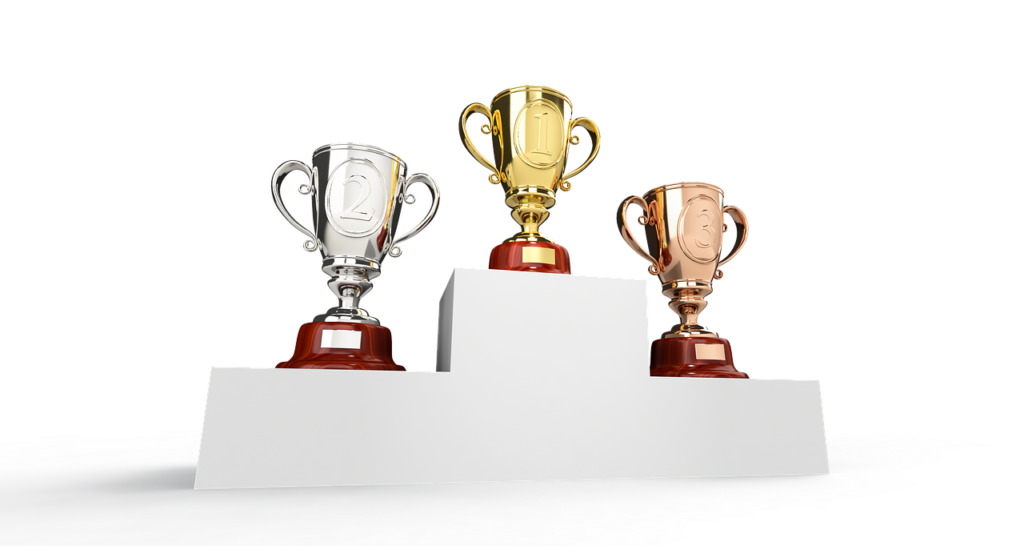
Teams form several technical universities spanning 32 countries have proposed pioneering solutions for fused filament fabrication (FFF), a key part of the high-end 3D printing process. The winning team form the Technical University of Munich (TUM) demonstrated that 3D printed parts can decisively match the performance and quality standards of conventional injection moulded parts, through combined optimisation of materials, hardware, and processes.
For the challenge, all teams were provided with a spool of Radel® polyphenylsulfone (PPSU) AM filament. They were then tasked to replicate an ASTM D638 Type V size tensile bar in the z-axis and a wavy-shaped pressure pipe, a difficult shape for injection molding. The competition emphasised on aspects of maximum dimensional accuracy, mechanical performance (including burst pressure tests), translucency, and of course, process creativity.
The Gekko Performance team from TUM achieved a 100 percent z-axis strength in the Type V size tensile bar and its wavy pipe showed overall dimensional accuracy, surface uniformity, and a remarkable mechanical performance by enduring a burst pressure test of 1,400 psi (96.5 bar) for two hours. Two other teams from Gent University, Belgium were awarded second and third places in the competition, due to their equally novel approach. All three teams were able to bring high performance prototypes in terms of tensile modulus, tensile strength, and ductility. The winning teams selected by an international jury received ten, five and three thousand euros respectively, to be reinvested in academic, societal or entrepreneurial activities.
About the event:
The Additive Manufacturing cup is an initiative to bring high-performance 3D printing material in the hands of talented design and engineering students with a passion for exploring ‘the art of the possible’ for this disruptive, revolutionary technology. The competition is organised by Solvay, an an advanced materials and specialty chemicals company, committed to developing chemistry that addresses key societal challenges.
About the host:
Solvay has taken a lead in the rapidly evolving AM market and offers a growing range of filaments for applications in different printing and fusion processes. Besides Radel® PPSU, the current portfolio also comprises neat and carbon filled KetaSpire® polyetheretherketone (PEEK) AM filaments, including medical-grade formulations for limited-contact healthcare applications. Moreover, these advanced filaments have recently been added to the Digimat® simulation software database of e-Xstream engineering, allowing customers to predict and optimise their parts in order ‘to print right the first time.’