While it is still at its early stages, distributed additive manufacturing is set to be a pivotal part of the manufacturing landscape. Organizations that have explored this route so far have kept highlighting the lack of reliable solutions that could couple end-to-end data security with data traceability. As I used to say, the challenge is even bigger for those who operate at a “glocal level” (both global and local levels).
Well, a group of organizations has just achieved a major step towards enabling a secure and transparent distributed additive manufacturing (AM) supply-chain model. A group made up of Assembrix , Boeing, EOS, 3T Additive Manufacturing, and BEAMIT. Together they have been able to establish a fully controlled 3D printing solution remotely connected to EOS 3D printers, directly.
At the heart of this work, there is cloud-based platform developed by Assembrix, which enables to virtualize industrial 3D printing – enabling this way a simpler, secured and more efficient production process. The Virtual Manufacturing System (VMS) platform oversees the entire additive manufacturing thread from the initial part model to the verified physical part, and beyond.
The solution also incorporates technology from Boeing, and a blockchain, seamlessly integrated with EOS industrial 3D printers.
In this specific case, building a secure digital manufacturing environment for additive manufacturing, absolutely required the security enabled by the blockchain, as well as a tight integration ‘on-machine’ between Assembrix and EOS software.
Assembrix was one of the first members of the EOS Developer Network (EDN), and together with BEAMIT and 3T Additive Manufacturing, has leveraged the capabilities of the EOS software platform through the EOSPRINT and EOSCONNECT APIs to create this end-to-end solution for controlled distributed manufacturing.
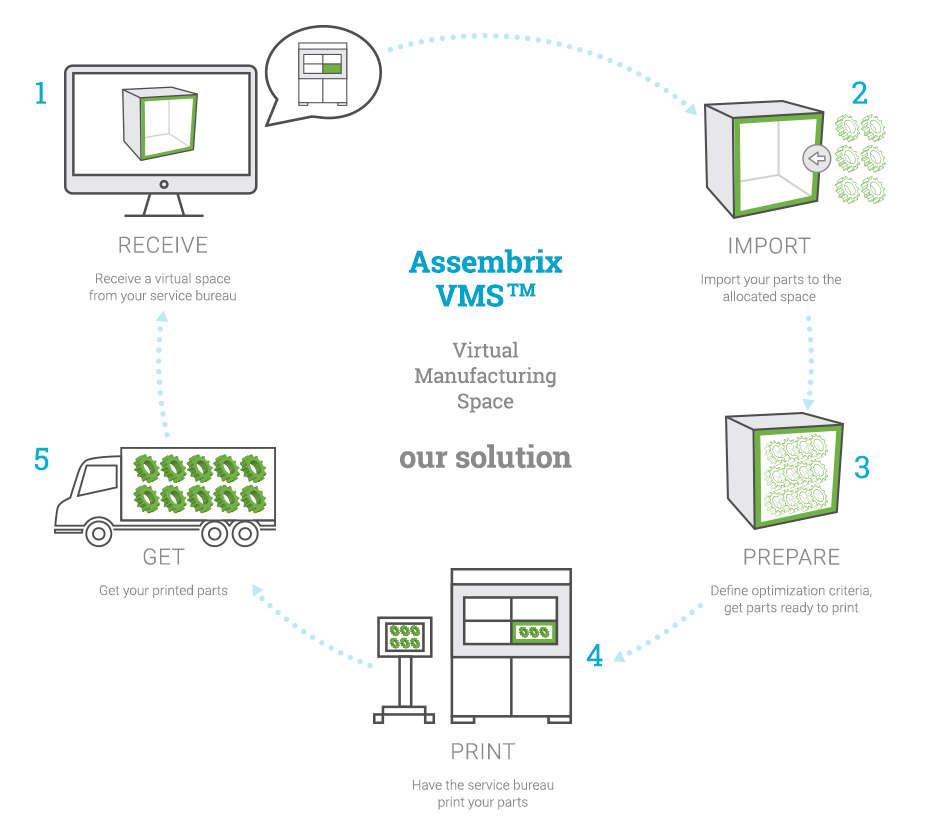
Dan Johns, CEO 3T Additive Manufacturing and CTO BEAMIT Group, says “Being able to securely connect the customer directly to the AM machine, anywhere in the world, has been a long-standing vision within the community. The end-to-end digital integration of a supply chain transforms the business model of traditional manufacturing to a scalable and flexible network of virtual warehouses for on-demand supply, with security and quality embedded into the system. The ability to digitize the complete value chain with our strategic partner Sandvik, means that BEAMIT Group is now able to offer the next generation of advanced manufacturing services.”
It’s certainly due to the confidentiality reasons that surround the aerospace industry but no information has been shared regarding the number of parts that were produced including when, where, and how. However, the good news is that other organizations across the world can now benefit from this solution. Therefore, they will be able to benefit from three main advantages: secured production, real-time monitoring, as well as data collection & monitoring.
This means that jobs could now be securely assigned to individual machines within a manufacturer, with IP fully protected and an auditable transaction trail. Customers could make sure excess parts are not produced, monitor job progress in real-time and protect their design instructions. On the other hand, data from the machine can be monitored to ensure it is within the parameters defined by the customer for the job. This may include machine bay humidity, temperature, print speed or cooling, for example. All factors that can impact the performance and final quality of a part.
Nel Zierhut, 3T Additive Manufacturing says “This collaboration has produced an exciting demonstration that will significantly contribute to an increasing level of confidence for companies that want to make worldwide digital manufacturing and serial production a reality, protecting IP and ensuring the highest component quality.”