Velo 3D has launched Sapphire System, a laser powder bed metal 3D printing system intended for high volume manufacturing. The manufacturer of metal AM systems and physical simulation-based print preparation software, will debut the Sapphire System at IMTS in Chicago this September.
By unveiling this system, the company offers the market a 3 in 1 solution made up of the Sapphire™ system, Flow™ print preparation software, as well as Intelligent Fusion™ technology.
The solution aims to tackle challenges related to product design limitations, part-to-part consistency, process control and cost-effective manufacturing.
Sapphire System
The metal 3D printing system can produce complex geometries such as designs with overhangs that are less than five degrees and large inner diameters without supports.
The 3D printer integrates in-situ process metrology that allows for closed loop melt pool control. In order to increase productivity, the Sapphire system contains a module that enables automated change-over with offline unpacking.
Flow Print Preparation Software
Support generation, process selection, slicing and simulation of part designs are some of the tools that have been incorporated in the software to validate execution feasibility before the build.
“Geometrical feature-driven processing enables low angles below 5 degrees. In addition, deformation correction technology enables the user to produce parts without the need for iterations, achieving a first print success rate of up to 90 percent. Flow minimizes the need for supports, reducing typical support volume by 3-5 times, which removes or reduces the laborious post processing necessary with conventional approaches.”
Intelligent Fusion Technology
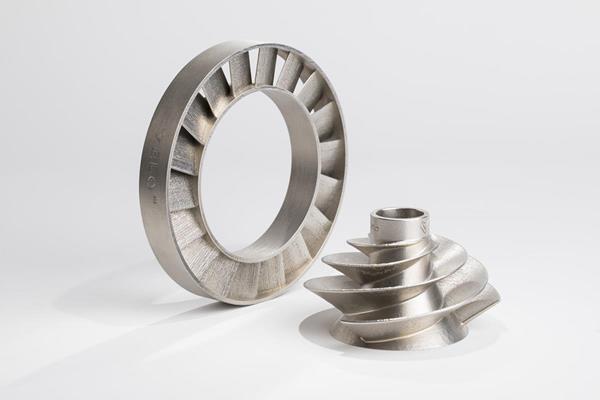
Such technology combines thermal process simulation, print prediction, and closed-loop control during print execution.
Benny Buller, founder and CEO of Velo3D explained that, four years ago, their approach relies on creating deep insights in physics fundamentals, enabled by research, characterizing and understanding of core mechanisms, developing intelligent process control through software simulation and in-situ metrology.
Original equipment manufacturers (OEMs) and manufacturing service providers constitute the main users of the company’s systems.
For further information about 3D Printing, follow us on our social networks and subscribe to our newsletter
Would you like to subscribe to 3D Adept Mag? Would you like to be featured in the next issue of our digital magazine? Send us an email at contact@3dadept.com
//pagead2.googlesyndication.com/pagead/js/adsbygoogle.js
(adsbygoogle = window.adsbygoogle || []).push({});