For twenty years, rpm GmbH, short for rapid product manufacturing GmbH, has been committed to producing parts with the use of rapid prototyping methods and traditional model-making techniques. Over time, the Germany-based company has invested in additive manufacturing technologies.
The company’s portfolio already includes resin 3D printing technologies from Carbon and early at the beginning of this month, the products manufacturer invests in two new Farsoon Polymer Laser Sintering Machines. The Farsoon AM systems will replace the first two AM machines that enabled rpm to debut its journey in the AM industry.
rpm and Farsoon Europe have been exchanging on this acquisition for more than a year. It was important for rpm to receive positive feedback from various tests such as surface quality tests, the production speed and the larger build chamber. Furthermore, the contract manufacturer had to analyze the machines flexibility, adjustable parameters, selection and mix of powders as well as the facility to control production.
“rpm deeply evaluated Farsoon for more than a year”, comments Dr. Dirk Simon, Managing Director for Farsoon Europe, “and I’m proud that such a highly experienced 3D-part producer could duplicate the performance of 4 laser sintering machines with 2 new Farsoon machines”
Adding Farsoon Polymer Laser Sintering Machines to its production capacity will allow for the fabrication of prototypes and small series parts (10,000 units). Furthermore, each 3D printer has its purpose: The Farsoon SS403 is a good candidate for stable, rapid production of series parts. The machine produces “ready-to-use” parts and faster prototype iterations whereas the HT403 brings high temperature shielding and thermal controls, two features required to process high-performance materials for the automotive and logistics industries.
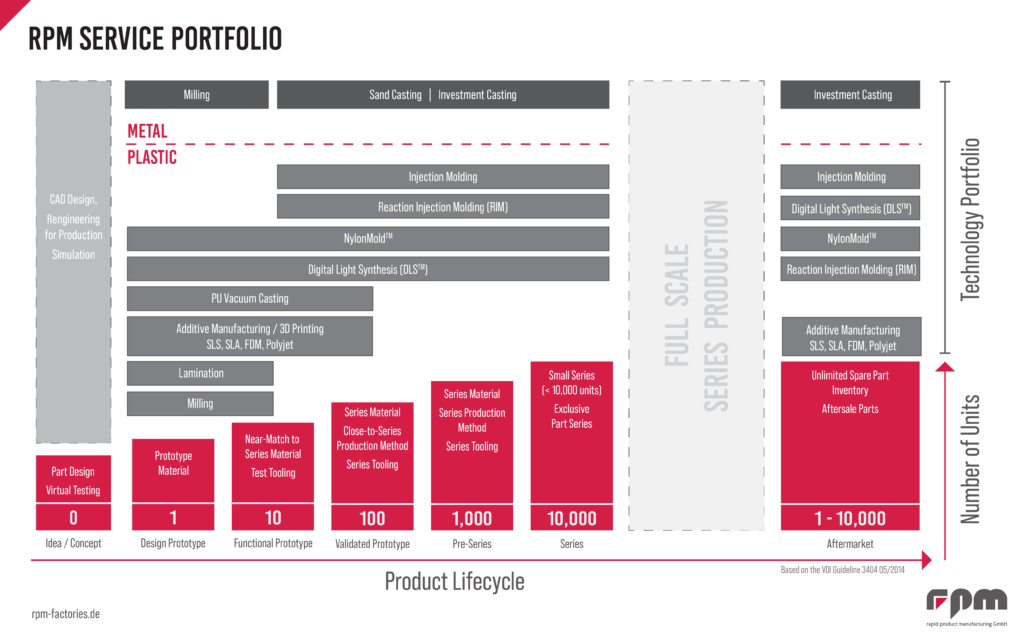
“When we started rpm in 1997, we were focused almost exclusively on rapid product development using the SLS (Selective Laser Sintering) additive manufacturing technology. Over the years, we have moved further down the production chain so that now rpm is a single contact point for bringing plastic parts from idea to reality. The new Farsoon machines are online, calibrated and have begun printing small series parts”, states Dr. Jörg Gerken, Technical Director, rpm.
rpm’s older machines will be sent to the Laser Center in Hannover (LZH e.V.). The center will leverage the machines for training and replacement parts for older machines. This symbolic donation means a lot to rpm’s two founding partners, Dr. Jörg Gerken and Dr. Klaus Kreutzburg who both learned and trained at the LZH in the 1990s.
Remember, you can post free of charge job opportunities in the AM Industry on 3D ADEPT Media or look for a job via our job board. Make sure to follow us on our social networks and subscribe to our weekly newsletter : Facebook, Twitter, LinkedIn & Instagram ! If you want to be featured in the next issue of our digital magazine or if you hear a story that needs to be heard, make sure to send it to contact@3dadept.com