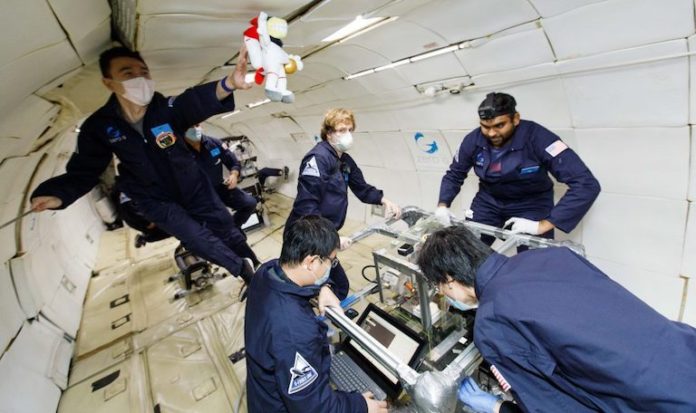
Any research that leads to productive results in a zero-gravity environment can positively affect astronauts’ experience in Aeronautics and Space as the state or condition of weightlessness is predominant in such environment.
A recent research conducted by a research team from Iowa State University College of Engineering occurred in a zero-gravity environment. It ambitioned to 3D print a conductive circuit pattern in microgravity.
“We want to help NASA develop a platform that can greatly expand the materials and devices they can make in space,” Shan Jiang, assistant professor in materials science and engineering (MSE) said. In this vein, the research team developed a novel 3D printing process that wears an acronym that outlines their goals for this vertical industry: NINJAS – No-Gravity INk Jet Printing for Aeronautics and Space.
“The main goal of our experiment was to print a conductive circuit pattern in microgravity,” said Hantang Qin, assistant professor in industrial and manufacturing systems engineering (IMSE) who led the research. “We tested multiple types of ink with different material properties, such as density, surface tension and permittivity, while pinpointing the optimal operating conditions, including voltage, pulse frequency and nozzle orientation.”
With the help of NASA’s Flight Opportunities program, the team has developed brand new ways to synthesize silver and barium titanate inks (patent pending) and successfully print those inks to a glass substrate during the test flight. These particular inks are desirable for their applications in printing electronic devices, including general circuitry, capacitors and humidity sensors, according to Qin and Jiang. The team hopes that the findings from this research might improve the manufacturing of flexible sensors, soft robotics, circuit boards, semiconductors and other micro-scale electronic devices on earth as well as in space.
Qin said vibrations from the aircraft transferring to the 3D printer onboard was one of the biggest challenges the team faced. Vibrations from the aircraft engine coupled with the turbulence caused disruptions to the nozzle of the 3D printer while in operation. The team attempted to recreate these vibrations in the months leading up to the test flight by operating the printer while driving a car around Ames. Qin said the team was able overcome the obstacles that the vibrations presented during the test flight by adjusting factors such as the voltage of the electric field and distance from the printer nozzle to the glass substrate. Adjusting the pulse frequency also alleviated some of the vibration-induced issues.
Adapting to the physical sensation of a zero-gravity environment was another challenge the researchers faced. Qin said motion sickness medicine helped them to deal with the nausea caused by the zero-gravity environment and he compared the sensation to “operating a printer while literally jumping off a 30,000-foot building.” Matthew Marander, a Ph.D. student in MSE, said the sensation was like being in a pool, but with less to push against.
“The zero-gravity environment wasn’t even that difficult to adjust to the feeling of,” said Marander. “What I felt was more difficult to deal with was the feeling of rapid transition between hyper-gravity, the normal gravity and zero-gravity. Switching between all of them so quickly can feel a little bit disorienting.”
The team plans to further improve their 3D printing technique and is in the process of applying for another parabolic flight test in May 2022.
Remember, you can post job opportunities in the AM Industry on 3D ADEPT Media free of charge or look for a job via our job board. Make sure to follow us on our social networks and subscribe to our weekly newsletter : Facebook, Twitter, LinkedIn & Instagram ! If you want to be featured in the next issue of our digital magazine or if you hear a story that needs to be heard, make sure to send it to contact@3dadept.com